中国の武漢で始まった新型コロナウィルスが全世界で猛威を振っており、経済や産業活動が各所で停滞しています。各国市場では販売の低迷とともに、供給側の問題も明らかになってきました。特に中国、アジアで製造する自動車、電子機器、電子部品などの業界では生産を停止した工場が多く、サプライチェーンの寸断が発生しました。日本国内でも主に中国から部品が調達できず、生産停滞の影響が出ています。
他国よりも早く新型コロナウィルスの鎮静化に成功した中国では、事業継続を優先した取組みが実施されつつあり、この際、サプライチェーンや在庫の可視化や設備のモニタリング、少ない要員で実施するための遠隔操作や自動化などの装備が進んでいます。世界的なウィルスの鎮静化には1年以上かかると見られますが、その期間の各企業の取組みは、デジタルトランスフォーメーション(DX)やスマート化を否応なしに推進したものになると予想されています<1>。そこで本コラムでは、DX,スマート化について積極的に取り組んで行きます。今回は、まずEAM(企業の資産管理:Enterprise Asset Management)システムのこれまでの動向と今後の展望について検討してみます。
1.EAMシステム開発の経緯
EAMシステムは、1980年代に導入された設備保全管理システム(CMMS :computerized maintenance management system)の拡張として開発されました。保全担当組織が保有する資産の数が増えるにつれて、確実な資産管理手順を確立する必要性が生じ、1990年代にITテクノロジーが普及したことから、ITを活用したEAMソリューションが登場しました。
多くの企業は、従来の保全と資産管理が部門単位で処理されるのではなく、EAMシステムにより企業全体で共通管理することが最も効果的であることを認識しました。2010年頃から生産設備・システムへのモノのインターネット(IoT)、クラウド、AIの普及により、さらにEAMシステムへの要求が高度化しており、様々な業界の企業が次世代のEAMシステムを構築する状況になっています。
メンテナンス(保全)は1940年代から段階的に発展してきた歴史があり、4つの世代が考えられますが、EAMシステムは、第3世代メンテナンスから導入されました。これからメンテナンス戦略と次世代のEAMシステムを検討する場合、第1~4世代のメンテナンス手法をすべて活用することから、メンテナンスの発展の経緯について考えてみます。
メンテナンスの発展経緯と世代
メンテナンスの世代は様々な機関が説明していますが、次世代のメンテナンスを語る上で最も引用されているMoubray<2>に第4世代の資料を加味して検討します。メンテナンスの発展経緯と世代を表1にまとめました。
まず、第1世代メンテナンス(第二次世界大戦までの期間、~1945)は、各産業は高度に機械化される以前の時代であり、設備の構造は単純だったことから、設備の故障防止の優先順位は高くなく、簡単な清掃や維持サービス、基本的な修理の実施によりメンテナンスを実施していました。メンテナンスの高度なスキルも必要ありませんでした。
設備が故障した場合に修理する改良保全(Corrective Maintenance)が中心でした。
しかしながら、第二次世界大戦の戦時景気で、あらゆる商品需要が拡大し、産業労働力の供給が逼迫したことから、設備投資が盛んになり、ダウンタイムの削減が必要になりました。
1950年代では様々なタイプの設備や機械の複雑化とともに、故障時の修理の難易度が上がり、ダウンタイム削減のための保全管理が重要になってきました。この時期から始まった第2世代メンテナンス(1945~1980年頃)では、機器の故障は防ぐことができるとし、防ぐべきであるという考え方のもとで、予防保全(Preventive Maintenance)が主流になりました。1960年代には、保全は一定間隔で行われる機器の予防保全やオーバーホールで構成されていました。この結果、メンテナンスコストは、その他の運用コストに比べて急激に上昇し、保全計画を作成して保全を実施する方法が普及しました。また保全作業を管理するシステムの必要性が指摘されました。この世代で、メンテナンス管理の基本的な方法が確立しており、現在でも継承されています。第2世代の後半では、固定資産である資本量と、その資本コストの急激な増加により、企業は資産寿命を最大化させる方法を模索し始めました。
