エンジニアリングチェーン(EC)とサプライチェーン(SC)
製造業のバリューチェーンには、大きく「エンジニアリングチェーン(EC)」と「サプライチェーン(SC)」という2種類の工程の流れがあり、この2つの流れを適切に管理することが、製品および企業の価値を大きく左右します。
本章では、エンジニアリングチェーンとサプライチェーンの概要や、その重要性や強化すべき理由、両者の連携の必要性などについて、経済産業省が公表している「2020年版ものづくり白書」の内容を中心に解説します。
エンジニアリングチェーンとは?
エンジニアリングチェーンとは、研究開発から製品設計、工程設計、生産など、設計部門を中心とした一連の工程の流れのことです。
製品に関する情報やデータを、各プロセスにおいて関係する部門が適切に把握・共有し、連携をとりながら効果的に活用することが重要であり、その際には、ITをいかに活用するかが問われます。
エンジニアリングチェーンを管理することをエンジニアリングチェーンマネジメントと呼びます。エンジニアリングチェーンマネジメントは、工程全体の最適化と製品設計力・開発力の強化を目的に行われ、適切に実施することで、製品やサービスの開発コストを削減したり、サプライヤーとの間で正確かつ柔軟な情報共有を実現したり、市場ニーズに迅速に対応したりすることが可能となります。
製品やサービスの品質や性能を向上させるための改善点を見つけ出したり、顧客のフィードバックを反映させたりすることも可能です。
エンジニアリングチェーンの重要性が高まっている背景
エンジニアリングチェーンの重要性が高まっている背景としては、「デジタル技術の進展」や「製品の複雑化」、「不確実性の高まり」といったものが挙げられます。
デジタル技術の進展
近年、IoTやAIなど先端技術の活用による産業構造の大転換を意味する「第4次産業革命」が提唱されています。これに伴い、製造業においても先端技術を活用した生産の自動化やネットワーク化が進んでおり、大きな転換期を迎えています。
この第4次産業革命において、特に重要なものがDXです。エンジニアリングチェーンにDXを導入し、開発や設計、製造プロセス等のデジタル化を推進する必要性がかつてないほど高まっています。
製品の複雑化
近年、グルーバル化の進展や顧客が製品機能に求める機能の高度化・多様化、さらに気候変動に対応するための、環境面・資源(エネルギー)面の制約の先鋭化といった傾向が高まっています。特に、2015 年9月の国連サミットにおいて「持続可能な開発目標(SDGs)」が採択されたことで、企業が果たすべき社会的役割に注目が集まり、我が国の製造業に携わる事業者も対応が求められています。製品に対する機能要求が高まる一方で、制約条件が厳しくなるのであれば、製品の複雑化が進んでいくことは避けられません。
また、製品に占める制御ソフトウェアの比率が高まっていることも、製品の複雑化を招いています。この傾向は自動車において特に顕著です。自動車ソフトウェアのコード数は、2000年時点では100万行程度でしたが、現在では1億行を超えています。
このように製品が複雑化していけばいくほど、エンジニアリングチェーンにかかる負荷はより大きなものとなります。こうしたことから、より高い精度や柔軟性を持つエンジニアリングチェーンを構築する必要性が高まっているのです。
不確実性の高まり
近年はしばしば「VUCA」(ブーカ)の時代と言われており、「Volatile(変動性)」、「Uncertain(不確実性)」、「Complex(複雑性)」、「Ambiguous(曖昧性)」が非常に高まっています。実際に、気候変動による自然災害の大型化・頻発化や、地政学的リスクの高まり、世界各国における政治的対立・分断の先鋭化、インフレの進行など、政治・経済・社会のあらゆる面で不確実性が高まっています。
日本の製造業が競争力を維持・向上するためには、この不確実性に対応しなければなりません。すなわち、想定外の突発的な環境や状況の変化が発生した場合、製品の仕様を早急に変更しなければならないリスクにさらされているということです。このような事態に対しては、仕様変更の自由度が高い設計段階において、可能な限り迅速に対応することが重要となります。さらに、仕様変更に対応する「製品設計」のみならず、仕様を変更した製品を効率的に製造できるよう、製造工程を迅速かつ自在に変更するための「工程設計」の能力も必要です。
このように、不確実性に対応するには、製品設計と工程設計の双方を含むエンジニアリングに高い能力が求められ、エンジニアリングチェーンの強化が必須となります。
サプライチェーンとは?
