1.在庫は悪だ、といった手前。。。
10年以上前の話ですが、ある自動車部品メーカの工場が火事になりました。その影響で、その部品メーカが製造する部品を使用する某自動車メーカのラインは半日で止まりました。この自動車メーカは、「在庫は少ないほど良い」という指導をしてきたのですが、在庫を持たない操業をした結果、生産のストップと同時に出荷もストップとなりました。
さすがに、この自動車メーカは、部品工場に苦情を言うことができなかったようです。噂で聞いた話では、本当に在庫をもっていなかったということで、褒められたそうです。工場止めて褒められるというのもすごい話ではありますが。
このケースでは、部品工場と自動車組み立て工場が数十キロしか離れていなかったため、輸送リードタイムが短く、「在庫は悪」と考えるのも仕方ないとは言えるかもしれません。
2.人生何が起きるかわからない
しかし、輸送距離が長い場合、特に海を越えるとなるとまた話が変わってきます。
最も近い、中国・アジア地区でも2週間ほどは見なくてはなりません。2021年11月現在、コンテナは払底しており、輸送料金はうなぎのぼり。お金も時間もかかります。日本メーカの生産は大変柔軟なところが多く、販売動向をみながら柔軟に生産をすることでビジネスチャンスを逃さないようにすることにかけては、おそらく今でも世界一でしょう。しかし2週間というのは情勢が変化するには十分な期間です。もとより、火事などのリスクよりも港でのリードタイム変化によるリスクのほうが格段に大きいというのが現実です。港湾労働者のスト、港湾設備の不足で作業が滞るなど、不測の事態が起きると瞬く間に港の外に貨物船が何十隻も文字通りたまってしまいます。先日のスエズ運河における座礁も「想定外」だった企業は多いのではないでしょうか。また積み替えた後の陸送のリードタイムも日本ほど安定していない上に時間がかかります。これらの変動要因を在庫という形でリスク回避することになりますが、"在庫をどの程度保持しておくべきか"ということは勘と経験だけですべてをカバーできるわけではありません。
3.印籠にはならないけど
4.信じる者は
