技術の進化によって、過去には実現できなかったことが現実のものとなっています。例えば、業務の実施場所(いわゆる、現場)に張り付いて業務を実施せざるを得ないという状態を変革し、より創造的な仕事の実施へとシフトできる、そんな可能性が目の前に広がっています。
製造業において生産を任された皆様は、安定的に生産設備を稼働させること、さらに生産効率を高めることに日夜心血を注いでおられるのではないでしょうか。そのご苦労を少しでも軽減するため、そして生産の安定レベルを少しでも上げるために、エクサでは従来のIT技術に加え、近年注目されているAI、VR、AR、データ分析、IoT技術、データ収集技術などを用いて、サイバーフィジカルシステム(CPS)を構築し、製造現場のお役に立ちたいと考えています。
このコラムでは、近年進化してきた先進技術を製造業の現場業務に適用した「現場DX」の事例やユースケースを、リレー形式でご紹介していきます。その中には、お客様とともにエクサの担当者が試行錯誤を重ねたアイデアも含まれています。
より良いものづくりに向けて、現場DXに踏み出していただくヒントになれば幸いです。
はじめに -製造業の現場DXを支援するエクサの取り組み-
デジタルトランスフォーメーション(DX)が叫ばれてからすでに数年が経過しましたが、取り組みが足踏みしている状況も散見されます。
その原因は、主に下記のような点にあると推測しています。
2 今の情報技術でどんなことができるのか分からないの情報技術でどんなことができるのか分からない
3 自分たちの工場の将来あるべき姿をなかなか描けない
4 製造装置自体は分かっても、装置の状態を可視化する方法は分からない
5 機械と電気のいずれか一方は分かっても、両方を分かる人がいない
6 設備のデータを収集しているけれども、どのように分析したらよいかが分からない
エクサのSmartファクトリー開発部では、このような悩みを抱える皆様と力を合わせて課題を解決し、製造業のDX化を推進するために幅広い支援を行っています。
製造現場のDX事例を、担当者のリレー形式でご紹介する連載コラムの初回は、エクサが考える製造業DX実現の道筋とその第一歩である「現場DX(現場デジタル化)」に関するお話をします。「DXだのデジタル化だの、その手の話はもう聞き飽きたよ」とお感じかもしれませんが、少しだけお付き合いください。