サプライチェーンとは、受発注から生産管理、生産、流通・販売、アフターサービスなど、生産から消費者に至るまでの一連の工程の流れのことです。
製品の原材料の調達から製造、在庫管理、配送、流通、販売などの各プロセスを一元的に管理して最適化することをサプライチェーンマネジメントと呼び、製品供給を効率化・安定化させる手法として近年注目されています。
サプライチェーンマネジメントを適切に実行することで、各工程における製品の流れに関する情報を収集・分析でき、それに基づいた正確な需要予測により在庫の過不足を防ぐことができます。また、正確な需要分析に加え、仕入れや出荷に関する情報を一元管理することで物流プラセス全体の無駄を省き、リードタイムの短縮にもつながります。過剰在庫を解消すれば無駄な保管コストやそれに伴う人件費の削減も期待できるなど、サプライチェーンマネジメントには多くのメリットがあります。
サプライチェーンを強化すべき理由
新型コロナウイルスの感染拡大を契機に、グローバルなサプライチェーンを強化する必要性が改めて認識されました。それに加えて、サプライチェーンを強化すべき理由としては、「市場のグローバル化」や「労働人口の減少」といったものが挙げられます。
市場のグローバル化
市場のグローバル化により、製造業のサプライチェーンは複雑性しており、競争が激化しています。企業は世界中の市場から原材料や部品を調達し、製品を世界中の顧客に提供する必要があります。このような状況下で、サプライチェーンは必然的に非常に広範囲に形成され、多くの国や地域との間で各工程を密接に結びつける必要があります。
こうしたことから、サプライヤーとの連携の促進や物流網の効率化など、サプライチェーンの強化が不可欠となっているのです。
労働人口(生産年齢人口)の減少
少子高齢化が進む日本では、労働人口(生産年齢人口)の減少が深刻な課題となっています。日本の生産年齢人口(15~64歳)は1995年の8,716万人をピークに減少しており、2021年には7,450万人となっています。2050年には2021年から29.2%減の5,275万人に減少すると見込まれており※、今後、企業がさらなる人手不足に直面することはほぼ間違いない状況です。
そのため、サプライチェーンの各工程において効率的な生産プロセスや自動化技術の導入を進め、より少ない労働力でサプライチェーンを維持できるような工夫が企業には求められます。例えば、サプライチェーンを強化する過程で自動化やロボット技術を活用することで、生産ラインの柔軟性を高め、労働力の不足を補うことができます。
※出典:総務省「令和4年版情報通信白書」
https://www.soumu.go.jp/johotsusintokei/whitepaper/ja/r04/html/nd121110.html
エンジニアリングチェーンとサプライチェーンは、両方とも製品の生産や提供におけるプロセスを管理する概念です。しかし、エンジニアリングチェーンは製品の設計や開発、製造に関する部署間の縦のつながりである一方、サプライチェーンは受発注や生産等を通じて、顧客のもとに製品が届くまでの製品の流れ(横のつながり)であるという違いがあります。
言い換えれば、エンジニアリングチェーンは製品の設計や開発、製造段階までの「情報」の流れに焦点を当てるものであり、サプライチェーンは製品の供給に関わる全体的な「モノ」の流れを指すということです。
