(3)設備のライフサイクルと保全業務におけるPDCAサイクル
策定した保全計画に沿って詳細な保守作業が実施されますが、保全対象となる設備・機器は、いずれも設備・稼働、点検、修理・保守、改修(あるいは廃棄)のライフサイクルがあり、時間とともに、刻々と状況が変化します。そこで、運転実績、計測情報の収集、分析を行い、対応策を検討して、次の保全作業に反映するPDCAサイクルを運用する必要があります(図3)。
PDCAサイクルは具体的には、保全計画に従って、1.Plan:作成した作業指示を提示、2.Do:作業を実施し、作業結果登録、点検/運転実績結果、不具合・原因・対処、作業員/資材/コストの情報登録、3.Check:作業実績情報から、KPIを定義し、故障原因分析、ダウンタイム分析、コスト分析、PM・CM比率、などの保全分析を行う、4.Action:分析結果から計画保全化検討、作業標準化検討、水平展開検討、保全周期の健全性評価、次年度作業見積り、次の活動を作成する、といった4つのアクションから構成されます。
こうした保全のPDCAサイクルは、その企業で設定した標準保全管理プロセスを確実に運用することで、登録された情報、分析情報をすべて記録し、常に現状の状態を把握し、活動の継続性が保証されていることが可能になるのです。
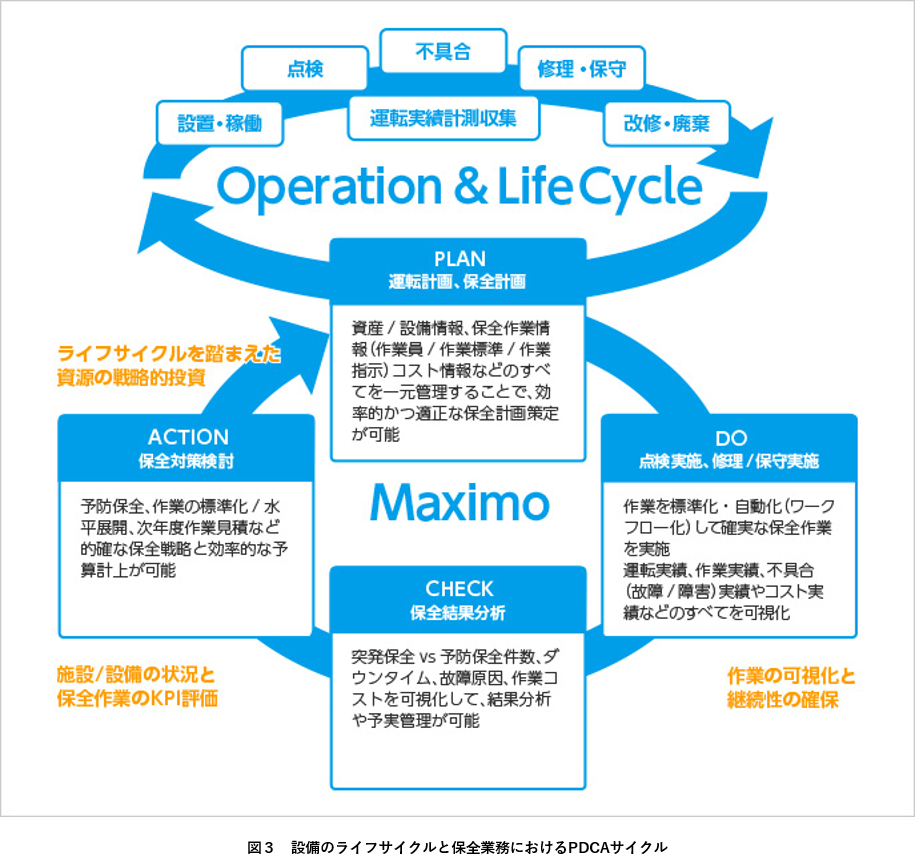
(4)保全のコストパフォーマンス向上
