顧客の要望に沿って、独自の仕様で製品を生産する「受注生産」は、在庫リスクを回避し、顧客満足度を高める生産方式です。しかし、納期の長さや手戻りの多さなどの課題もあります。本記事では、受注生産の概要をはじめ、見込み生産との違い、種類やメリット、解決すべき課題を解説します。また、課題を解決するシステム「SPBOM」も紹介します。
受注生産とは
「受注生産」とは、顧客からの発注に従って、製品を生産することです。顧客からの発注を確認してから製品を生産するため、在庫を持たずに事業を展開できる点がメリットです。
また、顧客の要望を聞いてから、具体的な設計を始められるため、カスタマイズ性の高さも特徴のひとつでしょう。一般流通している製品では実現できない、特殊な仕様を希望している場合など、幅広い顧客ニーズに対応できます。
特に、受注生産が積極的に活用されているのは、建築や造船、家具・寝具などの業界です。建築分野では、企業が施主の希望に沿った施工を提案し、詳細を確定してから、注文住宅の生産を開始します。造船も同様に、希望の仕様を確定してから、船を造り始める仕組みです。
家具や寝具は、一点物のオーダーメイドのビジネスモデルがよく利用されます。「洋服を収納する」「睡眠時の身体を支える」などの基本機能は共通していますが、顧客の希望に沿った、デザインやサイズ、素材などの部分のオリジナル作成が多いです。
他に、工作機械や金型においても、受注生産を活用したビジネスモデルがいくつも展開されています。
受注生産と見込み生産の違い
受注生産と「見込み生産」の違いは、あらかじめ在庫を持つかどうかにあります。受注生産は前述の通り、顧客からの発注に従って、その都度製品を生産する方式です。一方、見込み生産は、過去の売上データなどに基づいて事前に需要予測を行い、売れるであろう数量のラインを見極めて、顧客からの発注を受ける前に製品を生産します。
受注生産は、顧客の発注ありきになるため、事前の需要予測や販売計画は行いません。しかし、見込み生産は、発注があるかどうかにかかわらず、自社の生産計画に則って製品を生産する仕組みです。
受注生産と見込み生産はそれぞれ一長一短な部分があります。以下に見込み生産のメリット・デメリットを挙げるので、それらを踏まえて自社に適した生産方式を検討するとよいでしょう。
見込み生産のメリット
見込み生産のメリットは、リードタイムを短縮できる点です。事前に製品を生産して、在庫を確保しておけるので、発注を確認してから製品の生産に入る必要がなく、顧客に対して迅速に製品を届けられます。顧客が必要としているものを即座に提供できるのは、競争上の優位につながる利点です。
また、見込み生産の場合は自社であらかじめ入念に生産計画を策定し、それに沿って効率的に製品を生産できるのもメリットとして挙げられます。受注生産では、生産すべき製品の数量も設計も顧客ありきでその都度調整しなければいけませんが、見込み生産ならば自社でコントロール可能です。こうした利点は製品の品質を一定に揃えたり、人員の配置を常に最適化したりする上で役に立つでしょう。
見込み生産のデメリット
一方で、見込み生産には過剰在庫のリスクもあります。大量の在庫は保管スペースを圧迫し、管理のための人員も多く必要です。そのため、需要予測が外れてしまい、生産した製品が大量に余る事態になれば、大幅に値下げしたり廃棄したりしなければならず、損失が膨らみやすい点がデメリットです。特に進化が著しいテクノロジー関連の製品などは、すぐに技術が陳腐化してしまうので、在庫を抱えることは大きなリスクになります。
上記で挙げた見込み生産のメリットを引き出すには、正確な需要予測と安定した供給先の確保が前提になります。
受注生産に向いている製品
受注生産と見込み生産のどちらを採用すべきかは、製品の特性と需要に大きく依存します。
まず、受注生産は、注文住宅や工場機械のように単価が高く、カスタマイズが求められる製品が適しています。また船舶のように生産数が少なく、製造原価が高いために在庫を持てない製品や、希少性をもたせるために大量生産をする必要がない製品、試作段階の製品なども受注生産向きです。
身近なところでは、家具や寝具なども受注生産に比較的適しています。これらは自分の好みや設置する部屋の都合にあわせてサイズやデザイン、素材などをカスタマイズしたいという需要を一定以上見込むことが可能です。スーツやドレスといったフォーマルな服や指輪などの装飾品に関してもオーダーメイドには需要があります。
見込み生産に向いている製品