エンジニアリングチェーンとサプライチェーン連携の重要性
製造業において、製品や生産技術に関する情報は、エンジニアリングチェーンとサプライチェーンの2つの流れを通って結びつくことで付加価値を生み出します。この付加価値を最大化するためには、エンジニアリングチェーンとサプライチェーンをシームレスにつなぐことが不可欠です。これにより「生産の最適化」や「マスカスタマイゼーション」(大量生産と個別受注生産を組み合わせた生産方式)はもちろん、「サービタイゼーション」(製造業のサービス産業化)や「ことづくり」といった新たなビジネスの構築も容易となります。
出典:経済産業省「2020年版ものづくり白書」
エンジニアリングチェーンとサプライチェーンにおける課題
前章でみてきたように、エンジニアリングチェーンとサプライチェーンの強化、および両者の連携は今日の製造業にとって非常に重要です。そこで不可欠となるのがデータ活用をはじめとするデジタル技術の導入ですが、現状では課題も少なくありません。
本章では、エンジニアリングチェーンとサプライチェーンにおける課題を解説します。
エンジニアリングチェーンにおける課題
「2020年版ものづくり白書」内の調査によると、エンジニアリングチェーンにおいては、データ活用の遅れや製品設計および工程設計に関する課題がみられます。
データ活用の遅れ
国内製造業に対して、生産プロセスに関する設備の稼働状況等のデータ収集を行っているかを尋ねたところ、データ収集を行っている企業の割合は、51.0%でした。これは2018年12月調査時の58.0%よりも7%低い数字です。
また、複数部門間での情報・データ共有について、販売後の製品の動向や顧客の声を設計開発や生産改善に活用しているかどうかを確認したところ、「実施している」と回答した企業は8.4%であり、前回調査時(2017年度)の15.8%から大きく減少しました。
その他、センサーや IT を活用して個別工程、製造工程全般、人員のそれぞれの稼働状況の「見える化」によるプロセス改善等に取り組んでいる企業の割合もそれぞれ1割~2割程度と低く、このようなことから、日本の製造業におけるデータ収集・活用の取り組みには遅れがみられることがわかります。
製品設計および工程設計の課題
2019年12月に国内製造業に対して実施されたアンケートによれば、エンジニアリングチェーンの上流に当たる製品設計力のここ5年間での変化の状況について、約4割が向上していると答えたものの、半数以上が「あまり変化は無い」と回答しています。製品設計のリードタイムに関しても同様で、約4割が短くなっていると回答した一方で、半数以上が「あまり変わらない」と回答しています。
製品設計のリードタイム短縮を図るための取組として重視しているものを確認すると、半数以上が「生産技術、製造、調達といった他部門との連携促進」と回答しており、設計力の強化に向けては他部門との連携が重視されている状況です。
また、国内製造業に対して工程設計(生産技術)力のここ5年間での変化について尋ねたところ、36.9%が「向上している」、58.8% が「あまり変化はない」、4.3%が「低下している」と回答しています。
