生産管理には受注管理や生産計画などの複数の業務があり、各業務を適切に行うことでコスト削減や利益向上などにつながります。しかし、多品種少量生産による工程の煩雑化などの影響で、各業務を効率良く進めることが難しいのが現状です。
生産管理の改善には、各業務をシステム化し、作業の効率化を図ることが重要です。
複雑化する生産管理業務を、どう効率化すればよいか詳しく知りたい方は、ダウンロード資料をご活用ください。
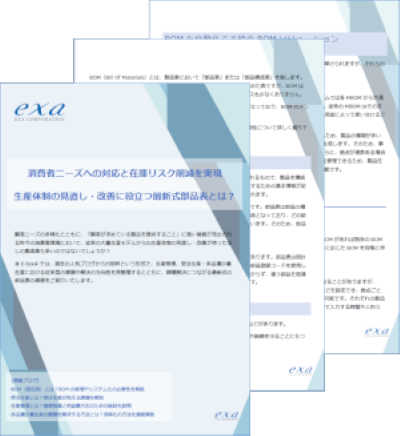
生産プロセスの効率化に向けた取り組み例
受注生産・多品種少量における課題整理と、 部品表を活用した改善策を解説しています。
生産管理とは
生産管理とは、生産計画に沿って製品を製造する上で、品質(Quality)、納期(Delivery)、コスト(Cost)すべてを適切に管理することです。QDCを最適化し、製品の計画から出荷までの全工程を効率的に進めることが求められます。
生産管理が正しく行われていれば、トラブルが発生しにくく現場の製造活動がスムーズに進みます。しかし、多くの企業では生産工程や業務プロセスが複雑化しており、生産管理が困難な状況です。そして生産管理が不充分だと、製品の品質低下や納期遅れにつながるため、できるだけ早急に改善しなければなりません。
生産管理の目的
生産管理の目的として、生産業務の効率化が挙げられます。生産管理部門がすべての生産プロセスを把握し、適切に管理することで、現場が効率的に業務を遂行できる環境の整備が可能です。適切な生産管理で業務効率化が実現すれば、これまでよりも少ないリソースで大きな成果を得られるようになり、生産性も高まります。
生産管理は現場をコントロールし、効率的かつスムーズな生産業務を実現する司令塔のような存在です。適切な生産管理によって現場の従業員は効率的に作業へ取り組め、その結果、組織の利益最大化につながります。
▼ 生産体制の見直しつながる解決策をご紹介(全49ページ)
『消費者ニーズへの対応と在庫リスク削減を実現 生産体制の見直し・改善に役立つ最新式部品表とは?』はこちらからダウンロードできます。
生産管理と工程管理や製造管理との違い
工程管理と製造管理に大きな違いはありません。イメージとしては、生産管理という大きな枠組みの中に工程管理、製造管理が含まれています。生産管理は、原材料の受発注から成果物の納品まで生産に関する全プロセスを管理するのに対し、工程管理や製造管理は工程の進捗や状況、品質など限られた領域を管理します。
工程管理をもう少し掘り下げましょう。工程管理は、円滑な製造業務を実現するために行う管理業務です。独立したそれぞれの工程がうまく連携しつつスムーズに作業を進められるよう、適材適所な人材配置を行うほか、設備状況のチェックも担います。次章からは、工程管理を含めたより詳しい業務内容を解説します。
生産管理の業務内容
受注管理(需要予測)
受注管理(需要予測)とは、受注履歴、競合の動き、経済状況、気温や天気といったあらゆる面を考慮し、製品の需要量を予測することです。予測と実際の需要量に大きな差が出ると、在庫が大量に発生する・製品が不足して機会損失を招くといった問題が発生するため、精密な需要予測が求められます。
また、顧客からの受注内容から正しく製品仕様を把握することも一種の受注管理です。この場合は製造する数量や納期などを正しく算出するために製品情報を整理したあと、各部門で共有し、生産スケジュールや納期を割り出し、実際の製造作業へ移ります。
さらに、これから受注・生産する製品のほかに、出荷待ちとなっている受注残の管理も行います。
生産計画
生産計画とは、需要予測や受注情報を基に製品の製造計画を立てることです。材料の調達や必要な人員、製造ラインスピードなどさまざまな面を考慮し、製造開始日、製品仕様、製造量、納期などを割り出します。
生産計画においては、需要予測で算出した需要量や製品仕様といった情報の洗い出しだけでなく、仕掛状況を踏まえたスケジュール作成も重要です。当然ですがスケジュール通り製品を出荷できるよう、現場の状況も考慮しながら日程を調整しなければなりません。