一方で、大量生産により安価で販売できる衣料品や加工食品などは、見込み生産が適している代表例です。家電や自動車など、ある程度の需要が見込める汎用性の高い製品も見込み生産で製造されています。
また後述するように、受注生産は生産のリードタイムが長いという特性があることから、受注から納品までの期間が短く、スピーディーに納品したい製品は見込み生産が適しています。どれほど緻密な需要予測でも誤差は付きものなので、製造単価の低い製品など、ある程度在庫が残ってもそれほど利益率を圧迫しない製品が見込み生産に適している製品の基本的な特徴です。
生産方式のパターン
工場における生産方式には、受注単位で仕様を決める「個別受注生産」、同じ図面を繰り返し使用する「繰返受注生産」、一定数量単位で生産する「ロット生産」、単一製品の大量生産が可能な「ライン生産」の4パターンがあります。
以下では、それぞれのパターンの特徴や、メリット・デメリットを解説します。
個別受注生産
受注単位で仕様を取り決めて、製品を生産する方式です。製品のプロトタイプを製作したり、多品種少量生産を行ったりするシチュエーションにおいて、個別受注生産が採用されるケースが多いでしょう。
受注単位で設計の内容が異なるため、発注があるたびに顧客から図面の提供を受けたり、自社で設計したりすることが一般的です。ただし、製品を作るのに欠かせない一部の原料や部品は、過去の図面の仕様と重複する場合も考えられます。
メリットは、顧客の要望に沿った、柔軟な生産が可能である点です。発注元の顧客のために、世界にひとつしかないオリジナルの製品を生産する性質上、細かい要望を汲み取って反映できます。
一方で、顧客から発注を確認してから、生産スケジュールを作成するため、納期の見通しを立てにくい点や、リードタイムが長くなりやすい点はデメリットです。
繰返受注生産
すでに決められた製品の仕様に則って、受注生産を繰り返し行う生産方式です。製品の製造に使用する図面は、受注時に顧客から提示されるケースと、顧客からの依頼によって自社が独自に設計するケースの、2パターンに分かれることが一般的です。
名称にある「繰返」の通り、2回目以降の製造においても、1回目と同じ図面を何度も繰り返し使用して、ひとつの製品を生産し続けます。製造業の多くは、繰返受注生産を採用しているケースが多く見受けられるでしょう。
メリットは、同じ図面を何度も使用するため、生産コストを抑えられる点にあります。特にロングセラー商品は、長期間にわたって、安定的に同じ生産サイクルを継続できるので、生産の効率化を図りやすく、生産スケジュールの変化も少ないことから、納期の見通しも立てやすいです。
ただし、決まった図面を使い続けるため、急な仕様変更への対応は難しく柔軟性が低い点が、デメリットとして挙げられます。
ロット生産
ロット単位で製品を生産する方式です。「ロット」は数量の単位を表す言葉で、ロット生産では1種類の商品を特定数量ごとに生産します。例えば、ひとつの図面から1種類のTシャツを生産するときに、「1ロット=1,000枚」と取り決めた場合は、1回の生産で1,000枚のTシャツが作られる仕組みです。受注生産と見込み生産の双方において利用でき、「バッチ生産」とも呼ばれます。
ロットの数量は一律ではなく、製品の種類や性質によって、個々に決められます。1回の生産で同じ製品を大量に作れるので、利益率を高めやすい点がメリットです。一般的には、ロット数が大きいほど、製品1個あたりの単価を下げられます。
一方で、最小ロット数を小さくした場合、生産ラインの切り替えが何度も発生し、生産効率の低下を招く可能性が高いです。逆に、最小ロット数を大きくした場合、過剰在庫の原因になるため、適切な最小ロット数の見極めが重要でしょう。
ライン生産
工場のベルトコンベアに製品を流して、部門別に製品加工と検査を行う生産方式です。ベルトコンベア上で、次々と作業を行う性質から、「流れ作業」とも呼ばれます。
単一製品の大量生産に長けているため、事前に需要予測を行って、製品を生産し在庫を確保する、「見込み生産」に向いている方式です。特に、自動車業界や製薬業界など、1種類の製品を長期的に製造し続けなければならない現場において、積極的に活用されています。
大量生産に適している反面、トラブルひとつで、生産プロセス全体に影響を及ぼす点がデメリットです。各部門が流れ作業で製造作業を行うので、ラインが停止すると、リードタイムが大幅に増大したり、納期遅延を引き起こしたりするおそれがあるでしょう。
受注生産のメリット
