多くの品種を少量ずつ生産する「多品種少量生産」は、幅広い消費者ニーズに対応するとともに、在庫リスクを軽減するための手段として多くの企業で取り入れられています。本記事では、多品種少量生産が求められる背景や導入するメリット・デメリット、さらにBOM管理の課題を解決し効率化を図るソリューションについて解説します。
多品種少量生産とは
多品種少量生産とは、「ひとつの工場内で、多種多様な品種の製品を少量ずつ生産する」生産方式のことです。従来は少ない品種を大量に生産する「少品種大量生産」が一般的でしたが、近年では多くの企業が多品種少量生産に舵を切るようになりました。
- 多品種少量生産の例
商品A~商品Jの10種類を3,000個ずつ生産する
- 少品種大量生産の例
商品A、商品B、商品Cの3種類を10,000個ずつ生産する
少品種大量生産は、事前におおよその需要予測を行い、予測に基づいた生産スケジュールを立ててから製造に取りかかるケースが多い生産方式です。
一方の多品種少量生産は、製造方法や生産プロセス、納期などが一律ではないため、事前に画一的な需要予測を行うことは難しい傾向にあります。少品種大量生産に比べると、製造ラインの管理も複雑になりやすい点が特徴です。
多品種少量生産と個別受注生産の関係
個別受注生産とは、それぞれの受注で異なる仕様に基づき製造する形態です。顧客から受注してから設計を行い、製造します。毎回受注してから製造するため在庫を持たずに済むことや、顧客の要望に応じた製品を提供できることがメリットです。
その一方で、工程が複雑になりやすく生産性を向上しにくい点がデメリットです。試作段階のため小ロットで必要な製品や、多品種少量生産で個別受注生産が行われることがあります。
多品種少量生産が求められる背景
近年では消費者のニーズが多様化しており、「顧客が求めている製品を提供すること」により強く価値が見いだされるようになりました。しかし、これまで一般的だった少品種大量生産は「決まった形の製品を大量に生産する」方式であることから、個々のニーズへの細かな対応は困難です。そこで、多品種少量生産を採用し、消費者ニーズに幅広く応えられる環境を整えようという動きが多くの企業で広まりました。
多品種少量生産は、ニッチ商品も含めて多品種を少量ずつ在庫として抱えておき、より多くの顧客に販売することで売上の合計額を増やす「ロングテール理論」と相性が良い点が特徴です。また近年では、多品種少量生産の考え方を進化させ、大量生産を維持しながら消費者ニーズに合わせた個別受注を実現する「マスカスタマイゼーション」の考え方も広まってきています。
多品種少量生産のメリット
多品種少量生産のメリットには、多様な消費者ニーズに対応できる点や、過剰在庫のリスクを軽減できる点が挙げられます。それぞれ詳しく解説します。
多様な消費者ニーズに対応できる
多品種少量生産を行うことで、デザイン・品質・コストなど多様な消費者ニーズに合った製品を提供できます。
完全な個別生産ではなく「多品種の在庫を少量ずつ抱えておく」という特徴も重要なポイントです。生産プロセスの決まっている部品をあらかじめ在庫しておくことで、ゼロから製品を作り始める必要がなくなるため、消費者ごとのニーズに細かく対応しつつ、製品の製造スピードを高められます。
例えば、ベースとなるパソコンのモデルをいくつか用意しておき、OSやCPU、メモリ、ストレージなどのパーツを自由にカスタマイズするという生産方式も多品種少量生産の一種です。
また、多様な消費者ニーズに応えられれば、まだ開拓されていないニッチな市場をカバーでき、売上アップや顧客満足度の向上にもつながります。
在庫過多のリスクを軽減できる
多品種少量生産は、過剰在庫のリスクを軽減できるメリットもあります。少品種大量生産は「一種類ごとに製品を大量生産して、売れなかった場合は廃棄する」というサイクルが一般的です。そのため、売れなかったときの損失と廃棄コストが膨らみやすく、在庫リスクが大きい点がデメリットです。
一方、多品種少量生産はニーズに合わせて必要な分の製品だけを生産するため、在庫過多に陥りにくく、廃棄を最小限に抑えやすいという性質があります。在庫を持たずに受注した製品だけを生産する「完全受注生産」を採用することも可能ですが、市場のニーズを見極めながら柔軟に在庫数や生産数を調整できる点が優れています。
多品種少量生産の課題
コストが増加する
多品種少量生産では製造時に、多種多様な資材・原料を少しずつ仕入れなければなりません。そのため、少品種大量生産に比べて仕入れコストが高くなりやすい側面があります。
