多くの工場が抱える点検・保全業務に関する課題
製造業にとって永遠のテーマとも言うべき「止まらない工場」を実現するためには、工場内で稼働しているさまざまな装置や設備に対する継続的な点検と適切な保全が欠かせません。しかし発電所や製鉄、化学、自動車などの大規模な工場やプラントになると、その点検・保全業務は容易ではありません。
次のような課題を、多くの工場が抱えているのではないでしょうか。
- 敷地や建屋が広すぎて短時間(短期間)では回り切れない
- 点検の巡回ルートも複雑で不慣れだと迷うことも多い
- 誤って入ってしまうと生命にかかわる危険な場所もある
- 正確な点検や保全を行うためには装置・設備ごとの専門知識を必要とする
- 機械系、電気系(制御系)、ボイラー系、エネルギー系など、複数の専門技術者が常にセットになって回らなければならない
- 担当者ごとに判断のバラツキがあり、ケアレスミスも起こる
さらに、これまで当たり前のように行われてきた点検・保全業務ですが、作業を担当する個人に依存している点も多々あり、昨今の人手不足によって、課題が一層顕在化しています。しかし、点検・保全業務の課題の本質は人手不足だけではありません。新たな人材を補充できたとしても、従来から担当されていた方のレベルに達するまでには、時間がかかります。業務の仕方を変えなければ、「止まらない工場」のような抜本的な現場DXを実現することはできないでしょう。
今回は、「より少ない人数で、より安全に、ミスを起こすことなく、確実に点検・保全を実施できる方法はないか」というお客様の共通課題についてサイバーフィジカルシステム(CPS)の構築で貢献することを考えてみたいと思います。
ユースケース1:XRデバイス+クラウドアプリで点検・保全業務を遠隔で支援する
お客様が将来的に目指すべきは、工場内のあらゆる装置・設備の稼働状況を見える化し、故障やトラブルが発生する前にプロアクティブに対処する予知保全や、点検・保全の自動化・自律化といった取り組みです。しかしこれらを実現するには、技術的にもコスト的にも乗り越えなくてはならない多くの壁があります。
そこで今ある技術や製品を活用することで、現場業務を変革するソリューションとして注目されているのが、VR(仮想現実)やAR(拡張現実)、MR(複合現実)など「XR※」と呼ばれる技術を活用した、点検・保全作業の遠隔でのサポートです。
※クロスリアリティ/エクステンデッドリアリティの略で、現実世界とデジタルな仮想世界を融合させる革新的な技術(AR/VR/MR)の総称