工程設計力が「向上している」と回答した企業に対してその要因を確認したところ、「生産技術、製造、調達といった他部門との連携強化」と回答した企業が最も多く 79.2%を占め、「営業、アフターサービスなどから顧客ニーズのフィードバックを強化(26.5%)」「デジタル人材の育成、確保(22.5%)」が続いています。
一方、工程設計力が「低下している」と回答した企業についても同様にその要因を確認すると、「ベテラン技術者の減少(79.4%)」、「製造現場との連携不足(30.9%)」、「属人的な設計プロセス(25.0%)」、「間接部門の人員削減(19.1%)」が上位に挙がっています。この結果から、工程設計力の維持が熟練者の技に頼りがちで、その技術を後継に引き継ぐことが課題となっている様子がうかがえます。
このほかにも、生産拠点の工程や設備などを意識した基準情報(BOM/BOP)がタイムリーに作成できていない課題や、膨大な数の基準情報(BOM/BOP)作成が必要となり、登録やメンテナンスが限界になっているなど、基準情報に関する課題もあります。
サプライチェーンにおける課題
サプライチェーンにおける課題としては、主に以下の4つが挙げられます。
業務連携が乏しく、個別最適で全体的視点での意思決定ができていない
サプライチェーン内の異なる部門やサプライヤー等との連携が不十分であり、各部門が個別に最適化された業務を行っていることがあります。
しかし、こうした個別最適化は全体的な視点に欠けるために、サプライチェーン全体の効率や柔軟性を損なう可能性があります。例えば、生産部門が生産能力を最大限に引き出そうとしている一方で、調達部門が在庫を抑えるために発注量を減らしている場合などが考えられます。
経営視点(金額)、業務視点(数量)を含む判断基準が明確でない
サプライチェーンにおける判断基準が明確でない場合、経営層と業務担当者の間で意思疎通が困難になります。例えば、経営層がコスト最適化を重視する一方で、現場の担当者が在庫の最大化を図ろうとする場合、目標を一致させることが難しくなります。
環境変化・予実乖離を探知する能力が不足し、利用情報鮮度が低く変化への対応スピードと柔軟性に乏しい
サプライチェーンにおける情報収集や分析の体制が整っていない場合、市場や需要の変化、またサプライヤー側の問題などに素早く対応することが難しくなります。リアルタイムでの情報共有や予測能力の向上が必要です。
熟練者任せ(勘・経験・度胸)の業務となっており、各種計画、回答精度が低い
過去の経験や個人の勘に頼った業務や意思決定が行われている場合、効率的なサプライチェーンマネジメントが難しくなります。データや分析に基づいたマネジメントや意思決定プロセスの導入が必要です。
エンジニアリングチェーンとサプライチェーンの連携における課題
エンジニアリングチェーンとサプライチェーンを効果的に連携させるためには、各工程に携わる部門間の連携が不可欠です。例えば、製品設計や工程設計、製造等の部門間の連携が取れていないと、品質不良が発生したり、設計変更が製造部門に伝わらなかったり、正確なコスト予測ができなかったりするリスクが発生します。
こうした問題は、製品の複雑化や不確実性の高まりによっていっそう深刻化し、製造業の競争力を損なう原因となりかねません。
また、以下のような課題もあります。
サプライチェーンに最新の基準情報(BOM/BOP)が反映できず、欠品や過剰在庫、納期遅延の要因となっている