時期 | 第1世代 | 第2世代 | 第3世代 | 第4世代 |
---|---|---|---|---|
第二次世界大戦まで~1945 | 1945~1980 | 1980~2010 | 2010~ | |
保全への要求 | 機器が破損した場合の修理 |
|
|
|
主な環境 | 機械化されていない。 設備の構造は単純 |
機械化が進展。 設備の構造が複雑化 |
各産業でジャストインタイムの導入コンピュータ、IT(~2000)、エキスパートシステムの導入 | IoT、クラウド、AI、アナリティクスなどスマート技術の普及 |
|
||||
保全方法 | 改良保全 |
|
|
状態監視、PHMを導入、予知保全(PdM)を中心とし、従来手法との最適構成 |
1960年代から1970年代に、鉱業、製造業、物流部門では、ダウンタイムが生産量の削減、運用コストの増加、顧客サービスへの悪影響を引き起こし、問題になっていました。
一方、製造業ではトヨタが1970年代から導入したジャストインタイムが成功すると、1980年代に米国の製造業で盛んに導入されるようになりましたが、ジャストインタイムは仕掛品在庫が減るため、生産設備の小さな故障でも工場全体が停止する可能性が高くなるといった欠点がありました。このため、ダウンタイムを回避する必然性が増し、信頼性と可用性が重視されるようになりました。企業が設備の装備とサプライチェーンの高度化を実施した結果、運用コストと所有コストが増大し、投資回収を最大化するためには総支出の一部として維持コストの削減と設備の高いパフォーマンスを維持することが必要になりました。
こうした背景のもとで、当時のコンピュータ技術を導入した設備保全管理システム(CMMS)が採用され、さらに1990年代のITテクノロジーの普及とともにEAMシステムが普及しました。そこで、第3世代メンテナンス(1980年頃~2010年)は、コンピュータおよびITによる設備保全の高度化が実現した世代と言えるでしょう。ICTによる産業革命とされる第3次産業革命がこれに当たります。この時期、コンピュータ技術を活用した状態監視とともに故障モードと影響分析(FMEA、FMECA)による信頼性中心保全(RCM:Reliability Centered Maintenance)が開発され、予知保全(PdM:Predictive Maintenance)が試行されました。
さらに2010年頃より、IoT、クラウド、AI、アナリティクスなどスマート技術の普及を背景に、産業界は第4次産業革命に取り組んでおり、第4世代メンテナンス(2010~)はメンテナンス4.0と呼ばれて、第4次産業革命の重要なコアとして発展しつつあります<3><4>。
第4世代では、IoTから人も含むあらゆるものが接続されるIoE(Internet of Everything)を志向し、相互接続性、欠陥除去、国際標準(ISO 31000、ISO 55000)の採用による標準化、再生可能エネルギー、社会的責任、環境や経済的リスクの管理に重点を置いています。
メンテナンス手法では、データ分析による予知保全(PdM)を中心とし、余寿命(RUL:Remaining Useful Life Prediction)を予測して保全アクティビティを決定するPHM(寿命予測と健全性:Prognostics and Health Management)を取り入れて、従来の手法と合わせて、信頼性、長寿命化、可用性、コスト削減など複数の目標に対して、メンテナンスの最適化を図る方法が採用されました。
また第4次産業革命は、「工場や企業レベル、サプライチェーンでのリアルタイムの状態把握と分析」、「資産、プロセス、リソース、製品の仮想世界(CPS:サイバーフィジカルシステム)のトレーサビリティを実現した需要と供給の最適化」を目指しており、あらゆる無駄、エネルギー、計画外のダウンタイムの削減の実現を前提条件としています。