多くの企業では、保全方式としては「故障や事故が発生してから対応する事後保全」と、「一定の間隔で点検や部品交換を行う時間基準保全(TBM:Time Based Maintenance)」を実施し、故障による設備稼働率の低下や操業停止を回避してきました。しかし、時間基準保全は設定した期間ごとに、故障していない設備の点検・補修、部品交換を行うため、保全コストが必要以上にかかり、一定期間に計画した箇所をすべて点検するため、設備を一時的に停止することで稼働率に影響がありました。この背景には、故障分析の結果から簡単には故障予知ができない問題があり、この保守の周期が妥当かどうか判断できない、計画的に廃棄できていない、といった問題がありました。
しかしながら、近年、IoT、アナリティクスの普及により、様々なセンシングを行い、豊富な実績データを基に分析・予測を実施して、予知分析、保全効果、予実結果の分析ができ、資産価値を判断することが可能になりつつあります。すなわち、時間基準による予防保全から、設備の状態センシングにより、故障を予知して保全する状態基準保全(condition-based maintenance)への展開です。これにより、保全コストの抑制と信頼性の確保のバランスが取れた保全を目標とすることが可能になってきました。
IBM Maximo、Maximo Base Kit紹介資料
IBM Maximoの概要からMaximo Base Kitのカバー範囲、Maximoを活用した設備管理・作業管理のPDCAイメージと実際の画面を用いて各主要機能の詳細を説明しています。
※「Maximo Base Kit」はIBM Maximoをベースとした短期導入・低価格ソリューションです
(5)保全業務の効率化、高度化