受注生産の強みとして、「在庫を持たずに運用できる」「顧客満足度を高めやすい」の2点が挙げられます。それぞれの強みについて、詳しく解説します。
在庫を持つ必要がない
顧客からの発注に基づいて製品を生産するので、常に「需要=受注数」の図式が成り立ちます。見込み生産のように、あらかじめ製品を生産して、在庫を確保するスタイルを取らないため、過剰在庫による廃棄リスクがなく、在庫保管コストもかからない点が強みです。
見込み生産による過剰在庫が生じると、まずは大幅な値引きを行って、赤字の拡大を防ぐ措置を取ることが考えられます。しかし、それでも売れ残った場合は、廃棄せざるを得なくなり、廃棄コストがかかって、利益を出すどころか損失を拡大させる原因になります。受注生産なら、このリスクの回避が可能です。
また、見込み生産によって事前に生産した製品は、発注を受けるまでの間に、保管するスペースが欠かせません。倉庫の契約料や光熱費、倉庫担当者を配置する際の人件費など、在庫保管コストを削減できる受注生産は、利益率の向上につながるでしょう。
顧客満足度の高い製品が作れる
顧客の要望を細かく反映できるので、顧客満足度の高い製品を作れる点に期待を持てます。
近年では、市場における顧客ニーズの多様化が進んでおり、企業は自社ならではの独自性を追求して、競合他社との差別化を図ることが求められています。重視されている点は、従来のように品質の高さだけではなく、「商品が顧客にとって、どのような価値をもたらすのか」です。
見込み生産のような、テンプレートに沿った大量生産は、顧客に対して、安定的な品質の製品を提供し続けられる点では効果的ですが、他社との差別化を図りにくく、市場における独自性を押し出す点が難しい生産方式です。市場での受注生産の活用は、まだ見ぬ新しい価値を提供し、顧客満足度を高める効果を発揮するでしょう。
受注生産のデメリット
納期回答に時間がかかる
見込み生産とは異なり、事前に行う製品の生産とストックが不可能です。発注を受けてから、生産スケジュールを作成して、納期を確定するため、顧客への納期回答に時間がかかります。
特に、個別受注生産においては、製品の詳細な仕様が確定してから、部品の調達を始めたり、生産プロセスの見通しを立てたりする必要があり、納期が確定するまでの期間が長期化しがちです。
顧客になるべく早く納期を伝えることは、顧客満足度を高める上でも重要なポイントです。発注を受けた後、スムーズに納期回答を行える環境に整えなければなりません。
手戻りが多い
同じ図面を繰り返し使用し続ける見込み生産とは異なり、顧客の要望に沿って仕様を確定します。そのため、生産を始める直前や生産開始直後に、「やっぱり仕様を変更してほしい」との要望が入り、手戻りが発生するリスクが高い点が特徴です。
生産を開始した後に手戻りが発生すれば、すでに使用した資材や部品は無駄になってしまいます。また、稼働した工数分のコストがそのまま損失するため、利益の減少につながるでしょう。
他にも、受注生産は見込み生産のように、生産する部品が常に一定ではないため、部品の情報管理が煩雑になりがちです。各部門が、どの製品に何の部品を使用して生産するのかを正しく把握し、連携の取れた生産プロセスを確立しておかなければ、手戻りが発生して損失やリードタイムの拡大に直結してしまいます。
生産のリードタイムが長い
仕様を確定して、納期を明らかにするまでの時間が長く、調達する部品が希少だったり、生産に特殊な技術が必要だったりする場合、さらに長期化してしまいます。リードタイムが長くなればなるほど、工場を稼働するためのコストが増加し、無駄なコストの発生につながりかねません。
また、納品までのリードタイムが長いと、入金までの期間も長くかかります。生産にかかるコストが高ければ高いほど、一時的な支出が膨らむので、あらかじめ生産にかかるコストを想定し、健全なキャッシュフローを心がけた経営が重要です。
見積もりが難しい
生産途中で仕様変更が起こりやすい性質上、正確な見積もりが難しい点も課題のひとつです。受注当初のヒアリングで想定していた仕様より、必要な部品や資材が増えた場合は、生産コストも増加するため、当初の想定よりも利益が目減りする可能性があります。
事情を説明して顧客の理解を得られれば、追加費用を請求できる場合も考えられます。しかし、予算の関係などで追加の支払いが難しいと、生産側が増加分のコストを、丸ごと負担しなければならないケースもあるでしょう。
また、製造する部品の種類が多岐にわたることから、「BOM(部品表)」の管理に手間がかかり、正確な見積もりが難しい背景も見受けられます。