CMMSからEAMへの展開
第3世代では、1980年代からコンピュータ技術により、CMMSの導入が始まりましたが、特定領域の個別システムに過ぎませんでした。複数の個別CMMSが導入されると、次第に資産管理の高度な目標に対応するため、これらを統合する必要が出てきました。そこで、90年代に広域で、さらに全社的に資産管理を実施するため、EAM導入が始まりました。CMMS各パッケージも独自に進化していますが、初期のCMMSとEAMの違いを整理すると概ね、表2のようになります<5>。
表2 CMMSとEAMの違い(<5>より作成)
CMMS(設備保全管理システム:computerized maintenance management system) | EAM(企業の資産管理:Enterprise Asset Management)システム | |
---|---|---|
対象部門・領域 | 単一の「サイト」 | 企業全体 |
管理対象 | 狭いフォーカス(作業管理) | 総資産管理機能 |
システム構築の特徴 | カスタムビルド | パッケージソリューション |
変更が困難 | 簡単にカスタマイズおよび設定 | |
利用できる機能 | その都度、機能を追加 *CMMSパッケージによっては、その後、多様な機能を用意している |
組み込みメニューとして、統合予測保全 (PM)、状態ベースの監視(CBM)、信頼性中心保全(RCM)機能を使用して展開。 モバイル労働力; 計画ソリューション。 ドキュメント管理ソリューションなど |
企業の担当者、組織 | 対象部門の明確なリーダー | 多くの一般的な機能組織 |
システム連携 | 他のビジネスアプリケーションとの連携が困難 | 各システムとの連携、ERPシステムとの統合 |
初期のCMMSは、特定の狭い範囲の作業管理を対象として、独自のビジネス仕様に合わせてカスタム構築されましたが、システムの変更が煩雑で、他のビジネスソリューションとの連携が困難な状態でした。そこで、保全管理ソリューションの各ベンダーは、これを総資産管理機能に拡張し、カスタマイズを設定などの方法で単純化し、周辺システムやERPと連携可能なパッケージソリューションを開発して提供するようになりました。これらは一般的にEAMシステムと呼ばれています。
CMMSは、作業指示の開始、必要なリソース、処理、終了からなる作業管理に焦点を当てる一方、EAMでは、最新の資産管理手法を取り入れており、データベース内の豊富な履歴情報を利用して、保全効率を改善する各種の手法、たとえば、統合予測保全(PM)、状態ベースの監視(CBM: Condition Based Monitoring)、信頼性中心のメンテナンス(RCM)、保全担当者がモバイルで利用できるソリューションを備え、最適な修理・部品交換を実施するための支援機能を備えています。
資産管理システムの統合
IBM Maximo、Maximo Base Kit紹介資料
IBM Maximoの概要からMaximo Base Kitのカバー範囲、Maximoを活用した設備管理・作業管理のPDCAイメージと実際の画面を用いて各主要機能の詳細を説明しています。
※「Maximo Base Kit」はIBM Maximoをベースとした短期導入・低価格ソリューションです
2.企業全体の資産管理による財務的効果
次に、全社共通の資産管理システム(EAM)の導入の期待効果を検討してみましょう。図1(a)に示すように、企業が目標とするROIや株主価値/定性的利益を向上させるバリュードライバーは、一般的に①収益/能力、②運用費用、③固定資産コスト、④運転資金のバリュードライバーに分解できます。
保全管理を対象にしたCMMSを活用すると、バリュードライバーでは、①の生産量の増加、②保全作業の費用削減、材料費の削減に効果を発揮しますが、設備や施設など資産を多く保有する企業では、企業全体の資産管理を徹底することにより、バリュードライバー③④でも財務的な効果を発揮することができます<6>。
