製造現場のデジタル化に欠かせないIoT技術
当連載の初回では、エクサが考える製造業DX実現の道筋と、その第一歩である「現場DX(現場デジタル化)」についてお話ししました。「DXジャーニーや現場デジタル化は、自分たちの業務とは縁遠い話」と思わないでください。今回からは、皆さんが日々直面されている現場課題への解決策に焦点を当てていきます。
業務において、「労力のかかる作業を省力化したい」と悩んだり、「これまでの改善活動には限界がある」と、諦めたりしていることがあると思います。そんな皆さんのヒントになれば幸いです。
前回触れたように、現場にアナログ状態で散在しているさまざまな情報をデジタル化し、DXを推進する上で欠かせないポイントは「IT(情報技術)とOT(制御技術)の融合」です。
とはいえ、「言うは易く 行うは難し」で、具体的にどうやってこの二つを融合していくのでしょうか。
その鍵を握るのが、IoT(Internet of Things:モノのインターネット)の技術です。
製造業の一部では、製品や生産ラインなどにIoT技術を導入し、生産や品質管理の高度化に活用しています。一方、設備の稼働状況の把握のために導入し、可視化はできるようになったものの、保全作業指示や点検計画に展開したり、業務を効率化したりするような実業務の変革にまでは結び付いていないケースも見聞きします。
いかにITが発達しても、IT技術だけで業務変革は起こせません。そして、OT領域の知見だけでも現場DXは実現できません。エクサはその双方に関する知識や経験を基に、お客様のお手伝いができると考えています。
「止まらない工場」は永遠の課題
製造現場に配置されているさまざまな装置や設備は、内部で使用されているパーツの経年劣化、想定範囲外の状況・環境下での運用、操作ミスなどの原因によって故障する場合があります。こうした故障や操作ミスによる「計画外停止の低減」は、すべての製造業において重要な目標です。
そこで製造現場では、定期的な点検によって各設備に適切なメンテナンスを実施するほか、異常が起こった際には警告灯などを通じて関係者に知らせ、早急に修理するといった体制を取っています。
