設備の保全計画作成における課題
前回のコラムでは、製造現場の設備・装置の点検・保全業務の課題について取り上げましたが、今回は「保全計画の作成」に焦点を当てたいと思います。
人員も予算も潤沢に確保できる状況なら、定期的にメンテナンスを行うことで設備を維持することができました。しかし現在は慢性的な人手不足に加えてコスト削減要求も厳しさを増しています。保全計画の作成業務には、どのような問題があるのでしょうか。
あるお客様(C社様)では、保全計画の担当者が月次の定期修理作業一覧をExcel*1で作り、グループ内ですり合わせた後、他のグループ間との調整をして計画を確定させていました。作業を選別するにあたって考慮すべき条件が多く、人手を要しています。加えて、広大な工場内の設備を複数のグループが分担し、各グループ内でさらに複数の作業者が担当エリアを持っており、保全対象の設備や部品に、人が紐づいていました。
また、工場内のさまざまな設備と構成する部品には、例えば10年といった「定格寿命※」が設定されていますが、ほとんどの場合メーカーは定格寿命にある程度の安全係数をとっています。このため製造現場では、「本当はあと5年使える部品を、10年目で交換しなければならない」ことになります。当然、交換にはコストがかかり、場合によっては生産ラインも止めなければなりません。
C社様は、定格寿命ギリギリまで部品を使い切りたいと考えました。ただし設備の稼働環境によっては、定格寿命に達する前に壊れてしまうこともあるため、先手を打って交換する必要があります。すなわち、各設備や部品に余力がどれくらい残っているのかを正確に見極めるための分析能力が求められます。また、膨大なデータを扱いつつ、効率的に計画を立案するためには業務プロセスのシステム化も欠かせません。
※製造元が想定する標準的な利用環境、利用条件において、その部品を利用可能な期間。部品の種類によっては、定格寿命の算出方法が国際規格として定められているものもある。
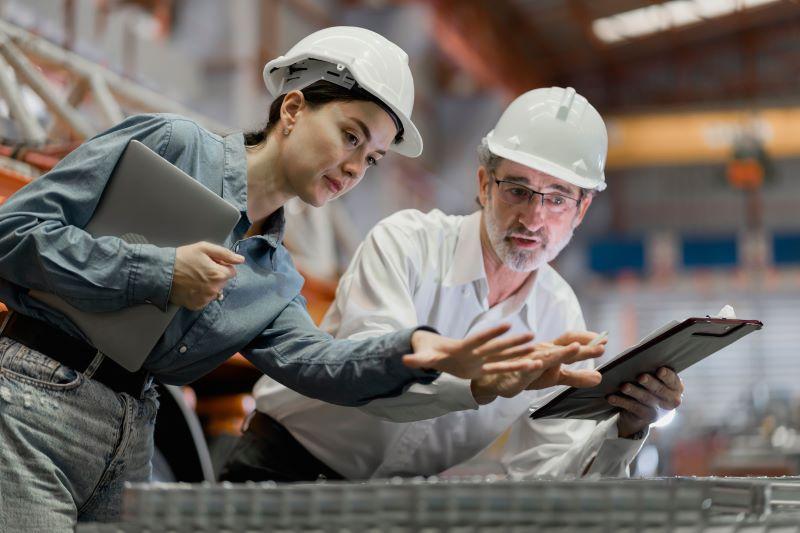
APMで各部品が持つパフォーマンスを最大限に引き出して活用する
こうした課題に対する一つの解が、設備資産パフォーマンスマネジメントシステム(Asset Performance Management:APM)です。APMは、さまざまなデータを利用して対象設備・部品の健全性を分析することで、各部品が持つ能力を最大限に活用できるようにします。言い換えればAPMは、予知保全(PdM:Predictive Maintenance)を実現するための手段です。
APMにおいてはまず、対象設備・部品の健全性を可視化することが重要です。可視化の手段として、リスクマトリクスという表示形式を利用します。リスクマトリクスはリスクを評価する手法の一つで、APMにおいては縦軸に対象の重要度、横軸に対象の故障確率(PoF: Possibility of Failure)をとった分布図を用います。ここで、「重要度×故障確率」の値がリスクを表します。重要度と故障確率が共に高い、つまりリスクが高い対象は、壊れたら影響が大きい設備が今にも壊れそうな状況にあることを表しているので、保全計画において最優先で対処すべき対象です。他方で、リスクが中程度以下の対象、例えばバックアップの設備があるため万が一壊れても影響が小さい対象は、たとえ故障確率が高かったとしても、保全作業を先延ばしにして良いでしょう。APMでは、そのような判断をシステムが支援します。