また、これらのバリュードライバーに直結するKPI(Key Performance indicator)(図1(b))について、各種機関が保全管理の実施効果の統計的な値を報告しています。図中の参考値は、第3世代は、CMMS、EAMを導入する以前の世代(第2世代)と比較した効果、第4世代は、スマート技術を導入する以前の世代(第3世代)と比較した効果になります。それぞれ調査の対象の範囲が異なるため、同列に扱うことはできませんが、今後、新規の保全管理を導入する企業では一つの目安になると考えます。
① 収益/能力
それぞれ概要をご説明しますと、「①収益/能力」では、EAMにより適切な保全管理を行うことで機器のダウンタイムを削減でき、生産量を増加させます。ITICによるグローバル800社を対象とした調査<7>では、ダウンタイムの1時間当たりの損失コストは、98%の企業は$ 1,00,000以上、81%の企業は3,00,000ドル以上、33%の企業は1,00万ドル以上と回答しており、ダウンタイムコストの削減は収益に大きく貢献します。
第3世代でダウンタイムは20%程度削減され(32)、生産量を8~15%増加(31)、第4世代では、設備の状態を常時、監視することから、計画外の停止は50%削減でき(35)、ダウンタイムも最大50%削減(34)といった報告がされています。
安全性の向上/リスクの低減の観点では、本コラム第1回で触れたようにプラントの重大事故数が増加していますが、事故原因の80%以上がヒューマンエラーであり、これをRCM (信頼性中心保全:Reliability Centered Maintenance)などの手法とともにシステムによる業務支援を実施することで、大幅に事故数を減らすことが可能です。大規模事故は、小規模故障から確率的に発生するハインリッヒの法則(コラム第1回参照)に従えば、小規模故障を減らすことが、大規模故障を回避する一つの手法です。第4世代では、設備の状態監視から故障を予測し、加えてRCMによる危険度分類で、大きいリスクの原因になる故障を中心に保全処置を実行することから、最大70%の故障の解消ができると報告されています。(36)
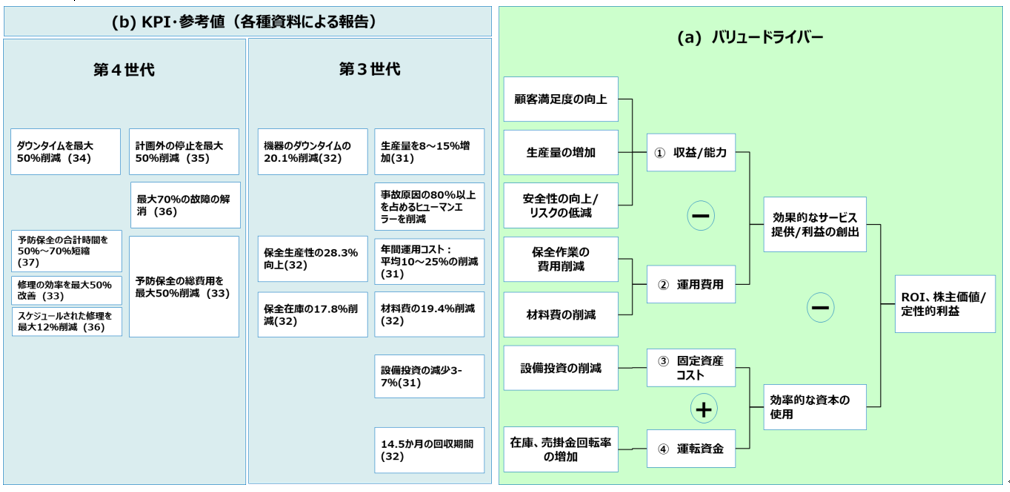
図1: ROIと株主価値に直結するバリュードライバー(各種資料より作成)
参考値の出所
(31):A. T. Kearney調査、Industry Week:保全管理システムを使用している558社の企業対象の平均値
(32):Andrew Meme, Facilities and Asset Management, Business Connect 2015,IBM
(33):Enterprise Asset Management and Field Service Management, ARC Advisory Group, 04/17/2015
(34):James Manyika, Michael Chui, Peter Bisson, Jonathan Woetzel, Richard Dobbs, Jacques Bughin, and Dan Aharon ,Unlocking the potential of the Internet of Things, McKinsey June 2015
(35):JAMES MANYIKA,MICHAEL CHUI, By 2025, Internet of things applications could have $11 trillion impact,Fortune TECHFUTURE OF WORK ,http://fortune.com/2015/07/22/mckinsey-internet-of-things/
(36):G.P. Sullivan, R. Pugh, A.P. Melendez and W.D. Hunt, "Operations & Maintenance Best Practices: A Guide to Achieving Operational Efficiency, Release 3.0," Pacific Northwest National Laboratory, U.S. Department of Energy, August 2010.