このような人間系に依存した業務プロセスではどうしても後追いの対処になりがちで、設備の復旧(生産の再開)までに長時間を要しています。そうした中で多くのお客様企業から持ち上がってきたのが、「各設備の稼働状況をリアルタイムに可視化したい」というご要望です。そこで活用されるのがIoTの技術です。
具体的には、工場内の各設備や生産ラインの要所に配置したセンサー(温度、振動、電流など)から取得したデータ、監視カメラで撮影した映像データなどを、ネットワークを通じてITシステムに集約します。これらのデータはTableau*1などのBIツール(ダッシュボード)を使って一元的に表示されます。センサーのデータは、センサーを管理しているPLC(Programmable Logic Controller)から、例えばOPC(OLE for Process Control)サーバーを経由して取得します。
ただし、単にデータを可視化するだけでは、従来の警告灯を高度化しただけに過ぎません。そこでエクサでは統計解析ソフトウェア(IBM SPSS*2等)や機械学習、AI の技術を駆使して収集したIoTデータを分析し、各設備に何が起こっているのか、どのような状態になっているのかを読み解く試みをしています。
さらにこの分析結果は、設備管理システムにも共有されます。例えば、世界の多くの企業で利用されている設備保全統合管理システム「IBM Maximo Application Suite*3(以下、IBM Maximo)」は単一のプラットフォームで資産の監視・管理、予知保全、信頼性プランニングなどを実現するツール群です。工場内に配備されているすべての設備を一元管理し、定期点検の計画や作業スケジュール策定など保全業務全般を担っています。従ってIoTデータおよびその分析結果をIBM Maximoと連携させることで、設備に突発的な故障が発生した際に保全要員に対して緊急の作業指示を行うなど、的確なアクションを迅速に実施することが可能となります。
そして、この一連のサイクルを回し続けることで設備管理や保全業務を洗練し、効率化・省力化を推進していきます。その取り組みの一環として、エクサでは設備に発生する異常の兆候を捉えて、装置が壊れる前に対処する予知保全にもアプローチしています。非常に難易度の高いテーマではありますが、製造現場との緊密な連携を通じて「止まらない工場」を共に実現していきます。