また、少品種大量生産よりも倉庫で管理する品種が多いため、品種別の管理コストが増加する点も考慮する必要があります。特に温度管理や湿度管理などの観点で、厳格さを求められる資材・素材を扱う製品を生産している場合は、管理コストの増加幅が大きくなりやすいため注意が必要です。
生産効率が悪い
少品種大量生産に比べると、多品種少量生産の生産効率は低くなるのが一般的です。一品種あたりの生産量が限られるため、大量に生産するためには自然と生産回数を増やすことになり、多くの人手やエネルギーが必要になることが原因です。
また、製品の仕様が変更されるたびに工場の生産ラインの組み替え作業が発生し、頻繁に生産ラインを停止させなければならないリスクもあります。
新しい生産ラインを軌道に乗せるまでのプロセスをスムーズに行えなければ、生産効率が高まらないまま次々と生産ラインを更新し続ける負のループに陥り、納期遅延やリードタイムの増大を招く可能性もあるでしょう。
納期回答に時間がかかる
多品種少量生産は、顧客一人ひとりに合わせたカスタマイズを行う性質上、納期回答に時間がかかりやすい点も課題です。
同じ形状の製品を大量生産する少品種大量生産は、生産プロセスがパターン化されているため、生産にかかる時間を予測しやすい状況にあります。そのため、顧客からの納期問い合わせに対して比較的スムーズに返答が可能です。
一方、多品種少量生産は注文内容ごとに生産プロセスが異なることも多く、仕入れる資材や原料も製品の内容によって変化します。このことから、正確な納期回答ができるまでに時間を要しやすい性質があります。
製造に時間がかかる
多品種少量生産は製造にかかる期間が長期化しやすい傾向にあります。製造する製品の性質に合わせて生産プロセスを細かく調整したり、生産ラインを組み替えたりする必要が生じて、製造に入るまでの準備にも時間がかかるためです。
顧客満足度を高めるためには、個々のニーズに合致した品質の高い製品を製造することが重要です。しかし、製造に時間がかかりすぎてリードタイムが長期化すると、製造コストが増加するだけでなく、顧客満足度も低下しやすくなるため、品質と製造期間のバランスを取ることが求められます。「製造にかかる時間をどのように短縮するか」という点も課題のひとつです。
多品種少量生産を効率化するには?
受注を分析する
多品種少量生産の効率化には、受注分析が有効です。受注分析とは、製品別に受注パターンを分類することを指します。受注パターンは、次の4種類に分けられます。
- 多頻度大ロット
- 多頻度小ロット
- 少頻度大ロット
- 少頻度小ロット
受注分析は、「頻度」と「ロット」の二つの観点から判断します。頻度は「月に〇回以上生産する場合は多頻度、基準を下回る場合は少頻度」のように定義するのが一般的です。ロットは「1回あたりの受注金額が〇円を超えた場合は大ロット、基準を下回る場合は小ロット」のように定義します。
生産方法を最適化する
分析した受注パターンによって生産方式を最適化することも、多品種少量生産の効率化を図るために重要です。前述の4つの受注パターンに分類すると、生産を効率化するためのポイントが見えてきます。
受注頻度が多い製品の場合、生産ラインの組み換えが頻繁に発生するため、生産効率が低下する可能性が高くなります。予算に余裕があるようなら、設備の増強を図るとよいでしょう。予算の観点から設備の増強が難しい場合は、在庫を多めに持つことで生産回数を減らす施策が効果的です。
ロットは大きければ大きいほどコストを回収しやすい傾向にありますが、小ロットを継続的に受注するのであれば、在庫管理や生産プロセスの見直しによって利益率の向上を図ります。
汎用性の高い部品や販売が見込める製品は在庫をあらかじめ確保する
汎用性の高い部品や、継続的な販売が期待できる製品は、在庫をあらかじめ潤沢に確保しておくと、生産の効率化につながります。
生産のたびに部品を仕入れると仕入れコストが増加し、利益率を低下させる原因になります。また、継続的な販売が期待できるにもかかわらず、注文のたびに生産していては、生産コストに無駄が生じるでしょう。
「よく使う部品」「よく売れる製品」は多めに確保して在庫を持つように意識すると、生産を最適化できます。また、在庫を確保しておくことで、リードタイムの短縮も実現可能です。
段取り替えの回数や時間を減らす
多品種少量生産では製品の仕様に合わせて、装置の設定変更や取り替えが頻繁に行われます。そのため、いわゆる「段取り替え」の回数や時間をどれだけ短縮できるかどうかは、生産の効率化に直結します。
段取り替えを行う際は、生産ラインを停止して段取り替えを実施する「内段取り」と、生産ラインを稼働させながら並行して実施する「外段取り」の二種類に分けて、それぞれの作業を最適化することが大切です。