(37):Christer Idhammar, Optimize your Preventive Maintenance, articles on Preventive Maintenance,IDCON Inc., http://www.idcon.com/resource-library/articles/prenevtive-maintenance/528-optimize-preventive-maintenance.html
② 運用費用
企業の運用費用のうち、保全に関わる運用費用は、保全作業の費用と予防保全や修理のための材料費用に分けられます。ダウンタイムの回避や故障数を最小に抑える最適な保全方法を適用し、システムにより保全作業を管理することで、運用費用が削減できます。
第2世代(~1980年頃)まで、保全方式は改良保全、オーバーホール、予防保全が実施されていましたが、米国連邦航空局(FAA)などが、6つのタイプの故障率曲線を明らかにし、オーバーホールが逆に信頼性を低下させるパターン、使用期間ごとに保全を実施する予防保全が有効なタイプ、無効なタイプが判明してきました。
実際には、設備や機器ごとの故障率曲線のタイプを特定するには長期間がかかるため、従来通りの保全方法を実施している企業が多く、無駄な作業になっている可能性があります。また予防保全の効果がある場合でも、保全を実施する頻度が多すぎる、いわゆるオーバーメンテナンスになりがちです。
第2世代の条件では、予防保全費用の30?40%は、故障の影響がほとんどない設備に費やされており<8>、また保全作業全体の45%が無効である<9>と報告されています。第3世代では、システムにより過去の作業履歴、センシングデータを分析して予知保全に移行します。この結果、効果のない保全の削減、適正な保全期間によるオーバーメンテナンスを実施し、保全の生産性28.3%向上(32)、保全費用を平均10~25%(31)が実現されたと報告されており、さらに第4世代では、予知保全の精度向上と最適な保全処置を実施することで、予防保全の費用を最大50%削減できたとしています(33)。この保全方式の特徴と故障曲線との関係は、別途のコラムで検討します。
③ 固定資産コスト
固定資産の観点は、設備の寿命を延ばす適切な保全管理方法により設備投資期間の間隔を広げ、従来の方法による設備投資と比較して設備投資費用の削減に寄与できます。第3世代の手法では、設備投資の3~7%削減が報告されています(31)。第4世代では、設備の状態監視、劣化モデル、統計分析を組み合わせたPHMを採用することで、設備の寿命を延ばす取組みがされています。
④ 運転資金
運転資金の観点では、EAMなどのシステムによる管理方法により、過剰な在庫と備蓄を制御でき、組織の固定資産投資を削減し、純利益に貢献できます。
保全管理のパフォーマンスの指標
図1(a)のバリュードライバーは、財務に関する結果としての業績指標になりますが、この結果指標を改善するためには、保全活動を改善してゆく必要があります。全社にEAMを導入した企業は、保全活動を先行指標、結果指標(図1(a)のバリュードライバー)を遅行指標として業績評価指標を設定し、保全業務改善のPDCAや投資意思決定の判断材料に活用しています(図2)。
業績指標は、財務の観点以外にも安全性、可用性、信頼性、保全性(RAMS)の観点で設定するケースもありますが、これらの観点で運用する手法は、メンテナンス・パフォーマンスメジャーメント(MPM)と呼ばれて様々な業界で工夫されています。
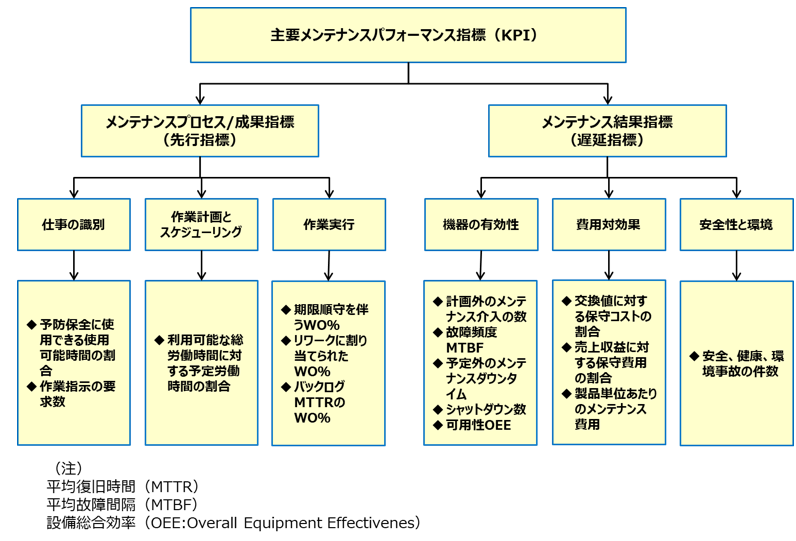
図2: 主要メンテナンスパフォーマンス指標の枠組み <10>より作成
IoT時代到来 予知保全への挑戦
参考文献
<1> John Robinson, What is the future for Industry 4.0 in the post Covid-19 paradigm?, 2 Apr 2020,The Manufacturer
<2>Moubray, John,Reliability-centred maintenance: [RCM II]. Second edition. Oxford: Butterworth Heinemann, 1997
<3>Giovanni Campanella, Why predictive maintenance is fundamental in Industry 4.0, Electronic product , 09/05/2018, URL:https://www.electronicproducts.com/Internet_of_Things/Why_predictive_maintenance_is_fundamental_in_Industry_4_0.aspx
<4>Mirka Kans,Diego Galar, The Impact of Maintenance 4.0 and Big Data Analytics within Strategic Asset Management,6th International Conference on Maintenance Performance Measurement and Management, 28 November 2016, Lulea, Sweden.