なお、生産計画は需要予測や仕掛状況を踏まえた上で、リアルタイムの情報も加味します。最も良いタイミングで出荷できるよう、市場調査や顧客へのヒアリングも必要です。
調達・購買計画
調達・購買計画は、生産計画を基に使用する材料量や材料の入手時期を計画することです。必要な時期に必要な材料を入手すれば、生産ラインを止めることなく円滑に作業を進められます。
この調達・購買計画には、材料の発注先・購入日・数量・費用などを管理する業務も含まれているため、いつ・何を・いくつ・どの業者に発注するかを明確にすることも非常に重要です。
材料の調達スケジュールと生産計画を照らし合わせ、次の工程に影響が出そうな場合は調達スケジュールを変更するなど、柔軟な対応が求められます。
もし材料調達に関する正確な情報管理ができていなければ、材料が不足して生産がストップする、過剰に在庫を抱えて予算超過となるといった問題が発生します。生産計画に沿って過不足なく調達しつつ、仕入れ先を選定してコストを抑えることが必要です。
工程管理(製造管理)
工程管理(製造管理)とは、生産計画を円滑に進めるため、各加工工程のスケジュール設定や進捗管理などを行うことです。必要に応じて工場のライン制御や飛び込み注文への対応を柔軟に行いつつ、納期は厳守することが求められます。
また、工程管理には各工程のスケジュール作成も含まれており、各工程での手順を示し、加工に必要な時間や生産ラインのスピードなどを加味してスケジュールを立てます。生産能力を超える負荷がかかると進捗に遅れが生じかねないため、リアルタイムで生産ラインの負荷状況を確認する場合も少なくありません。
もしひとつの工程で遅れが生じた場合、以降の工程スケジュールにも影響が出るため、各工程の期日の設定は綿密に行う必要があります。スケジュールを再設定する手間が生じて、最悪の場合、納期に間に合わなくなるおそれもあるためです。
品質管理
品質管理には、製品の品質が保たれているかどうかの検査や、不良品の調査・品質の改善作業などがあります。製品の品質は顧客からの信頼度に直接かかわるため、非常に重要なポイントです。
品質の検査方法には、各工程で正しい手順により作られているかどうかの検査や、製品をランダムに選んで行う検査などがあり、検査時に不良品が出た場合は原因を特定するための調査をします。
また、顧客からのクレーム対応も品質管理に含まれます。クレーム内容は各部門で共有し、製品の改良に活かすことが大切です。内容によっては、加工手順の改善にもつながります。
在庫管理
在庫管理とは、製品の在庫状況を把握し、必要に応じて生産計画を調節することです。在庫量を最適に保つために製造スケジュールを修正したり、需要量と生産量に差が出ないよう各工程を管理したりします。
材料や中間品、部品等の仕入れ時期を時系列で管理しなければならないため、いつ・どこで・何を・いくつ・いくらで調達したのかといった情報を整理して、在庫量を柔軟に調整する必要があります。
なお、当初予定していたよりも大幅にスケジュールが遅れる・需要量よりも製造量が多い(または少ない)といった問題が発生すると、在庫量の最適化に影響が出るため、各工程の進捗や需要と供給のバランスを随時チェックしておかなくてはなりません。
原価管理
原価管理とは、材料や加工に必要な費用を分析し、利益を最適化するために各費用を比較・調整することです。製品設計時に設定した見積もりと実際にかかった費用を比較し、原価が適正であるかどうかを分析します。
また、各工程の作業を分析し、無駄な手順や統合できる作業はないか確認する、手順の改善活動も原価管理に含まれます。そして、市場調査によって複数の材料の原価を比較すれば、より安い原価で材料を仕入れできるため、コストパフォーマンスの改善も可能です。
そのほか、製品ごとに原価管理を行えば、次回の製品開発時に適切な材料費や加工費を見積もれます。原価管理とあわせて過去の実績や社会の経済状況なども加味し、予算とコストの比較・分析を行うことも大切です。
生産管理における課題
生産管理を最適化するには、生産管理における課題を解決する必要があります。しかし、各企業が抱える課題は多く、原因を追究するための時間やコストを確保できない状況に陥っているところもあります。生産管理における課題として、代表的なものを確認しておきましょう。