コストがかかる
受注生産は、顧客からの依頼に沿って製品仕様を決め、部品を調達して生産を行います。部品や材料にこだわるケースが多く、同じ図面の使い回しも難しいため、見込み生産と比較して大幅にコストがかかります。製造の途中で仕様と部品の変更を求められ、さらにコストが上がってしまうこともあります。
見込み生産のような在庫管理や保管コストは不要ですが、生産コストの削減は難しいケースが多いでしょう。
BOMの管理に時間がかかる
BOM(Bill Of Materials)とは、製品に使用されている部品を一覧化したもので、部品表とも呼ばれます。品目情報と部品情報、どの部品が何に使われるのかなどを示す構成管理情報で構成されている、極めて重要な情報です。BOMにより、設計情報と品目の関係性が明確になります。
BOMは用途ごとに作成され、設計部門が作成するE-BOM(Engineering-BOM・設計BOM)、E-BOMをもとに製造部門で作成、利用するM-BOM(Manufacturing-BOM・製造BOM)があります。設計部門で作成された後に生産部門に引き渡され、生産管理に必要な情報が加えられます。
製造工程を効率化するためには、これらのBOMをデジタル化し、有効活用することが重要です。しかし多くの企業では、部門によって異なる部品番号を用いていて統合できない、在庫数や内容の認識に齟齬が生じているといった問題があり、連携が難しい状況です。Excelなどを使った独自のフォーマットで管理しているケースも多く、管理に時間がかかっています。
BOMが爆発的に増える
結果的にシステムでの管理が煩雑になり、時間と労力がかかります。手作業では担当者の記憶に頼るなど属人的な対応になりがちです。人的ミスが発生するリスクもあります。
受注生産の課題を解決するシステムSPBOMを紹介
受注生産の課題を解決に導くには、部品表の作成を自動化する「SPBOM」がおすすめです。SPBOMは、BOMの課題を解決するために、株式会社エクサが独自開発したソリューションです。
そもそも、BOMにおける課題が発生する理由は、製品名や仕様・製造の情報が、正しく連携されていない点にあります。したがって、製品情報や生産に必要な情報を集約し、生産に関わる現場担当者が、正確に把握できる環境に整えることが大切です。
従来のBOMは、設計BOMと製造BOMが連携されていなかったり、生産の目的によって管理の粒度が大きく異なっていたりと、管理が煩雑になりがちです。結果的に生産が非効率化し、手戻りの発生による損失の拡大や、生産リードタイムの長期化を引き起こしてしまいます。
SPBOMは、多種多様な規格を持つ製品を、システム上に登録しておけば、製品名と仕様を指定するだけで、「MBOM(製造部品表)」を自動生成できる点が特徴です。仕様に基づいて、自動的に生成する「パラメトリックBOM」なので、受注生産のデメリットである、BOM管理の煩雑さの解消に貢献します。
生産拠点ごとに、生産プロセスが異なるBOMや「BOP(工程表)」にも対応が可能であるため、複数の工場を運用している現場にもおすすめです。受注生産の課題解決に悩みを抱えている人は、SPBOMの導入を検討してみてください。
受注生産の効率を向上!
SPBOMの導入により製造BOMを自動生成することで、従来手作業で行っていたBOMの登録作業を削減できます。カタログにはないオーダーメイドで使う多様な部品表も管理可能です。これにより人件費削減や時間短縮になるほか、煩雑だったBOMの管理やメンテナンス作業も大幅に削減できます。工場・生産ラインごとに異なる製造BOMの生成も可能です。
またシステムが製造に関するルール・ノウハウや仕様情報を一元管理するため、設計BOMと製造BOMとの齟齬もなくなり連携もスムーズです。従来熟練者の知識や経験に頼っていた部分をシステムで管理するため、属人化を解消できる点も魅力です。
BOM管理の効率化だけでなく、今まで時間がかかっていた納期回答の大幅短縮や納期遅れの防止にもつながります。
まとめ
受注生産は顧客満足度の向上や在庫リスクの回避に有効ですが、生産リードタイムの長期化や手戻りの多さなどの課題もあります。課題を解決するためには、BOM情報の整備や設計・製造BOMの連携が重要です。紹介したSPBOMの導入を検討し、スムーズに生産プロセスを行える体制を整えましょう。
BOM管理の効率化を実現させる「BOMシステム」の導入ガイド
部品管理(BOM)の概要やシステムの選定フローなど、BOMの導入に関わる情報を10スライドに凝縮!