短期的な予知保全のアプローチとしては、各設備の状態を各種センサーで計測しつつIoTを活用してリアルタイムに監視します。これによって故障につながる可能性のある異常(予兆)を検知し、必要なメンテナンスを実施します。さらに長期的な予知保全のアプローチとして、システムに蓄積・保管された履歴データに基づき、過去のパラメータ値と過去に発生した故障のイベント(時期)の相関関係を分析することで故障を予知するとともに、各設備や部品の重要度も加味しながらリスクを判断し、保守タイミングの最適化を図ります。
APMは予知保全の観点から、効果とコストのバランスのとれた保全計画の立案を支援します。
保全計画業務のTo-Be業務フローを策定
ただ、概念的には理解できても、実際にどのように実施していくのかがイメージしにくいかもしれません。以下、エクサが担当した事例をもとにAPMをどのように業務に適用していくかについてご説明します。
保全計画に関する一連の業務をシステム化することを目指すあるお客様(D社様)では、次の2点を目標に掲げていました。
- グループごと、担当者ごとに紐づいている属人的な手作業を解消し、不特定の1人の担当者がすべての設備および構成部品の保全計画を立案できるようにする。
- 工数や費用などの制約条件を変えながら複数の保全計画を立案し、比較検討を行えるようにする。
これを受けてエクサがD社様と共に取り組んだのが、保全計画業務のあるべき姿(To-Be)であるAPM活用を想定した業務フローの策定です。
DXを成功させるポイントの一つは、現状の業務を正しく理解することにあります。その上でお客様とベンダーが一緒になってTo-Beを描いていくことが、システム化を進めていく上での最も基本的かつ重要な取り組みです。
まず、APMによる保全計画の対象期間、作成と更新のタイミング、立案結果そのもののライフサイクルがどうあるべきかについて検討し、誰がどの範囲でどのレベルまで保全計画を検討するかという基本方針を定めました。 これを受けてエクサがD社様と共に取り組んだのが、保全計画業務のあるべき姿(To-Be)であるAPM活用を想定した業務フローの策定です。
DXを成功させるポイントの一つは、現状の業務を正しく理解することにあります。その上でお客様とベンダーが一緒になってTo-Beを描いていくことが、システム化を進めていく上での最も基本的かつ重要な取り組みです。
まず、APMによる保全計画の対象期間、作成と更新のタイミング、立案結果そのもののライフサイクルがどうあるべきかについて検討し、誰がどの範囲でどのレベルまで保全計画を検討するかという基本方針を定めました。
次に、下記の点についても検討を進めました。
- 現行の計画立案作業に対し、APMはどこを担うのか
- 他システムとの役割分担をどうするのか
- 点検結果をAPMはどのように利用すべきか
こうした議論を経てエクサは、D社様に対してAPMを活用した保全計画業務の「たたき台」を提示しました。
従来の保全計画では、各設備や部品ごとの使用時間や生産量を積算することで定格寿命にどれだけ近づいているかを判断し、保全タイミングを決めていました。これに対してAPMでは、実際の稼働状況(稼働時間、動作速度、温度など)を含む複数のパラメータを反映した劣化予測モデルに基づいて故障確率を算出することで、より精度の高い保全タイミングを提示します。