また、現場の作業員がスムーズに生産を行えるように、工場内のレイアウトを見直したり、業務フローを振り返って改善点を見つけたりする方法も効果的です。
生産管理システムを導入する
生産管理システムを導入することも、生産の効率化に貢献します。生産管理システムとは、工場内のさまざまな製造業務を一元管理できるシステムのことで、生産スケジュールの作成や受注生産品の内容確認、在庫管理、原価管理などを行うことが可能です。
原価管理機能を活用すると、製品の生産にかかるコストを明確に把握できるようになるため、純原価が明らかになります。製品を生産するためにどのくらいのコストがかかっており、販売するとどれだけの利益が出るのかを知ることで、生産効率を可視化できます。
生産にかかるコストを把握できれば、製造原価を見直したり、適正な販売価格を設定したりする際にも役立つでしょう。また、生産ラインにおける課題を発見し、解決に向けた取り組みを行えるようになるメリットもあります。
部品表のルールを見直す
部品表のルールを見直すことも、生産を効率化するポイントのひとつです。部品表(bill of material:BOM)とは、製造業において、生産に使用する部品を管理するための図表のことです。一種類の製品に対して必要な部品の種類や数量を可視化するために、重要な役割を果たします。
部品表は生産プロセスのさまざまな場面で活用されており、生産スケジュールの作成や原料・資材管理、生産ラインなど、あらゆる部門にとって必要不可欠です。部門ごとに求められる情報は異なるため、部品表の様式は生産プロセスによって多種多様です。そのため、各部門が求める情報を網羅し最適化を図ることで、生産プロセス全体の生産効率化につなげられます。
マスカスタマイゼーションを導入する
マスカスタマイゼーションとは、大量生産(マスプロダクション)と個別設計・生産(カスタマイゼーション)を組み合わせた用語です。大量生産の長所である低コスト・短納期と、個別生産の長所である顧客ニーズに沿った生産の両方を取り入れた生産体系を指します。
近年顧客ニーズの多様化が進み、同一商品を大量に製造してコストを下げる大量生産では安価な海外製品に勝てなくなっています。そのため複数の製品での共通部分を作ることでコストや期間を短縮しながら、サイズやデザイン、搭載機能などをカスタマイズできるようにして付加価値を付け、競争力を獲得するのがねらいです。
国内外の自動車メーカーでは、フレームやサスペンションなどの基本部品は複数車種で共通のものを使用して開発期間を短縮し、金型などのコストを抑えています。一方、内外装は顧客が自由に選べるようにして、コストを抑えながら「自分だけの車」という付加価値を与えています。また、アパレルであれば、共通の型紙を使いながら生地やボタン、襟のかたちなどを好みで変えられるセミオーダースーツがマスカスタマイゼーションの例です。フルオーダーよりも圧倒的に安価で早く、顧客のサイズや好みに合わせたスーツを提供します。
マスカスタマイゼーションを実現するには、共通部品とカスタマイズ部品を分けて管理・製造する生産体制づくりや、厳密な部品管理を行うためのシステム導入が必要です。多くの場合は既存システムでは対応できず、新たにシステムを追加・入れ替えすることになるため、相応のコストと時間がかかります。さらに個別部品によるカスタマイズとコスト低減を両立するためには、製造工程の自動化・省人化による効率化を進めることが求められます。過剰在庫の発生を防止するための手立てとして、蓄積した顧客・販売データ分析に基づく高度な需要予測や顧客ニーズの把握も不可欠です。
生産体制を整えるだけでなく、顧客に対してのサービス提供・システム改善もマスカスタマイゼーションを実現するための重要なポイントです。非対面で顧客からの注文を受け付けるアプリやWebシステムの開発、クラウド上に顧客情報や注文履歴を蓄積して最適な提案を行うサービス、バーチャルで完成品を確認できるシステムなどを開発・提供することで、顧客満足度の向上と差別化を行います。それと同時に、データ収集やデジタル化による作業効率化にもつなげる仕組みです。
もともとマスカスタマイゼーションの考え方自体は1990年代からあるものですが、当時は思想を実現するための技術が追いつけずに広く普及するまでには至りませんでした。近年AIやIoT、ビッグデータや3DプリンタといったIT技術が進展したことに加えて、DXによる自動化・省人化が工場で進められていることも後押しし、マスカスタマイゼーションが拡大しています。
部品表の作成を自動化する「SPBOM」で
多品種少量生産の課題を改善!