例えば比較的容易に導入できるスマートグラス型のXRデバイス(ヘッドセット)に、マイクロソフト社のHoloLensがあります。眼鏡の上から装着できる、あるいはヘルメット一体型のモデルも用意されていることから、危険度の高い工場やプラントや建設現場などで多く活用されています。Windows*1を 搭載した自己完結型ホログラフィックコンピューターとして設計されているため、Teamsをはじめマイクロソフトが用意している豊富なアプリケーションをクラウド経由で利用することができるのです。
これまでも点検・保全の現場に赴いている作業者に対して、事務室など離れた場所からベテランの技術者が携帯電話やトランシーバーを使って指示やアドバイスをすることはよくありました。しかし、音声のみでは要領を得られない場合もあり、意思疎通のために長い時間を要しがちです。これに対して現場の作業者がXRデバイスを介して見ている映像を共有すれば、対象設備や状態などをより具体的に伝えることができ、タイムロスを減らすことができます。現場で点検・保全作業にあたっているのが経験の浅い技術者だったとしても、的確な指示をスピーディーに出すことが可能となり業務効率を高め、何よりも大きなメリットとして事故につながりかねない誤操作を防止できます。
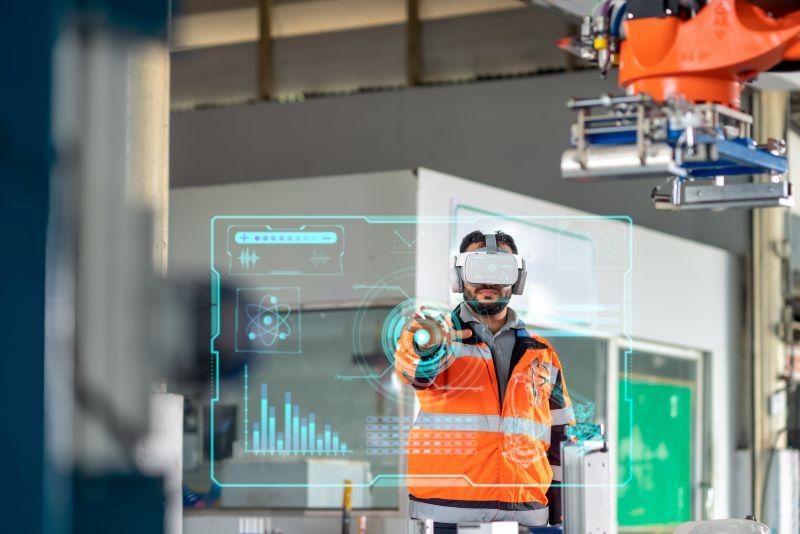
ユースケース2:電波が届かない場所ではスタンドアロン型XRソリューションを活用
ただし、上述したようなXRソリューションを点検・保全業務に適用するためには、「ネットワークにつながっている」ことが大前提です。大規模な工場やプラントでは、広大な敷地や建屋のすべてのエリアで、Wi-Fiやローカル5Gなどのネットワーク環境が整備されているとは限りません。そうした場合には、また別のアプローチを取る必要があります。
以下に、ある製造業のお客様(B社様)において、実際にトライアルを行ったユースケースをご紹介します。
ネットワーク接続が困難な現場では、XRデバイスをスタンドアロンモードで使用して作業を実施。その後、ネットワークに接続可能な場所に移動して、スタンドアロンモードで蓄積したデータをサーバーにアップロードする方法で対応しました。このアプローチについて、少し詳しく見ていきましょう。
■ソリューション概要
① 工場全体の3Dモデルを作成
まず3Dスキャナーを用いて工場全体を計測し、収集した点群データをもとに正確な3Dモデルを作成します。
② デジタルツインとして再現