こうした劣化予測モデルを作成するためには、過去の長年にわたる保全業務および保全計画業務を通じて蓄積してきたデータや、組織として培ってきた知見、熟練の担当者の頭の中にある経験則が不可欠であるため、原則としてはD社様の担当範囲となります。しかしエクサはこのお客様領域にも踏み込み、機械学習の手法も適用しながら劣化予測モデルのチューニングに共に取り組むことで、APMのシステム化を推進しています。
データレイク導入によるデータの一元管理へ
APMの導入に向けた、もう一つの重要な取り組みがデータの一元管理です。
製造業において工場内のデータはさまざまなシステムに分散して存在しています。各システムからデータを収集すること自体は可能ですが、それぞれのデータは鮮度や粒度、検索キーも異なるため、すぐに二次利用することは困難です。加えてAPMのシステムでは、IoTデータのように各設備から短時間に生成される大量のセンサーデータも取り込んで、活用できるようにする必要があります。
そこでエクサでは、必要なときに必要なデータに容易にアクセスできる基盤として、IoTデータ含めた工場内のあらゆるデータを一元管理する「データレイク」の構築をお客様に提案しています。データを1カ所に集めることで、ばらばらなツールを用いた無駄なアクセス、非効率な加工作業などは不要となり、データの容易な二次利用が可能となります。またバックアップを含めたデータ管理もシンプルになり、システム運用の負荷を軽減します。
お客様においてAPMシステムの導入を本格的に進めるのはこれからかもしれませんが、この取り組みは「現場DX」、さらには会社全体の「製造業DXのジャーニーマップ」の実現に向けて非常に重要な鍵となっています。
過去のメンテナンス履歴や故障履歴を含む設備資産情報を包括的に管理しているEAM(設備資産管理)に対して、APMによって明らかになる各設備の健康状態や将来リスクなどをフィードバックしていくことで、あるべき保全計画業務のPDCAサイクルを標準化されたフレームワークの中で回していくことが可能となるのです。これによって次のようなことが実現されます。
- 重要な設備のパフォーマンスを迅速に評価して、保守作業の優先順位付けと計画を実施する
- 設備ごとに過度な保全、不足している保全、適度な保全の状態を判別し、予測分析を用いて保全の実施を最適化する
- 設備パフォーマンスに好影響または悪影響を及ぼす運用要因を識別し、改善に向けた新たな保全戦略を導き出す
- 設備ごとの属性、リスク要因、保守のログ、障害までの予測時間などからパフォーマンスを詳細に分析し、保全業務および保全計画業務に有効な情報を提供する
エクサは引き続き、製造業のお客様の取り組みを支援してまいります。
執筆者紹介
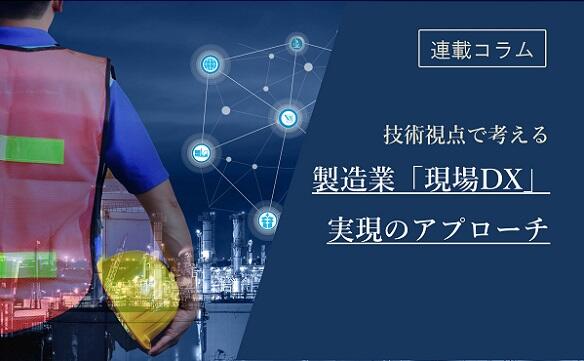
連載コラム:技術視点で考える製造業「現場DX」実現のアプローチ
このコラムでは、近年進化してきた先進技術を製造業の現場業務に適用した「現場DX」の事例やユースケースを、リレー形式でご紹介していきます。
関連コラム
関連ソリューション
関連事例
お問い合わせ
CONTACT
Webからのお問い合わせ
エクサの最新情報と
セミナー案内を
お届けします
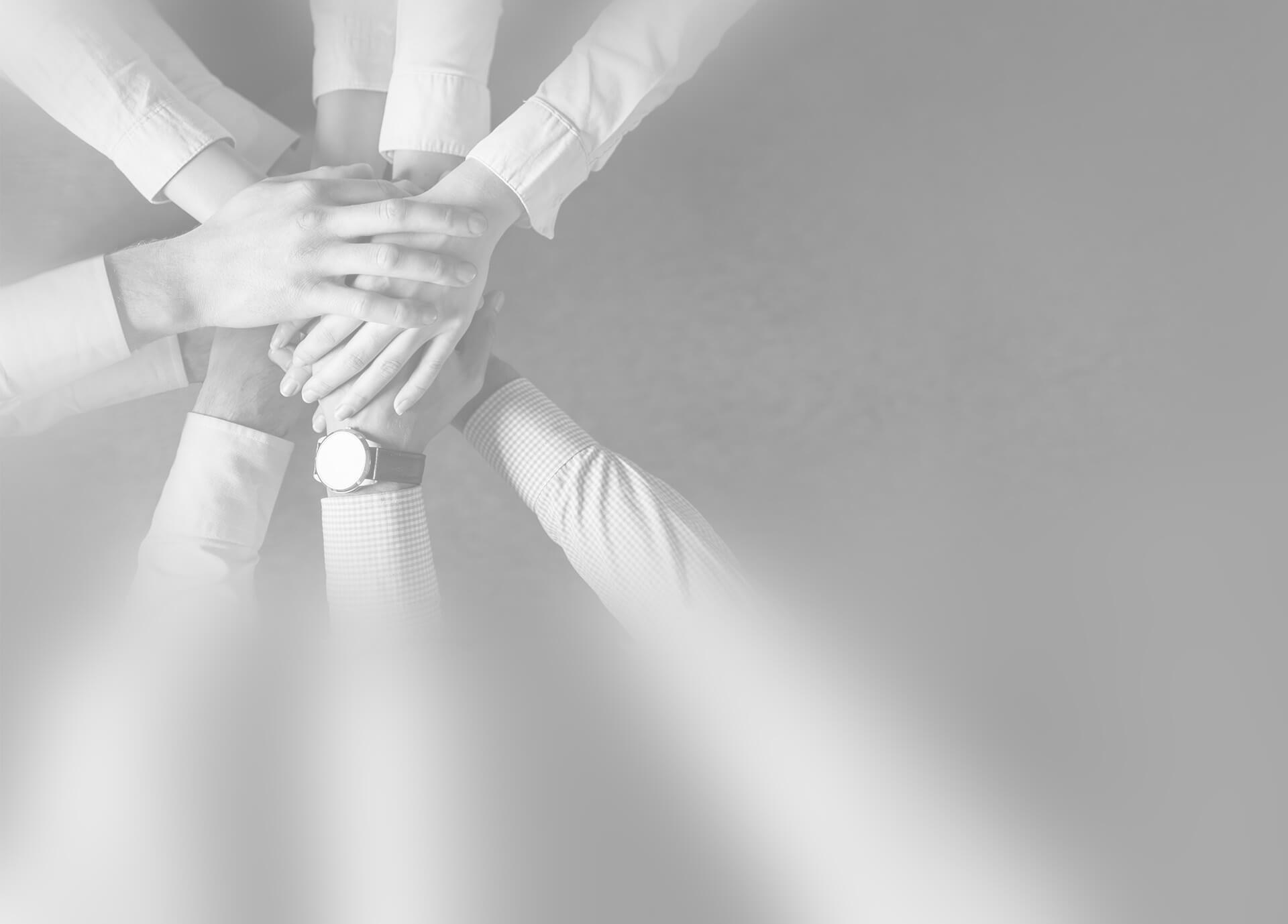