変革への取り組み強化が求められる国内製造業
生産年齢人口の減少に伴う人材不足、エネルギーや資源コストの高騰、地政学的リスクの上昇など、不確実性がますます高まっていく中で、製造現場の皆様が抱える課題はますます高度化し、複雑化しています。国内外の競合他社と市場で伍していくとともに、自社が成長していくために、さらなるデジタルトランスフォーメーション(DX)の強化が求められています。
しかし、現在の製造業界においては多くの情報がアナログ形式のまま存在しているか、あるいはデジタル化は進んでいても抜本的な業務変革には至っていない状況が広く見られます。現状のままでも生産を進めていくことは可能だと思います。しかし、工場内の業務がベテラン技能者の"匠の技"のような暗黙知(主観的で言語化されていないナレッジ)で成り立っていても、彼らが年々退職していき、また、技能を受け継ぐ若手の採用や育成も難しい今、何らかの対策を取っていかないと、いずれ生産が継続できない状況になってしまいます。
そうならないために、現場の個々の技能者の頭の中にある知見を引き出し、形式知へとまとめていくこと、新しいIT技術で担当者に寄り添った生産作業を実現していくことが求められているのではないでしょうか。
そこで必要となるのが、IT(情報技術)領域とOT(制御技術)領域の連携です。工場内の設備や作業者の状態・実績などをデジタル化されたデータで捉え、ITシステムで蓄積・活用することで生産に関連する業務の高度化、さらには経営の高度化が可能となります。この連携により、リアルタイムな情報共有や効率的な意思決定が実現され、企業の競争力向上に寄与します。
ITとOTの両輪で、将来の業務のあるべき姿を描き、新たなシステムをつくり上げることが求められます。
業務効率・業務品質向上のカギを握るITとOTの融合
エクサは国内製造業がDXを推進していく上でのテーマを検討し、ロードマップを策定するためのベースライン となる「製造業DXのジャーニーマップ」を取りまとめました。
[図1]製造業DXのジャーニーマップ
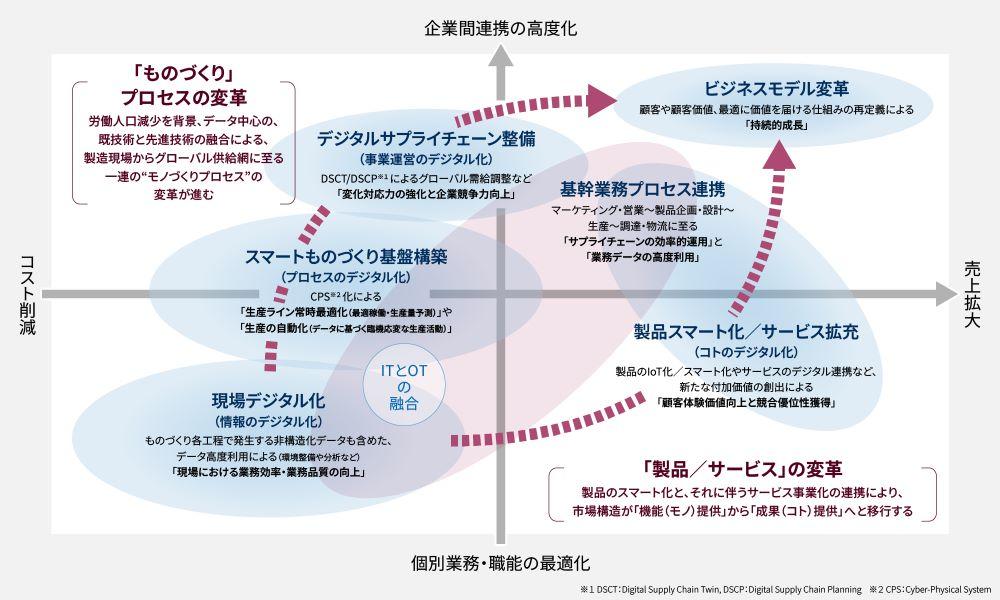