製造現場における実際の生産状況や需要変動などがサプライチェーンに適切にフィードバックされず、最新の基準情報が反映されないことがあります。これにより、不足や過剰な在庫、または納期遅延といった問題が生じる可能性があります。
拠点や目的別に基準情報(BOM/BOP)を作成するのに手間がかかり、整合性が保てない
製品や部品の設計変更や改良が頻繁に行われる場合、それに応じて基準情報(BOM/BOP)を更新する必要があります。
しかし、この作業に手間がかかり、さらに異なる拠点や目的別に異なる基準情報を作成する場合、整合性が保てなくなります。これにより、生産ラインやサプライチェーンに混乱が生じ、効率が低下します。
企業・事業統廃合、新ビジネスモデルに対応できない
企業の統合や事業の統廃合が行われた場合、それに伴うサプライチェーンやエンジニアリングチェーンの変化に迅速かつ柔軟に対応する必要があります。また、新しいビジネスモデルの導入や市場の変化にも迅速に対応する必要があります。
しかし、これらに対応するための体制やプロセスが整備されていない場合、調整や変更に時間がかかり、競争力が低下する可能性があります。
エンジニアリングチェーンとサプライチェーンの連携に向けて
前述のように、世界的に不確実性が高まっている中で製造業が競争力の維持・向上を図るためには、製品設計と工程設計の双方を含むエンジニアリングに高い能力が求められ、エンジニアリングチェーンの強化が不可欠です。
エンジニアリングチェーンを強化するためには、設計、製造、調達といった部門間の連携を高める必要があります。しかし、実際には企業内部において、設計部門と製造部門の間のコミュニケーションが十分に行われていない場合があります。また、設計部門と製造部門が、それぞれ異なるIT ベンダーから異なる IT システムを導入しているため、両部門のシステム連携が必ずしもうまくいっていないケースもあります。
エンジニアリングチェーンとサプライチェーンの連携に必要なこと
エンジニアリングチェーンとサプライチェーンを連携させるために必要な第一歩は、設計部門が設計を行う上で使用する設計部品表(E-BOM)、製造部門が製造を行う上で使用する製造部品表(M-BOM)、そして工程設計情報をまとめたものである工程表(BOP)を結びつけて、各部門がこれらを共有することです。これにより、設計部門から製造部門、あるいは製造部門から設計部門への双方向の円滑なデータ連携が可能となります。
部品表(BOM)や工程表(BOP)の整備と統合は、部門を超えたデータ連携を容易にし、柔軟性の高い組織を実現します。さらに、このようなデータの連携と双方的なコミュニケーションは、設計部門と製造部門のみならず、企業全体、さらにはサプライヤーや顧客などの間でも実現されることで、さらに大きな効果を生み出します。
部品表(BOM)や工程表(BOP)の整備・統合はサプライチェーンの柔軟性を高める
部品表(BOM)や工程表(BOP)の整備・統合は、サプライチェーンの柔軟性等を高める上でも、極めて重要です。