適切な生産準備が行えていない
生産準備とは、製造ラインを立ち上げて製造を開始する前に、製品仕様の検討・工程計画・設備計画などを行うことです。製品を納期までに完成させるために、必要に応じて製造ラインの変更や、各種工程のスケジュール計画をします。
生産準備に不備があった場合、実際の製造過程でトラブルが発生したり、スケジュールが遅れたりするおそれがあります。そのため生産準備は、各部門間で正しく情報を共有し、間違いや認識違いがないように進めることが大切です。
しかし、実際は現場の業務が優先され、生産準備に十分な時間がかけられていません。また、複数の部門や拠点間での意思疎通ができず、生産準備が不充分なケースもしばしば見られます。
生産管理と生産準備の違い
生産管理と生産準備の名称は似ていますが、意味は大きく異なります。生産準備とは、生産管理の業務の一部に含まれる、本格的に製品を製造する前の準備段階です。
具体的な内容としては、試作品の作成、材料の調達先の選定、原価の計算などがあり、生産準備を適切に行うには、あらゆる業務を遂行できるマルチスキルが求められます。また、各工程で出た課題や問題点をすぐに改善し、製品の出荷までに完成品として仕上げなければいけないため、問題解決スキルも求められます。
生産準備の不備は、納期遅延や製品の品質悪化につながりかねません。生産準備では全工程の最適化が重要な課題です。
生産の標準化が困難
標準化とは、作業のレベルや品質の高さが誰でも・どこでも一定に保たれている状態を指します。生産の標準化とは、各拠点や部門で生産スピードや品質のレベルが同一であるということです。しかし実際は、各拠点で生産量に差が出たり、品質に違いが出たりすることがあります。
生産の標準化を妨げている原因として、工程の複雑化や多品種少量生産の増加が挙げられます。最大の問題は、工程の複雑化によって業務内容を拠点間で共有することが難しくなり、生産負荷を可視化できない点です。
生産の標準化を実現するためには、まず各拠点で生産負荷を可視化し、問題点を明らかにすることが重要です。しかし、現状では原因の追究よりも現場作業が優先されており、改善活動に十分な時間をかけられているケースは多くありません。
不良率が改善できない
不良率とは欠陥品が発生する割合のことで、利益を上げるためには不良率を下げることが重要です。しかし、元から不良率が高く、不良率が上がる原因も特定できない場合も多いです。
不良率を上げている原因がわからない以上、改善は困難でしょう。そして不良率が高い状態のまま製造し続ければ利益率が上がらず、売り上げにも悪影響を与えます。
原因の特定が難しい理由は、部品の数が膨大であることや、工程の複雑化などです。膨大な部品の中から不備があるものを見つけるには、多くの時間とコストを要し、工程の複雑化は、そもそも各工程の不良率自体を把握できていないという問題を引き起こします。
ヒューマンエラー(手配漏れ・誤発注)が発生する
近年の製造過程ではさまざまな工程が機械化・デジタル化されていますが、全く人の手を使わないことは不可能です。データを手作業で入力したり、部品を加工したり、目視でチェックしたりなど、人の手を必要とする作業は必ず発生します。
人の手が入ると、ヒューマンエラーが発生します。どれほど注意していても、人が作業する限りヒューマンエラーを完全に無くすことは難しいでしょう。ヒューマンエラーを防ぐには、何度も自己チェックする・第三者によるチェックを入れるなどの対策が必要です。
しかし、チェック作業には時間・手間・人的コストがかかるのが難点です。チェックにかかる時間やコストをできるだけ削減することが、多くの企業で課題となっています。
部門間でコミュニケーションが取れない
部門間でうまくコミュニケーションが取れていないことも、多くの企業が抱える課題です。部門間のコミュニケーションが不足すると、進捗状況の共有ができず全体のスケジュールが遅れたり、在庫不足によって生産がストップしたりといったトラブルが発生します。