第1・2回では、保全を実施する人材の年齢構成のアンバランスの問題やノウハウをもつ熟練人材が定年退職を向かえることで、保全ノウハウを喪失する問題を挙げました。保全の現場では、近年の人材確保の難しさから、IT活用による保全業務の効率化が志向されており、保全ノウハウの維持に観点では、AIを活用した取組みが進んでいます。
従来、現場で点検、検査業務を実施し、建屋に戻り、端末入力など報告作業のデスクワークを実施していましたが、モバイル端末を使い、現場で作業ができるようになりました。また複雑な点検、検査業務では、モバイル端末から現場で必要な情報にアクセスすることができ、オフィスへ関連資料を取りに戻る手間が省けるようになっています。
過去の保全対応記録やノウハウをIT基盤に一元管理すれば、AIが作業の必要性に応じて適切な情報を提供する仕組みを使えば、過去のトラブル情報から類似問題の情報入手や、未熟な人材でもベテラン人材の作業ノウハウを現場で入手し、適切な対応作業を実施できます。定型業務では、保全担当者が作業進捗をモバイル端末に音声で伝えると、AIが音声で作業指示を行うといった仕組みも可能になっています。こうした環境があれば、ベテラン要員が退職した後でも、残された現行の保守要員のスキルインベントリーを基に効率的に作業員のチーム編成ができます。
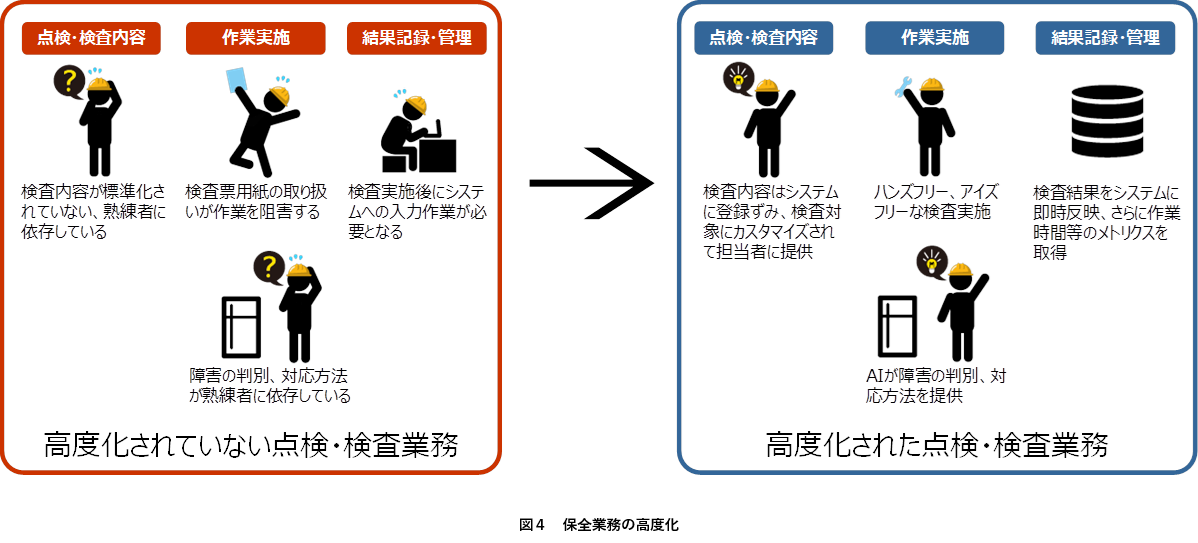
(6)IT基盤による次世代の設備保全システムの実現
装置産業の設備保全の問題解決の3つの方向性として、「設備に関わるヒト、モノ、カネ、情報の総合的な管理」、「保全管理業務の標準化・基準の統一・徹底」、「ノウハウを蓄積、活用できる仕組みの構築」が重要であると記述しました。