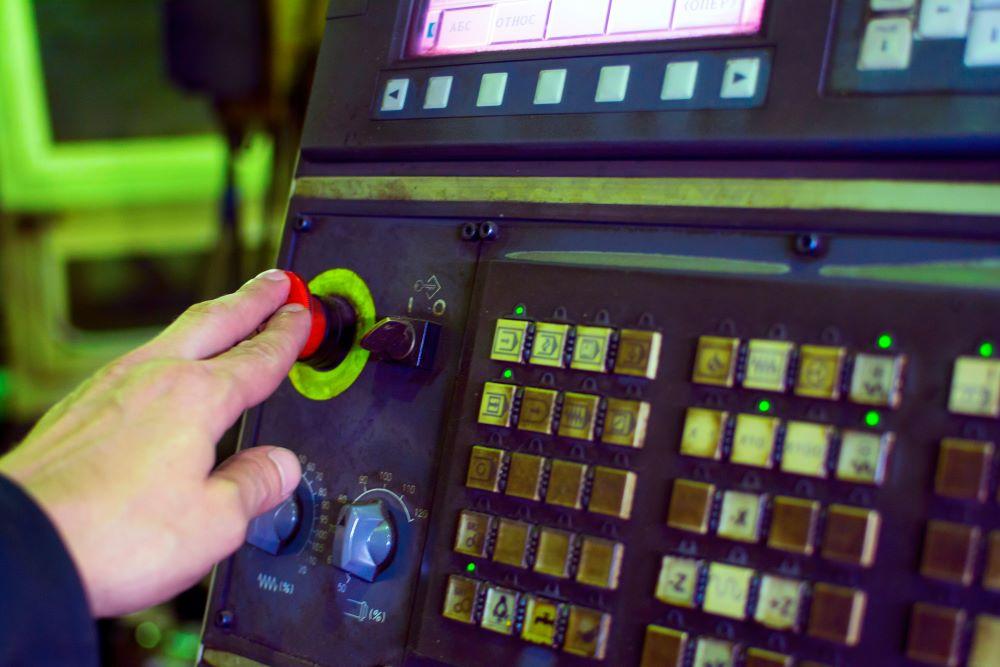
ユースケース: 主要設備の稼働をダッシュボードに表示、現場に行かずに状況を把握
実際にエクサとともにIoT技術を活用してITとOTの融合に取り組み、現場DXを推進している機械メーカーの例を紹介します。
このお客様(A社様)は産業用電子機器を専門とし、業界内でも高いシェアを誇っていますが、設備に突発的に発生する故障に悩まされていました。工場内の設備に問題が起こって初めて、ベテラン作業者の経験に頼って原因を探り、修理するという後追いの対処を実施。ベテラン管理者の方の頑張りで生産ラインを支えているという状況でした。その負荷を下げること、そして、現場の警告灯を見なくても設備の状況を事務所で確認できること、ひいては設備の稼働率を高めることが課題として挙げられていました。こうした課題はどこの工場でも発生し、対応が必要なことが多いのではないでしょうか。
A社様では今まで、定期点検やメンテナンス時に収集したデータをExcel*4に記録していました。しかし、過去のデータを遡って確認するには、Excelでは限界があります。また、故障が発生する以前の詳細な情報、例えばその設備がどのような状況で稼働し、どのような兆候が起きていたのかなどのデータはありませんでした。
こうした経験を経て、新たなアプローチとしてエクサとともに取り組みを開始したのが、IoT技術によって集められたデータを活用した統合設備管理システムの構築です。
まず各設備を制御しているPLCからOPCサーバー経由で収集したIoTデータをエッジサーバーに蓄積するようにしました。一方で設備管理システムとしてIBM Maximo を導入し、設備台帳管理、予防保全としてのメンテナンス作業計画・実績管理、故障の修理作業指示・実績管理のためのマスターDBとして活用しています。 そして、この二つの基盤の間で、例えば事前に設定した閾値を越えたことをエッジサーバーから設備管理システムに連携して作業指示書が自動的に発せられる、あるいは、各設備の稼働状況をリアルタイムに近い形でダッシュボードに表示することによって、現場に行かなくても設備の状況を把握し、次の対応が取れるようになりました。