生産プロセスの効率化を図るためには、部品表の作成を自動化する「SPBOM」の導入がおすすめです。
SPBOMは、BOMの課題を解決するための、エクサ独自開発のソリューションです。サイズや規格など、さまざまな特徴を持つ製品の「ルール」をあらかじめシステム上に登録しておき、製品名と仕様を指定すると、自動的にMBOM(製造部品表)を生成できます。
SPBOMを活用すれば、膨大なバリエーションを持つセミオーダー品を扱っている現場において、必要なMBOMを簡単に出力可能です。生産プロセスが付記されたBOMやBOPも作成できるため、現場で広く活用できます。
多品種少量生産は膨大な数のBOMを作成しなければならず、BOMのメンテナンスが追いつかなくなりがちですが、SPBOMならこのようなメンテナンス面の課題を解決に導きます。受注情報を参照した自動的なBOM生成にも対応しているので、手作業で都度BOMを登録する従来の作業に比べて、大幅に手間の削減につながります。
また、生産拠点ごとに異なる生産プロセスを持つBOMやBOPにも対応しているため、複数の拠点を有する企業にも最適です。
多品種少量生産における生産プロセスの効率化にお悩みの方は、ぜひSPBOMの導入をご検討ください。
多品種少量生産成功の具体例
近年働き手不足が社会的な問題となるなか、製造業においても労働力の確保が喫緊の課題となっています。さらにグローバル化の進展に伴い、製造業は今まで以上に激しい価格競争にさらされています。そのような状況下で、企業が多品種少量生産やマスカスタマイゼーションへの転換をし、成功するためには、製造方法を変えるだけでなく、プロセスの見える化や、自動化・省人化をいかに進めるかが非常に重要なポイントです。
ここでは、部品管理などの自動化や在庫の見える化といった改善を進めながら多品種少量生産を成功させた、2つの企業事例を紹介します。
BOM管理の自動化により効率化を進めた精密機器メーカー
精密測定機器や光学測定機器などの実験研究機器分野で高いシェアを持つある精密機器メーカーでは、生産管理の効率化やデータ収集による業務の見える化を目指して生産管理システムを導入。これは製造部門と営業部門で情報を共有することで、今まで問題となっていた購買・設計プロセスでの遅延を解決するのがねらいでした。実際、生産管理システムの導入により一定のデータ収集は実現には至っています。しかし、頻繁に発生する仕様変更による遅延などが影響してリアルタイムでの進捗管理が困難なことや、受注ごとに部品を設計し試作品を作成するため正確な原価が把握できないといった新たな課題が生まれました。