しかしサプライチェーンソフトは市場動向の予測や、海運状況の急変など、リスク設定までは考えてくれません。何が変動要因になるか、市場はどう動くか、これはまだまだ人間系でカバーしなくてはならないところです。市況のひっ迫を予測して能力確保に走るとか、海運状況の悪化に備えてコンテナ確保に走るとか、そういうことは教えてくれません。
あるソフトウエアメーカは「機械学習で需要予測ができる」と豪語しているようですが、偶発リスクまで予測できたらそれは確かにすごい。 もっとも我々の業界ではそれができると自称するシステムを"Crystal Ball System"と呼びます。その端末の左右には蝋燭がゆらめいていることでしょう。
LIXIL様導入事例がこちらからダウンロードできます
資料では、お客様にインタビューした以下のような内容を掲載しています。
- 統合生産システム構築の背景/目的
- BOMソリューションとしてSPBOMを選んだ理由
- SCMソリューションとしてKinaxis Maestro(旧称:RapidResponse)を選んだ理由
- システム構築によって得られた効果
- LIXIL様の今後の展望
Maestro(旧称:RapidResponse)
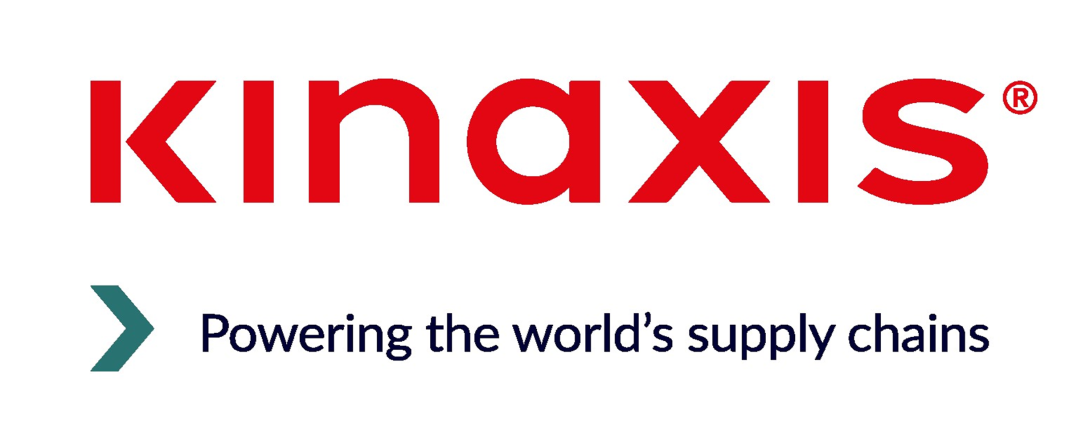
S&OP分野でのグローバルリーダーに位置づけられるクラウドサービス
需給の急激な変動に際して、異常を瞬時にアラートし、迅速な意思決定・対応を支援するSCM、S&OPソリューションです。
執筆者紹介
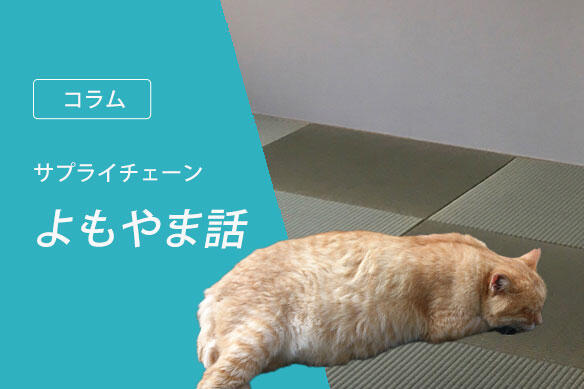
コラム:サプライチェーンよもやま話
サプライチェーンに関するあれこれを著者独自の視点からお届けします。
貴社サプライチェーン改革のヒントがここにある(かもしれません)。
関連コラム
関連ソリューション
関連事例
お問い合わせ
CONTACT
Webからのお問い合わせ
エクサの最新情報と
セミナー案内を
お届けします
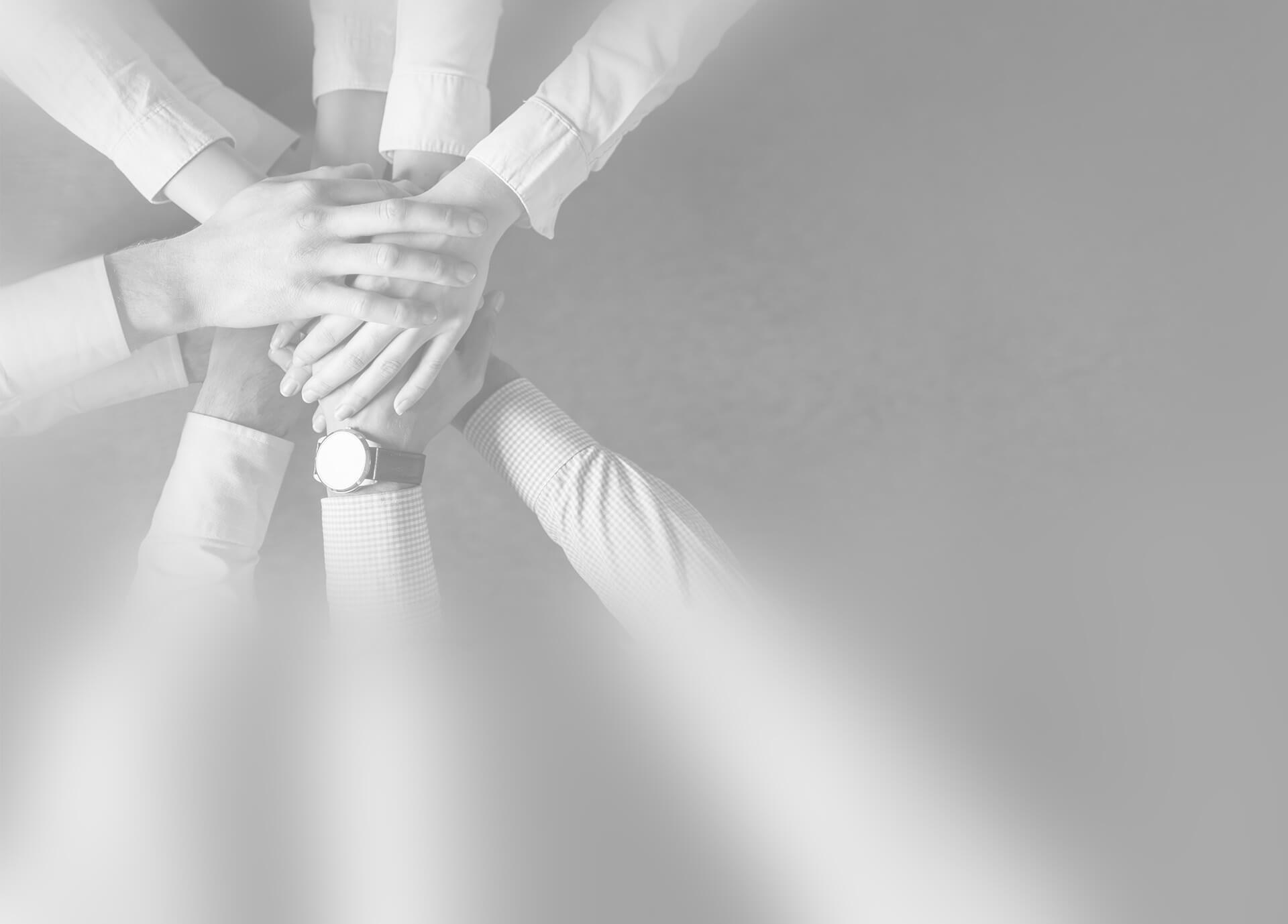