<5>Don Barry, Brian Helstrom, and Joe Potter Original by B. Stevens, Chapter 5 Information Management and Related Technology, ASSET MANAGEMENT EXCELLENCE - Optimizing Equipment Life-Cycle Decisions, SECOND EDITION,CRC Press Taylor & Francis Group,2011
<6> IBM Corporation, Understanding the impact and value of enterprise asset management- Make smarter decisions about your assets using the Internet of Things and artificial intelligence, Watson IoT white paper,April 2019
<7>Laura DiDio, ITIC 2017 Hourly Cost of Downtime and Minimum Reliability Requirements Survey, June 2017,ITIC
<8>Deryk Anderson, Reducing the Cost of Preventative Maintenance, Oniqua Enterprise Analytics, Aug 13, 2018
<9>T.A. Cook, Maintenance Efficiency Report 2013, August 2013.
<10>Kumar, U., Galar, D., Parida, A., Stenstrom, C. and Berges, L. (2013), "Maintenance Performance Metrics - A State of the Art Review", Journal of Quality in Maintenance Engineering, Vol. 19 No. 3, pp. 233-277
執筆者紹介
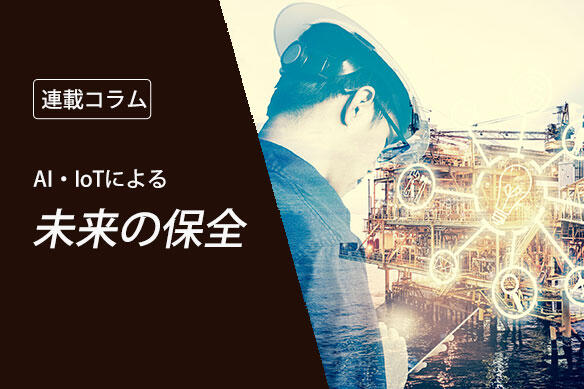
連載コラム AI・IoTによる未来の保全
わが国は、社会インフラ、多くの産業の成熟化、高齢化、少子化に伴う人口構成の変化から、先進国でも未経験の未来を迎えようとしています。戦後から50年以上建設を続けて来た社会インフラはもとより、製造業では高度成長期に花形産業だった大規模プラント、工場が建設時期の順に老朽化を迎えており、事故の発生件数が増加しつつあり、いずれ活用できなくなる時期が目前に迫っています。労働力人口の急激な減少加えて、ベテラン社員の退職によるノウハウの喪失が顕著になっており、災害後の早期の復旧ができないどころか、施設や設備を維持することも難しくなることが容易に予想できます。
従来、資産管理(アセットマネジメント)は、資産を維持するコストで見る傾向にありましたが、本来はISOで定義されているように設備稼働維持のPDCAの運用で見るべきであり、近年、国家や産業の成長が見込めない中で、既存の資産(アセット)を如何に効率的に維持しながら利用できるかといった観点が見直され、必要不可欠な経営手法と注目されています。
本コラムでは、近年、盛んに導入されているデジタル化や欧米で盛んに取り組まれている第四次産業革命のコアとなっている設備保全手法も含め、次世代の保全のあり方について議論します。
関連コラム
関連ソリューション
関連事例
お問い合わせ
CONTACT
Webからのお問い合わせ
エクサの最新情報と
セミナー案内を
お届けします
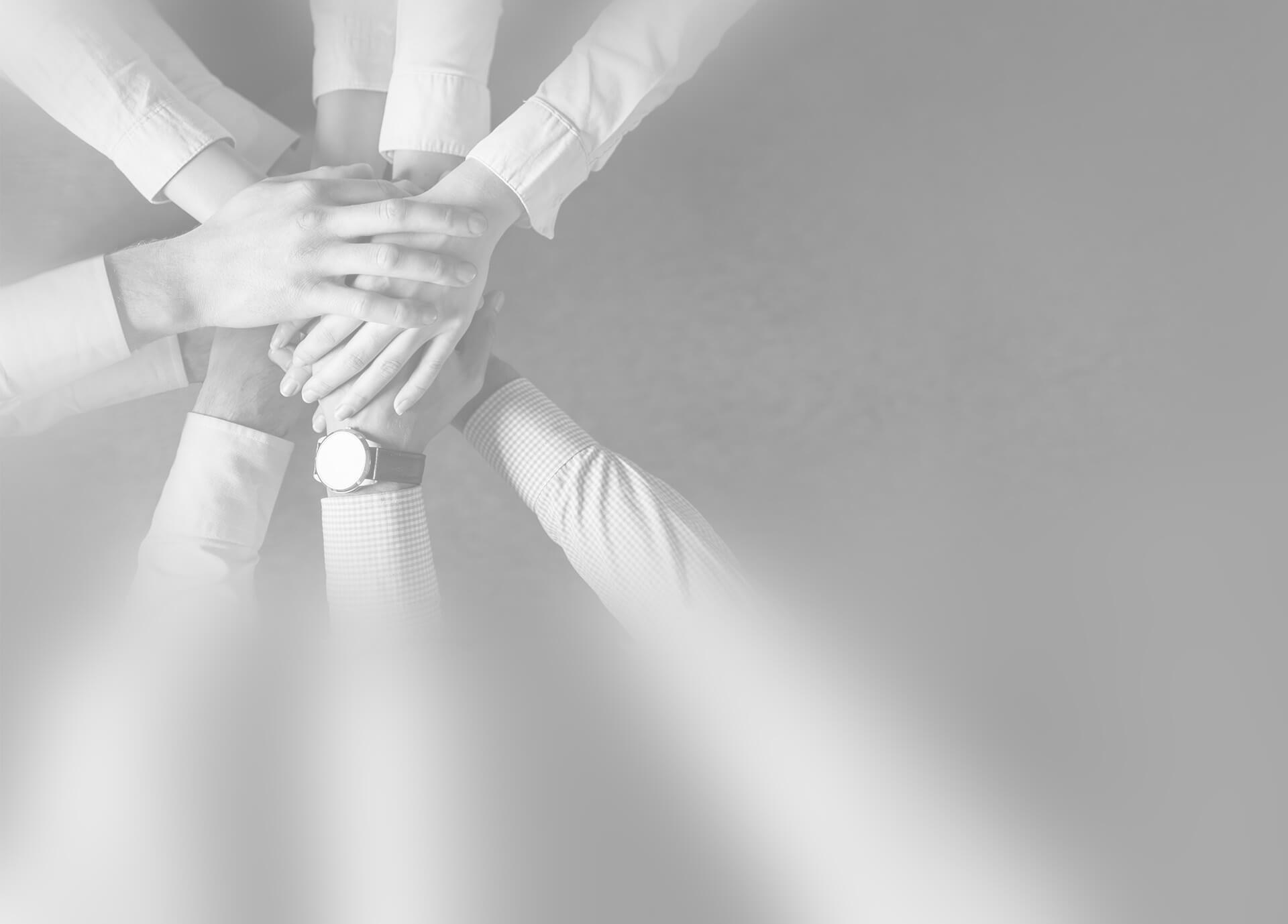