これらを実現する仕組みが、Enterprise Asset Management(統合資産管理)です。部門横断して、設備・予備部品・作業(計画・実績)・コストの情報を統合管理することで、設備保全におけるPDCAの実現のみならず、作業員スキル・資格、外注先の管理、保全プロセス・ルールの統制、設備投資の諸元情報としての活用が期待できます。
また設備情報の発展的な活用として、設備が持つ計測データをリアルタイムに収集し、現場業務を強力に支援する仕組みとして設備の健全性・運転制御に活用したり、非構造化データを蓄積し、異常の要因の分析・予測をシミュレーションすることで、設備予知保全/保守最適化に至る次世代の設備保全のシナリオを実現します。
このような設備の稼働状況・状態管理の仕組みは操業管理で活用されてきましたが、保全の領域においても稼働情報、過去の不具合記録、優先度といった定義を設備毎に評価し、保全方式を決定していく信頼性中心保全の取り組みに必要な情報として活用することができます。(信頼性中心保全の詳細については、別回にてご紹介します)
更に次のステージとして、保全業務におけるの"勘と経験"をAI・アナリティクスを搭載したIT基盤を構築することで、のノウハウの参照・高度技術指示を実行するような取り組みも着目されています。
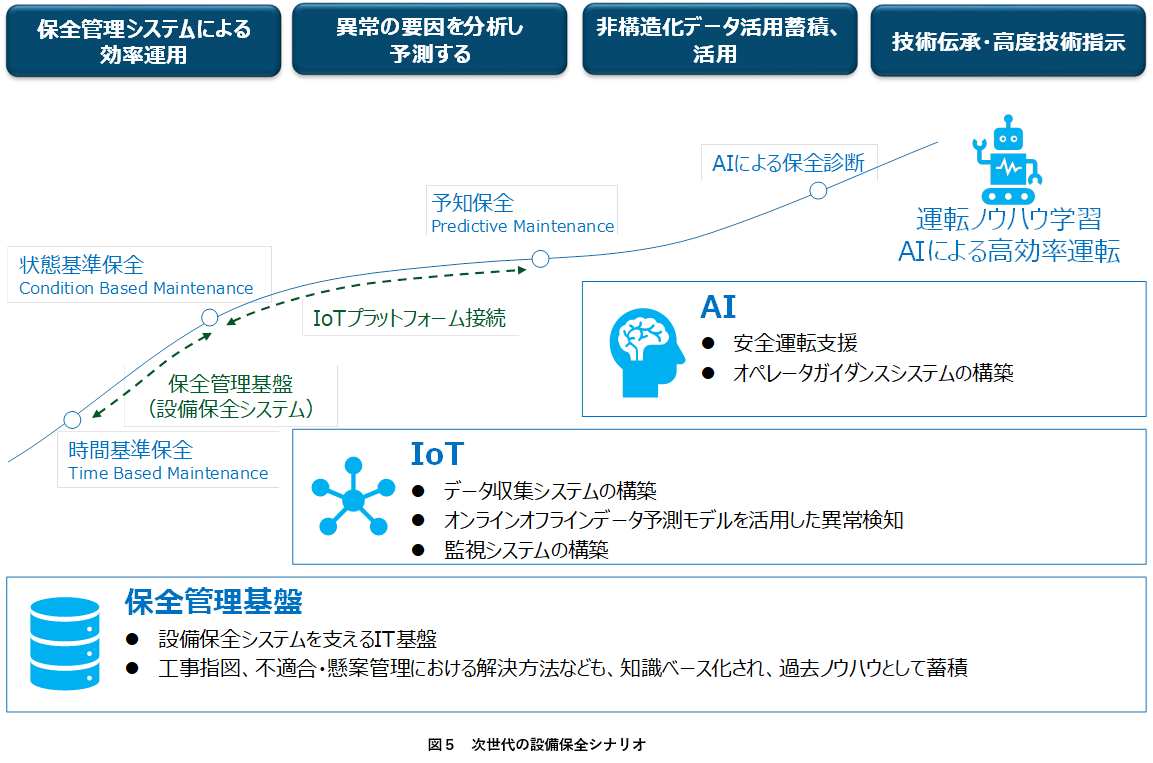
IoT時代到来 予知保全への挑戦
執筆者紹介