例えば、何かしらの不測の事態が勃発し、ある国の生産拠点が停止せざるを得なくなった場合、別の工場で生産を迅速に代替できれば、供給途絶は回避できます。しかし、設計部品表や製造部品表、工程表が統一的に整備・共有されていない場合は、代替生産を開始する際に部品表から調整しなければならないため、膨大な人的・時間的リソースが必要になります。これでは、柔軟かつ迅速な代替生産を行うことは不可能です。つまり、サプライチェーンの柔軟性等を高め、ダイナミック・ケイパビリティ(環境変化に柔軟に対応し、組織を変革する能力)を強化するためには、部品表や工程表を整備し、エンジニアリングチェーンとサプライチェーンを連携させておかなければならないということです。強靭なグローバル・サプライチェーンを構築するためにも、部品表や工程表を整備し、エンジニアリングチェーンを強化することが不可欠となります。
なお、エンジニアリングチェーンとサプライチェーンの連携には社内の多くの部門が関わるため、部門を越えた横断的な取り組みが求められます。そのため、経営陣を巻き込み、必要な予算を確保し会社としてのビジョンを提示した上で全社的に取り組む必要があります。
マスター統合の課題
前述の部品表や工程表は基準情報(マスターデータ)ともいいます。マスターデータは、企業や組織内で共有される業務上必要な基礎データであり、顧客情報、製品情報、サプライヤー情報なども含まれます。
また、統合すべきマスターデータを選択して一元化することを「マスター統合」と呼びます。マスターデータが統合されていない状態では、各部門が保有しているデータベースやシステムで個別に管理されているため、データの重複や矛盾などが発生しやすくなりますが、マスター統合を行うことで、データの重複や矛盾が排除され、各部門がマスターデータの情報を共有できるようになります。
マスター統合は製造業の競争力向上にとって重要な役割を果たしますが、実際に行う際には課題もあります。
データの一貫性の確保
異なるシステムや部門で扱ってきたデータを統合する際には、データの一貫性を確保することが難しい場合があります。多様な種類のデータを同じ場所に集約するため、データの種別に応じて取り扱いを変える必要があり、その際に多くの工数がかかることも課題です。
構造化データと非構造化データが混在することもあり、それぞれのデータすべてに対応できるだけの柔軟性を持たせる必要があります。
ガバナンスとセキュリティに関する課題
マスター統合を進める際には、これまで個別に管理していたデータを一元的に集約するため、データを管理する責任の所在が曖昧になりがちです。
各部門が独自のルールでデータを管理・活用していた場合には、ガバナンスの統制が弱くなり、思わぬ情報漏洩リスクにさらされることが考えられます。例えば、他部門のデータに対するアクセス権限のルールが徹底されておらず、社外への不用意な持ち出しや不正アクセスにつながるなどのリスクが考えられます。
人的リソースの課題
マスター統合に関する知識やスキルを持つ専門人材の不足という課題もあります。各部門の業務システムのサイロ化が進んでいると、データの抽出や整理の難易度が高く、より高度な知見を持つ人材が必要となります。
人的リソース不足に対応するためには、人材の育成・確保に関する計画を立て、着実に進めることが重要です。人材の育成はもちろん、即戦力の採用やアウトソーシングも選択肢に入ります。
マスター統合のためのステップ
マスター統合の目的の決定