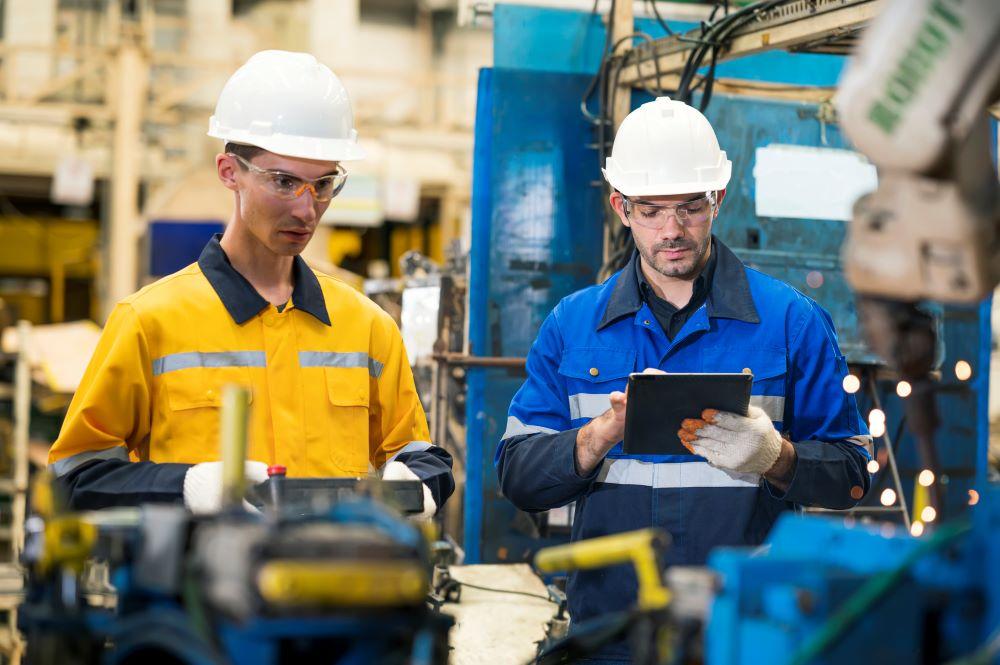
さらに、エッジサーバーに蓄積されたデータをBIツールで処理することで、例えば、主要設備のMTBF(平均故障間隔)、MTTR(平均修復時間)を算出し、ダッシュボードに表示するなど、データを単に蓄積するのではなく、それを活用し、生産に役立てようとされています。
このように、A社様では現場DXによって大きな成果を上げ、さらなる業務変革へと製造業DXのジャーニーマップに示した歩みを進めています。しかし、このような保全業務の効率化や保守コスト削減は、当然ながらエクサのサポートだけで成し得るものではありません。A社様のこれまでの経験と知見を活かしたデータの分析が必要です。Smartファクトリー開発部にはデータサイエンスを得意とするチームメンバーもいます。ぜひ、お客様と一緒に変革プロジェクトを進めていきたいと考えています。
現場DXの第一歩として、まずIoT技術の活用から検討してみませんか。お気軽にお問い合わせください。
*2 IBM、およびSPSSは、世界の多くの国で登録されたInternational Business Machines Corp.の商標です。
*3 IBMとIBM Maximoは、米国およびその他の国または地域におけるInternational Business Machines Corp.の 商標または登録商標です。
*4 Excelは、米国Microsoft Corporationの米国およびその他の国における登録商標または商標です。
執筆者紹介
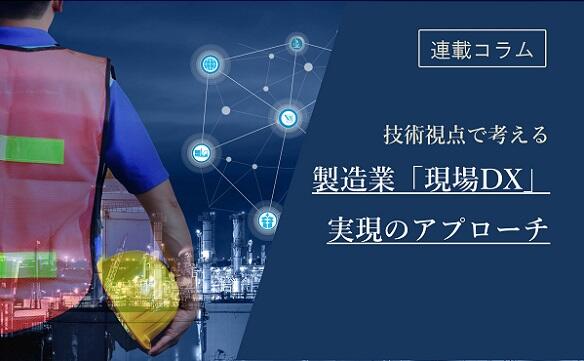
連載コラム:技術視点で考える製造業「現場DX」実現のアプローチ
このコラムでは、近年進化してきた先進技術を製造業の現場業務に適用した「現場DX」の事例やユースケースを、リレー形式でご紹介していきます。
関連コラム
関連ソリューション
関連事例
お問い合わせ
CONTACT
Webからのお問い合わせ
エクサの最新情報と
セミナー案内を
お届けします
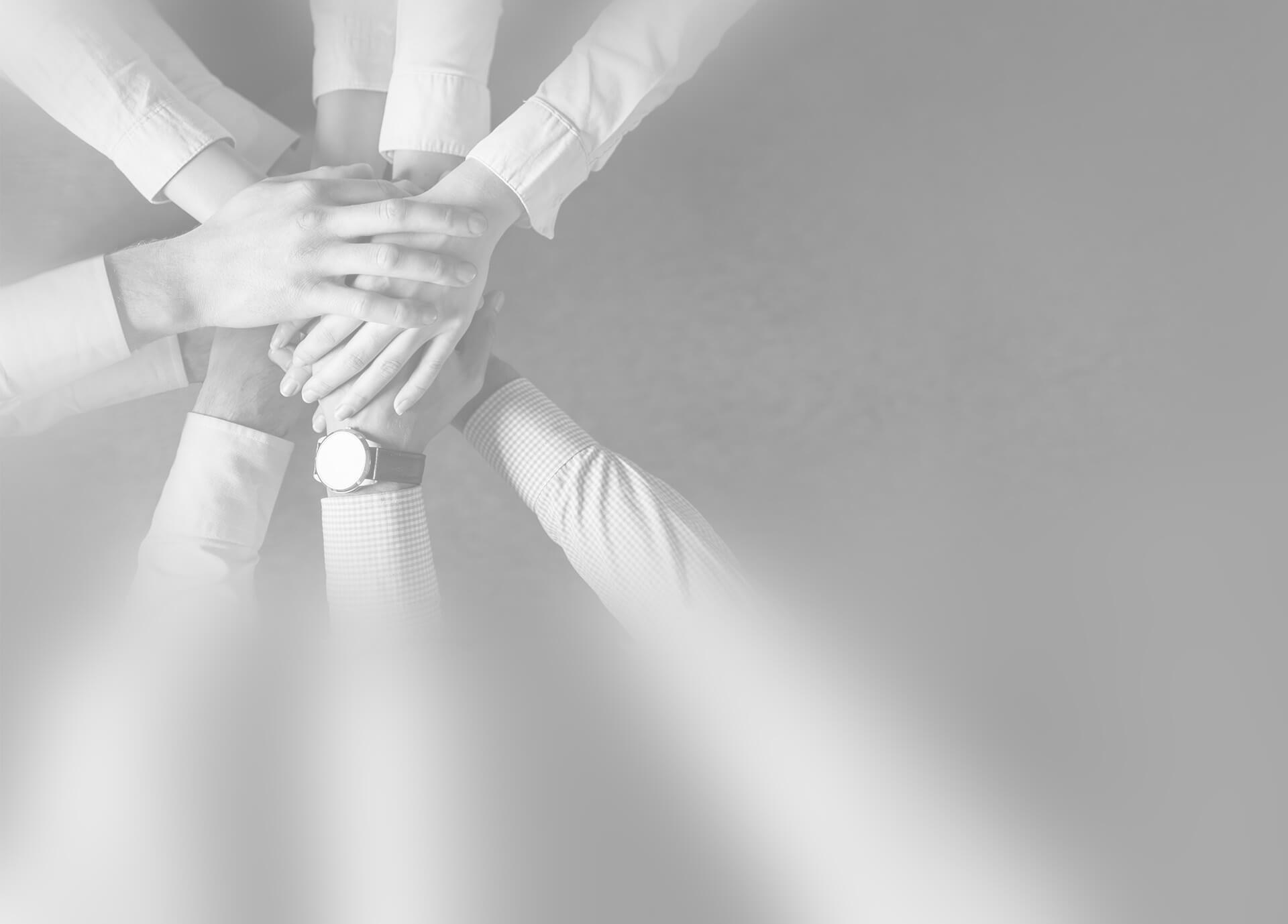