作成した工場の3Dモデルを、点検・保全作業者が持ち歩いているXRデバイスに転送して保存。現実の工場をバーチャル空間にリアルに再現した、いわゆる「デジタルツイン」として表示します。 (注:前項ではHoloLensの利用例を紹介しましたが、ネットワークに常時接続できない環境下では、XRデバイス自体にアプリや大量のデータを保持して、スタンドアロンで運用できるようにする必要があります。処理負荷やバッテリーの持続時間なども考慮し、ここではタブレットPCをXRデバイスとして利用することを想定しています。)
③ 今いる場所、見ている装置・設備を特定
作業者は自分が今いる場所を、持ち歩いているXRデバイス(タブレットPC)のカメラで撮影します。この映像に基づいて、作業者は自分が工場内のどこにいるのか、カメラ映像の視界に入っているのは、どの装置・設備なのかを把握できます。 映像として捉えている光景やモノの形状、位置関係などをデジタルツインと突き合わせ、工場内での現在地や見ている装置・設備を推定します。さらに、デジタルツイン上に特定のモノの画像をマーカー(出現キー)として事前に登録しておけば、より正確に現在地や装置・設備を特定することができます。
④ AI(機械学習)を活用した作業支援
特定された装置・設備の制御盤(操作パネル)にXRデバイスのカメラを向けると、事前に学習済みのAIモデルと照らし合わせ、現状の設定がどうなっているのかを認識するとともに、設定変更が必要とされる際には必要な操作に関する指示やヘルプを表示します。従来のように分厚いマニュアルや作業手順書を持ち歩く必要はありません。
制御盤には似たようなスイッチが多数並んでいるものもあり、作業者が指示とは違うスイッチを誤って操作したり、AIモデルが誤認識を起こしたりする恐れがあります。予防策として、前述したマーカーを制御盤ごと、スイッチごとに登録しておけば、正確な操作を支援することができます。
⑤ 実施した作業の記録
作業者がたどったルートや、現場で行った操作はすべてログとしてXRデバイスに記録されます。
なお、作業者は設定変更を行った装置や、その場では対処できない異常を発見した装置について、以降の使用や操作を禁止するための物理札を掲げておきます。この物理札にはRFIDタグが組み込まれており、そのデータをXRデバイスで読み込むことで、どの装置にどの物理札を掲げたのかの記録も残されます。
⑥ 離れた場所にいる管理者との情報共有
上記のような点検・保全業務の支援はすべてオフライン状態で行われますが、ネットワーク接続が可能なエリアまで作業者が戻ってきた時点で、XRデバイスに記録されたログがクラウドやオンプレス環境のサーバーにアップロードされます。