ここには大きく、二つの道筋があります。 一つは現場デジタル化(情報のデジタル化)からスマートものづくり基盤構築(プロセスのデジタル化・垂直統合)、デジタルサプライチェーン整備(事業運営のデジタル化)を経てビジネスモデル変革に至る「ものづくりプロセスの変革」ルートです。 もう一つは、現場デジタル化から製品スマート化/サービス拡充(コトのデジタル化)、基幹業務プロセス連携(プロセスのデジタル化・水平統合)を経てビジネスモデル変革に至る「製品/サービスの変革」ルートです。
いずれの取り組みにおいても出発点となるのは、現場におけるデジタル化です。ものづくりの各工程では、その日の生産実績や歩留まりなどをExcel*1で管理したり、設備に故障が起こった際にはその対応履歴を日報にまとめたりしています。また大量生産を行っている工場では、ラインを次々に流れてくる製品をカメラで撮影して品質をチェックしているケースも見られます。こうした製造現場から発生する多様なデータを"使い捨て"にするのではなく、しっかり捉えて高度利用することで、「現場における業務効率・業務品質の向上」を目指します。エクサではこれを「ITとOTの融合によって実現する『現場DX』」と定義しています。
製造業を母体とするノウハウを生かして課題解決に寄り添う
エクサはこうした製造業の現場DXの推進を支援いたします。その背景にあるのは、エクサ自身がもともと製造業だったという歴史です。1987年に日本鋼管株式会社(現JFEスチール株式会社)の情報システム部門が分離独立する形で発足し、その後もJFEエンジニアリング株式会社をはじめとする設備・装置メーカーの皆様と協働しながら、JFEスチールにおけるさまざまな業務のデジタル化やデータ分析・活用、DX推進といった取り組みに携わってきました。実際に製鉄所の現場に赴いて課題や要件のヒアリング、システム導入、ユーザーサポート、メンテナンスなどにあたる機会も多いため、製造業の文化や感覚を熟知しています。
[図2] エクサの強み
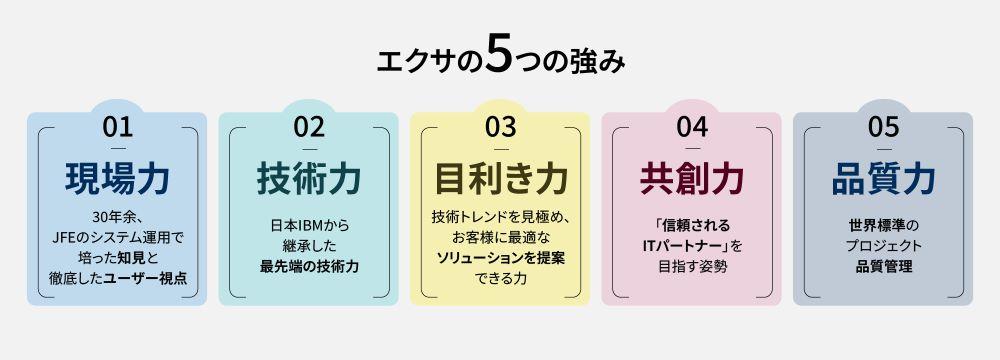
長年にわたり培ってきたこの経験とノウハウがあるからこそ、製造業のお客様が抱えるさまざまな課題の解決に寄り添い、共に現場DXを推進していくことが可能なのです。エクサは皆様にとって身近な存在であり、同じ船に乗った仲間であるとお考えいただければ幸いです。
お客様の取り組みを一貫して支援するSmartファクトリー部の体制も強化しています。具体的には現在、次の3つの室が連携して活動しています。