BOM管理システムの導入を検討する全ての方へ!
ブログに関するお問い合わせ
関連する記事
関連ソリューション
関連事例
お問い合わせ
CONTACT
Webからのお問い合わせ
エクサの最新情報と
セミナー案内を
お届けします
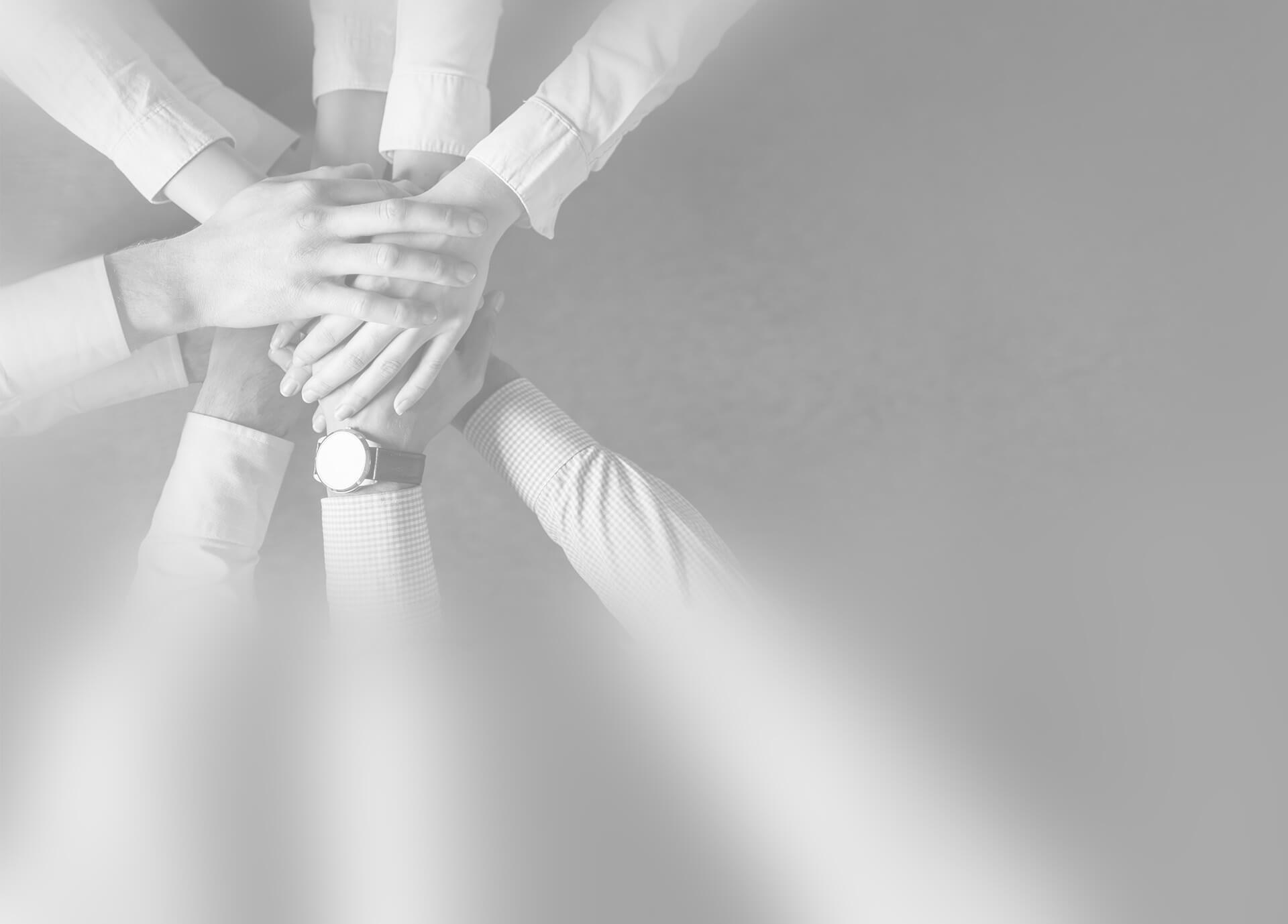