まずは、なぜマスター統合を進めるのか、その目的を決めます。業務効率化やデータを活用した売上の拡大、的確なデータ分析による迅速な経営判断など、目的は企業や置かれた状況によって異なります。
組織全体にマスター統合により得られるメリットを伝え、目的について部門間で合意を得た上で開発者へ伝えることが重要です。
集約すべきデータの整理と抽出
目的の実現に必要なデータを整理・抽出するため、統合するデータを特定します。
ただし、データ収集を優先するとデータの中身が整理されず、重複や矛盾したデータを見過ごしてしまうことがあります。不要なデータは統合した際に混乱を招きかねないので、重複したデータや不正確なデータを特定し、必要に応じて整理する必要があります。データの粒度やフォーマットなども揃えておくと良いでしょう。
データ統合管理基盤の設計・構築
各業務システムやデータを集約する場所(データレイクなど)、クレンジングツール等を選定します。それぞれが持つ特性や仕様を考慮して、設計・構築を進めていく必要があります。
データの移行と運用
基板設計と構築が完了した後は、データ移行計画の策定に入り、データ移行後は実際の運用に入ります。
運用プロセスでデータの登録や更新方法が異なると、表記ゆれなどを起こし、複数のデータが作成されるなどの不具合が発生する可能性があるため、各部署や業務におけるデータの登録や更新等の手順を統一する必要があります。マスターデータを使うためのガバナンスポリシーなども策定しておくと良いでしょう。
運用開始後は、データ統合プロセスが適切に行われているかチェックし、必要に応じて定期的に見直しを図ることが大切です。
まとめ
国内の製造業がさまざまな国際環境の変化に対応しながら競争力を維持・向上させるためには、エンジニアリングチェーンの強化とサプライチェーンとの連携が不可欠です。
また、製品の複雑化が進んでいることから、エンジニアリングチェーンそのものを強化する必要性も高まっています。
エンジニアリングチェーンとサプライチェーンとの連携で求められるのが、部品表(BOM)や工程表(BOP)の整備と統合、すなわちマスター統合であり、これを通じてサプライチェーンの柔軟性が高まり、ダイナミック・ケイパビリティを持つ組織の実現に寄与します。
エンジニアリングチェーンとサプライチェーンの連携を実現する基準情報(マスターデータ)のあり方については、下記のホワイトペーパーでも解説していますのであわせてご覧ください。
お役立ち
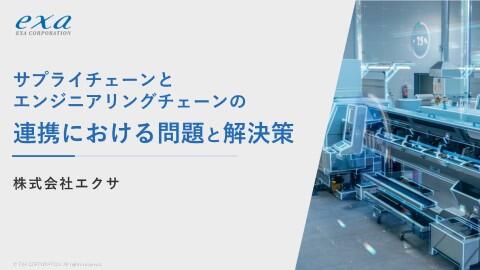
サプライチェーンと エンジニアリングチェーンの 連携における問題と解決策
製造業におけるバリューチェーンには「サプライチェーン」と「エンジニアリングチェーン」があります。製品や生産技術に関するデータは、この2つのチェーンを通って流れ、結びつき、そして付加価値を生み出します。この2つのチェーンの連携を強化し、様々なビジネス環境変化への迅速な対応は喫緊の課題となっています。
本資料では、サプライチェーンとエンジニアリングチェーンの連携における問題解決に向けた取り組みをご紹介します。
関連する記事
関連ソリューション
関連事例
お問い合わせ
CONTACT
Webからのお問い合わせ
エクサの最新情報と
セミナー案内を
お届けします
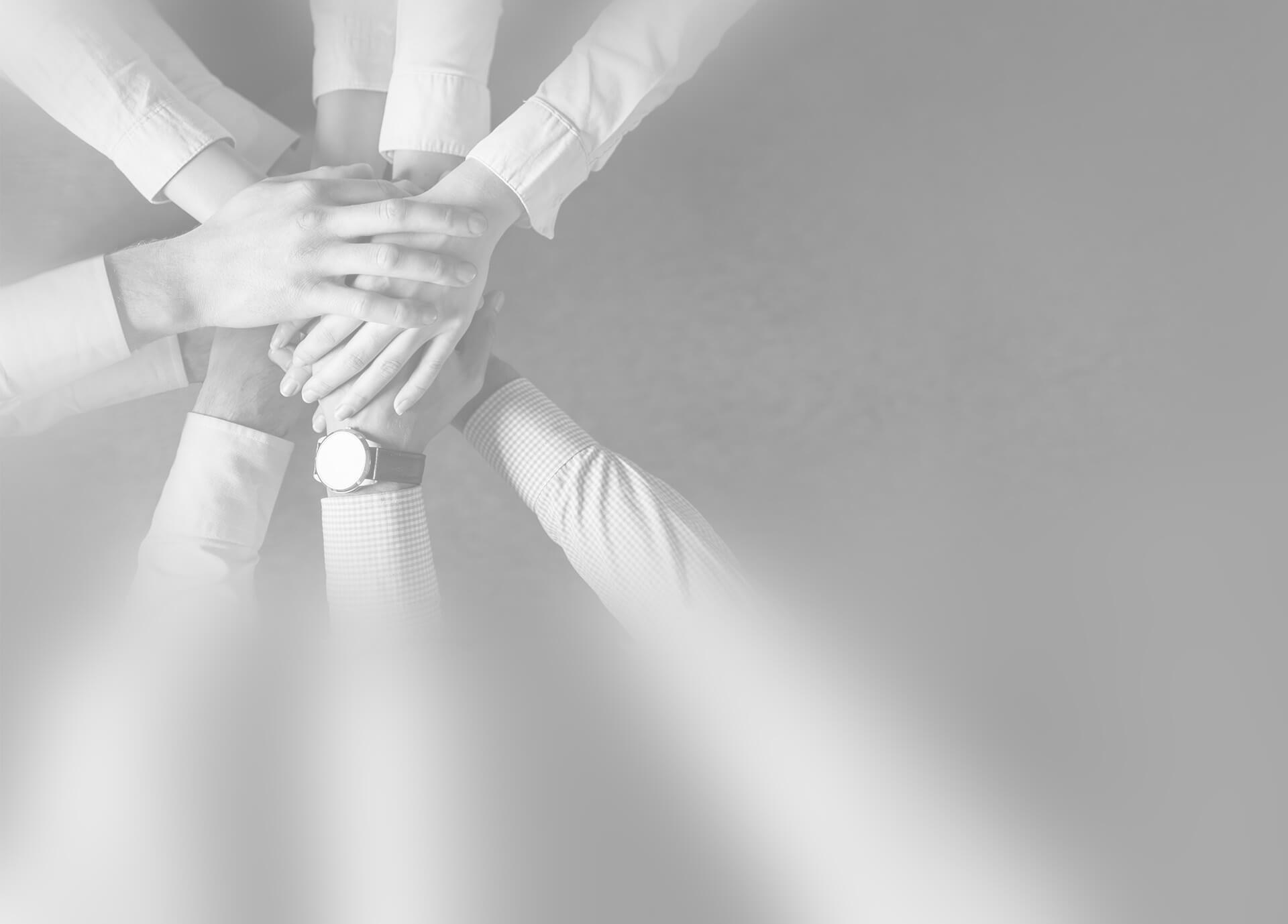