事務所など離れた場所にいる管理者や熟練技術者は、作業者から報告書が届くのを待つことなく、アップロードされた情報を即座に閲覧して正しく作業が行われたかどうかを確認するとともに、作業者にフィードバックすることができます。万一、実施した操作に不手際が発見された場合でも、タイムロスを最少化した対処が可能になります。
スモールスタートで対象エリアを段階的に拡大
一つ目の市販のXRデバイスとクラウドのアプリケーションを組み合わせる方法に比べて、二つ目のスタンドアロン型のXRソリューションは、企業によっては少しハードルが高いかもしれません。
なぜなら工場内を3Dスキャンして正確な3Dモデルを作成し、バーチャル空間にデジタルツインを再現するといった、取り組みの導入部分からして多くの苦労が伴います。的確に位置や角度を変えながらの計測および点群データの収集を行わなければならず、測量に関する専門的なスキルとともに工数も要します。各装置・設備の制御盤のAIモデルの作成も同様で、地道な機械学習を重ねる必要があります。
そこで重要となるのは、スモールスタートのアプローチです。プロトタイプを作成して工場内の限られたエリアに適用し、点検・保全の実務を通じて検証し、システムを改善していきます。そして効果が実証されたなら、段階的に対象エリアを拡大していきます。最終的に工場全体にシステムが行き渡ったならば、次のステップとしてそのノウハウと成果物を生かす形で別工場への横展開も可能となります。
エクサはこうした息の長い取り組みにもしっかり寄り添い、お客様の成果が出るまで根気よくサポートしていきます。
現場からのDX、まずは設備の点検・保全業務の変革について、エクサと一緒にチャレンジしてみませんか。ぜひともお気軽にお問い合わせください。
執筆者紹介
株式会社エクサ
エンタープライズ開発本部
Smartファクトリー開発部長
加藤 俊弘
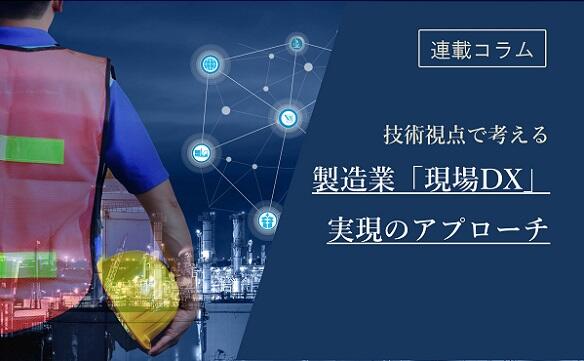
連載コラム:技術視点で考える製造業「現場DX」実現のアプローチ
このコラムでは、近年進化してきた先進技術を製造業の現場業務に適用した「現場DX」の事例やユースケースを、リレー形式でご紹介していきます。
関連コラム
関連ソリューション
関連事例
お問い合わせ
CONTACT
Webからのお問い合わせ
エクサの最新情報と
セミナー案内を
お届けします
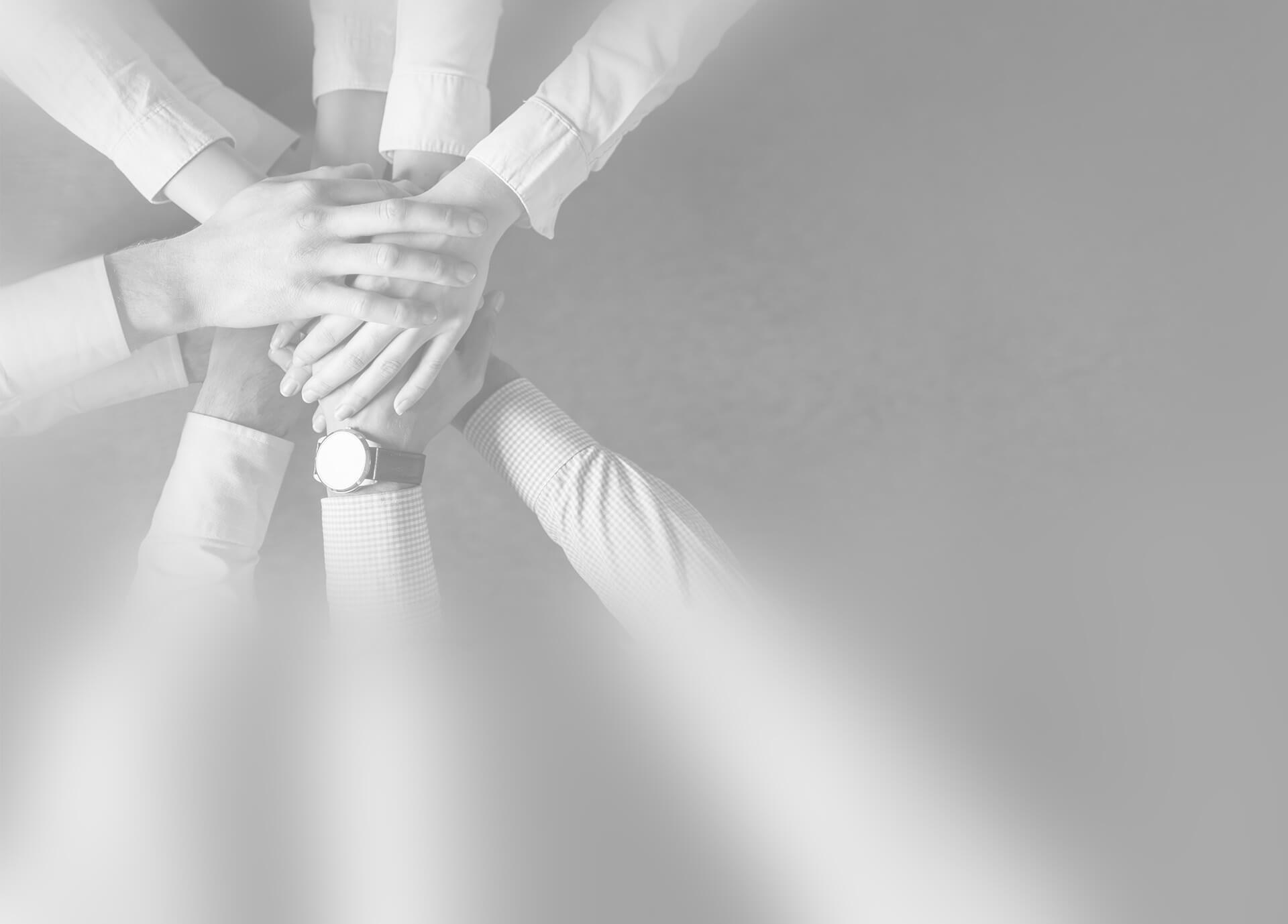