そこで同社が課題解決の手段として新たに導入したのが、BOM管理に特化した生産管理システムでした。これは従来設計部品表と製造部品表が個別に存在していた生産プロセスを、BOMを中心とした管理方法へと変更することで業務効率化を目指すものです。統合BOMを中核として発注から予算管理まで、生産管理に関連するすべての情報をデータベースで一元管理できるようにし、在庫や手配状況、原価などの情報が全社でリアルタイムに把握できるようにしました。これにより正確な原価把握やリアルタイムでの生産管理が実現し、課題であった情報共有不足による遅延が解消しました。さらにBOMの自動出力による省人化や入力ミスなどのヒューマンエラー削減にもつながったといいます。
在庫の見える化により多品種少量生産を成功させた建築資材メーカー
建築用の組み立て資材を製造するある大手メーカーでは、サイズの違いや部品の組み合わせが数千~数万種類にもなる製品を製造・販売しています。製品種類が膨大なため、長い間在庫をほとんど持たずに施工会社の注文に合わせて製品を製造・納品する方式を取っていました。しかし受注から出荷までの期間が約3か月と長く、受注生産のためコストも割高なことがネックとなり海外の安価な製品に負けてしまうケースが増え始め、このままでは市場でシェアを維持するのが難しくなるという危機感を経営層が持っていました。
そのため同社は課題解決のため社内プロジェクトを発足。従来型の受注生産を見直し、すべての在庫を少量ずつ持つ方式へとシフトしました。今まで売れ筋製品のみ大量の在庫を保有し、販売数が多くない製品は在庫を持っていなかったのが、販売履歴を分析することで適正在庫を確保。これにより過剰在庫の削減が実現しただけでなく、即納可能な製品を増やしたことで売り上げ全体も増加しました。さらに商品が販売される都度次の製品を製造して補充するようにしたことで、すべての製品で納期を大幅に低減できました。
まとめ
多品種少量生産は、多様化する顧客ニーズへの対応や、過剰在庫のリスク軽減などのメリットがあります。その一方で、生産効率化に関する課題も数多くあります。現場の生産プロセスを効率化するためには、受注分析や生産方法の最適化、在庫の確保など、さまざまな工夫が必要不可欠です。
生産プロセスの効率化には、BOM管理の自動化やBOM間の連携による情報の一元管理・可視化も高い効果を発揮します。適切なソリューションを導入し、生産管理の適正化や業務効率化をめざしましょう。
生産プロセスの効率化に向けた取り組み例
生産プロセスを改善する様々な手法を5つご紹介いたします。
・ABC分析を活用したプロセス改善
・4Mを活用したプロセス改善
・IoTを活用したプロセス改善
・RPAを用したプロセス改善
・BOM管理システムを活用したプロセス改善
ブログに関するお問い合わせ
関連する記事
関連ソリューション
関連事例
お問い合わせ
CONTACT
Webからのお問い合わせ
エクサの最新情報と
セミナー案内を
お届けします
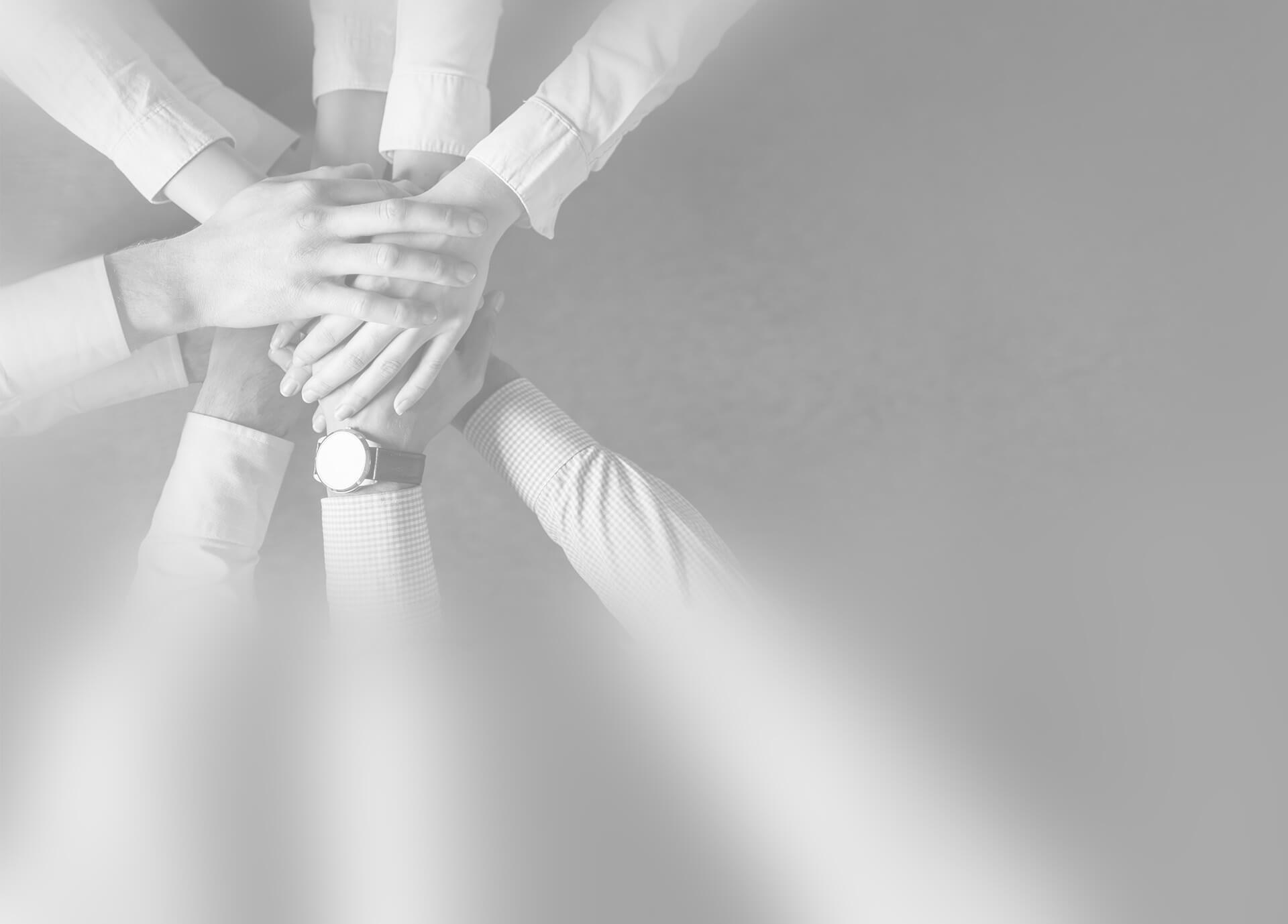