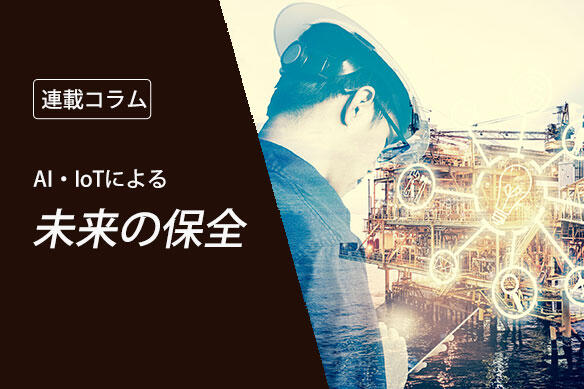
連載コラム AI・IoTによる未来の保全
わが国は、社会インフラ、多くの産業の成熟化、高齢化、少子化に伴う人口構成の変化から、先進国でも未経験の未来を迎えようとしています。戦後から50年以上建設を続けて来た社会インフラはもとより、製造業では高度成長期に花形産業だった大規模プラント、工場が建設時期の順に老朽化を迎えており、事故の発生件数が増加しつつあり、いずれ活用できなくなる時期が目前に迫っています。労働力人口の急激な減少加えて、ベテラン社員の退職によるノウハウの喪失が顕著になっており、災害後の早期の復旧ができないどころか、施設や設備を維持することも難しくなることが容易に予想できます。
従来、資産管理(アセットマネジメント)は、資産を維持するコストで見る傾向にありましたが、本来はISOで定義されているように設備稼働維持のPDCAの運用で見るべきであり、近年、国家や産業の成長が見込めない中で、既存の資産(アセット)を如何に効率的に維持しながら利用できるかといった観点が見直され、必要不可欠な経営手法と注目されています。
本コラムでは、近年、盛んに導入されているデジタル化や欧米で盛んに取り組まれている第四次産業革命のコアとなっている設備保全手法も含め、次世代の保全のあり方について議論します。
関連コラム
関連ソリューション
関連事例
お問い合わせ
CONTACT
Webからのお問い合わせ
エクサの最新情報と
セミナー案内を
お届けします
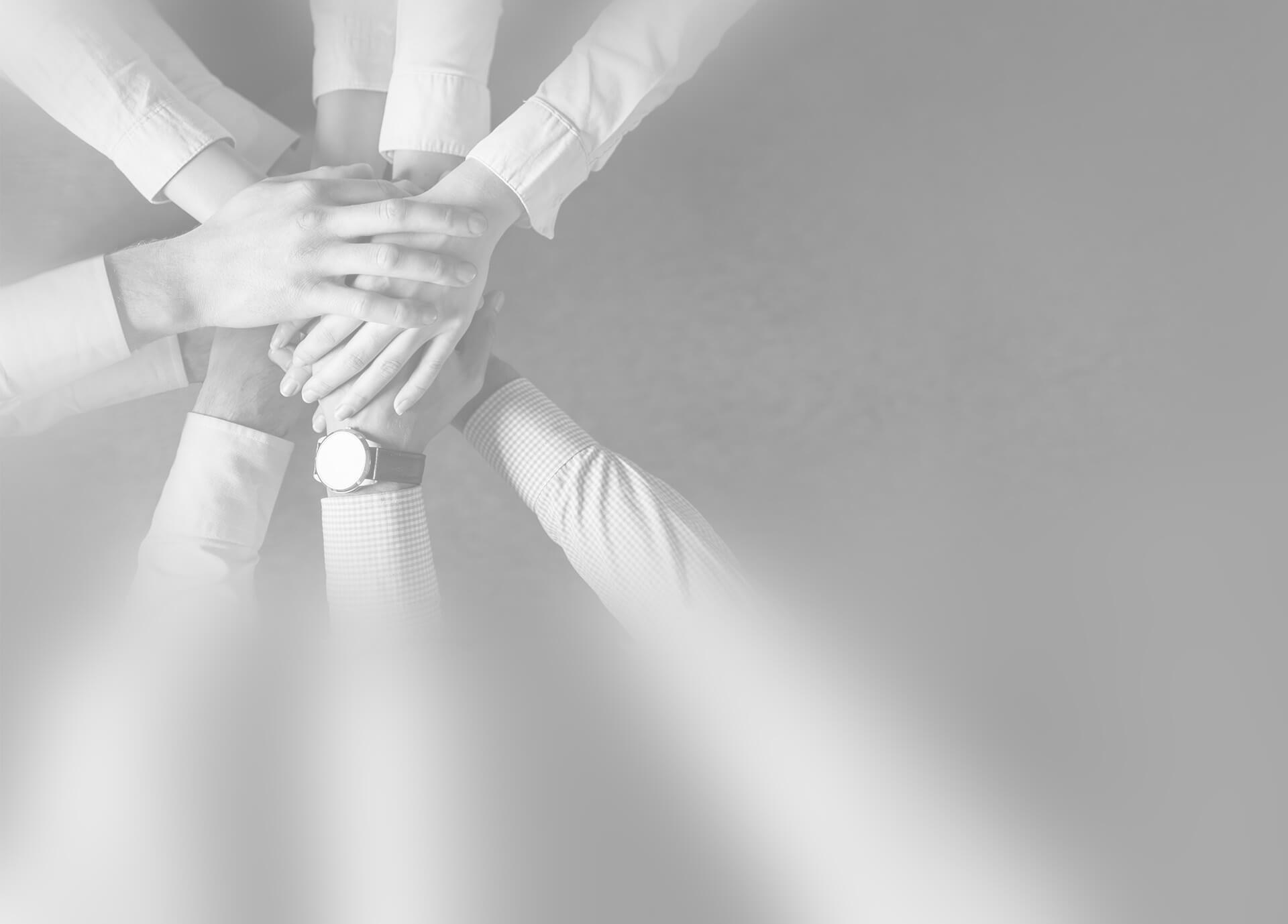