1 設備管理ソリューション室:IBM Maximo Application Suite*2ならびにエクサ独自のベストプラクティスをパッケージ化したMaximo Base Kitなどのソリューションをベースに、最適な統合設備管理システムを実現します。
2 データサイエンス推進室:収集したIoTデータの可視化や分析を担います。設備に発生する予兆を捉え、故障する前に先手を打って対処する予防保全や予知保全も視野に入れています。
3 海洋・DX開発室:お客様と上記2つの室との共創によって実現された成果をベースに、PLC(Programmable Logic Controller)や各種センサーからIoTデータを収集し、エッジサーバーに蓄積、さらに3Dデータ活用、XR(VR、AR、MR)技術の活用、現場担当者に分かりやすいデータの統合化、ロボットによる点検など新たな価値創造を追求し、現場DXを推進していきます。
一方でSmartファクトリー部はエクサの他部門とも緊密に連携し、サービスDX(サービスとITの融合)や経営DX(経営とITの融合)を推進することで、ビジネスモデル変革をゴールとする「製造業DX」の実現を支援していきます。 DXについて、現在お客様各社がそれぞれ取り組みを進めています。次回以降は、その実態や活用方法について、技術などの基礎知識や現場の声などもご紹介しながら、エクサがそれらを使って、実際にどのようなサポートを行っているか、さまざまな事例を紹介していきます。
*2 IBMとIBM Maximoは、米国およびその他の国または地域におけるInternational Business Machines Corp.の 商標または登録商標です。
執筆者紹介
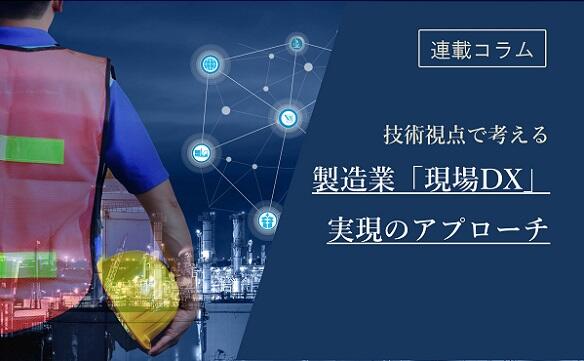
連載コラム:技術視点で考える製造業「現場DX」実現のアプローチ
このコラムでは、近年進化してきた先進技術を製造業の現場業務に適用した「現場DX」の事例やユースケースを、リレー形式でご紹介していきます。
関連コラム
関連ソリューション
関連事例
お問い合わせ
CONTACT
Webからのお問い合わせ
エクサの最新情報と
セミナー案内を
お届けします
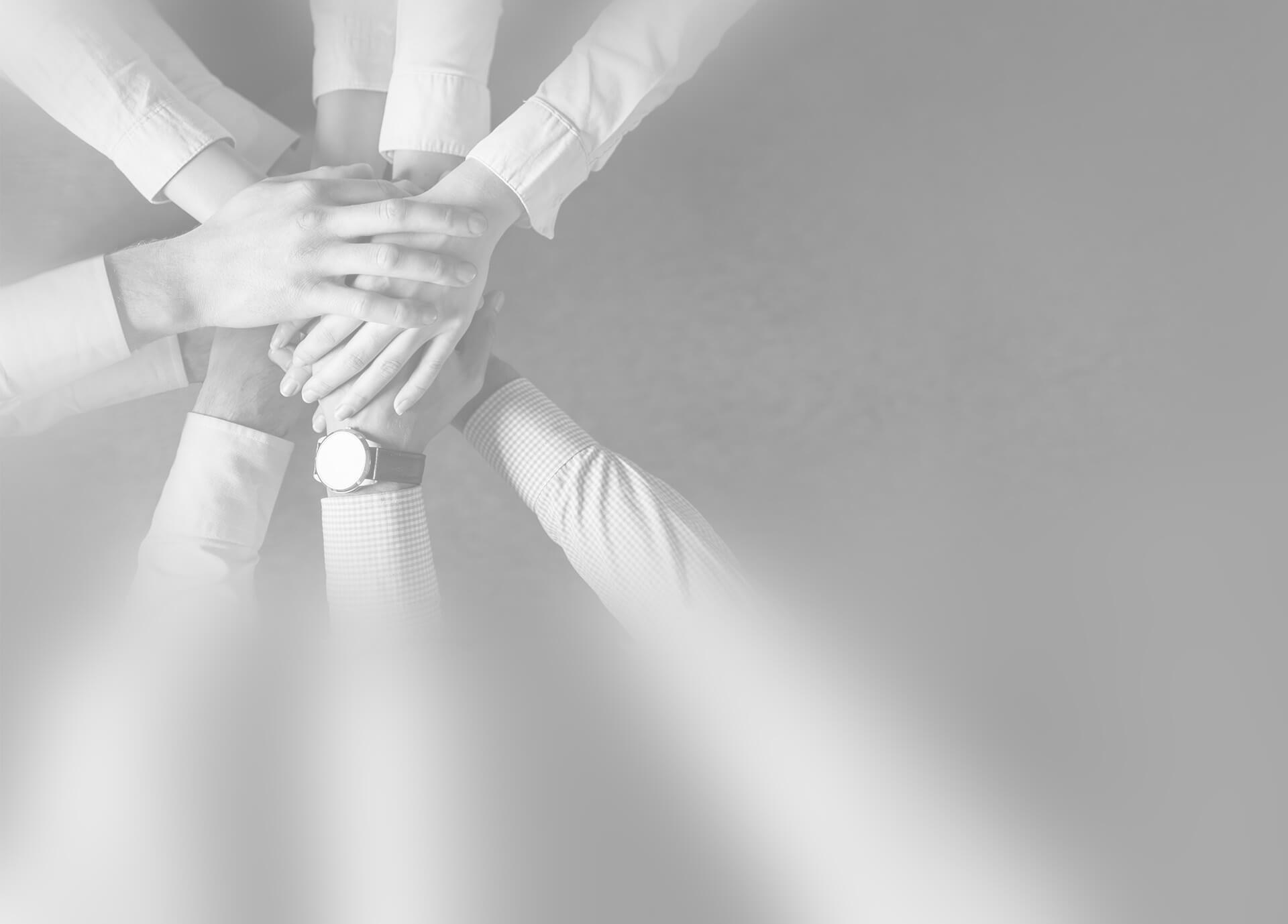