部門間のコミュニケーションが不足する原因には、各部門が対立していることや、効率的なコミュニケーションの手段がないことがあります。
企業の方針が部門単体での評価だと、自部門の利益だけを考えた行動に走るケースもあるでしょう。また、拠点数が多い・製造工程が複雑化している・情報が一元化されていないことで、そもそもコミュニケーションをとるための環境が整っていない現状もあります。
コミュニケーション不足が発生すると、環境の変化やトラブルに迅速な対応ができません。環境変化やトラブルに迅速かつスムーズに対応するには、部門間でシームレスにコミュニケーションを取れる環境や体制の構築が求められます。
生産管理を改善するには
生産管理にはさまざまな課題があり、課題を解決することで生産管理を最適化することにつながります。ここでは生産管理の改善に役立つ6つの方法を紹介します。
生産準備を見直す
生産準備での問題点を見直し、改善することで、出戻り作業の発生防止や、各工程にかかる費用や人的コストの削減ができ、製造過程全体の効率向上が期待できます。
生産準備を最適化するには、まず生産準備にかける時間を確保し、必要な情報を入手することが大切です。現場の作業も重要ですが、生産準備に時間と労力をかけることで、今後の製造過程の効率化を図れます。
また、生産準備には多くの作業があり、部門をまたいだ協力が不可欠です。部門間での情報共有がスムーズにできるよう、適切なコミュニケーションが必要となります。生産準備に必要な情報を正しく・素早く共有することが大切です。
3視点で業務を見直す
「無くす」「減らす」「変える」の3つの視点で業務を見直すと、わかりやすく効率的に業務を改善できます。「無くす」は業務そのものを止めること、「減らす」は業務量を減らすこと、「変える」は業務内容を変えることを意味します。
「無くす」の対象となる業務は、必須ではないが昔からの慣習で残っている業務です。例えば、誰も確認することがない業務日誌への記入や、使っていない物品の管理などです。不要な業務を無くすことで、その分の時間をほかの作業に充てられます。
また、毎日チェックする内容がある場合、週一や月一などにまとめて行うようにすることで、業務量を「減らす」ことができます。
非効率な作業を改善するため、作業の一部や全体を「変える」ことも重要です。なお業務を変更する場合は、製造工程全体に影響が出る場合があります。業務の変更は慎重に行ってください。
業務をマニュアル化する
生産管理では、各工程の計画立案や関係者とのスケジュール調整などの、マニュアル化されにくい業務が多く、業務の品質やスピードが個人のスキルや経験に左右されがちです。特に、複雑な業務や不規則に発生する業務では、経験が浅い人と長い人でかなりの差が出ることもあります。
上記の問題を改善するには、あらゆる業務をマニュアル化し、作業時間の短縮や作業品質の安定を図ることが効果的です。業務をマニュアル化することで、誰がやっても一定のレベルで作業をこなせるようになります。
また、マニュアル化した業務を増やせば生産管理の最適化につながり、コスト削減や製品の品質向上、納期の短縮などの効果が見込めます。
属人化している業務を無くす
属人化している業務とは、特定の人にしかできない業務を指します。属人化している業務があると、担当者が欠勤したときに作業がストップしたり、退職や部署異動の際に引き継ぎ作業が困難になったりといった問題が発生します。
このような属人化している業務には、特別なスキルや権限が必要なケースもありますが、業務の可視化や情報共有ができていないために、業務が属人化してしまっているケースもあります。後者の属人化を解決し、生産管理を改善するには、業務内容の可視化と業務の標準化が効果的です。
業務内容を可視化すればフローが明確になり、業務のマニュアル化が可能になります。そして業務をマニュアル化できれば、誰がやっても一定の品質・スピードを保つことができ、業務の標準化を実現できます。
スモールスタートで始める
業務に課題が見つかり改善しようと思っても、一部の業務を変えることで製造過程全体に影響することがあるため、なかなか改善作業を実行できない場合があります。そのため、業務改善をスモールスタートで始めて、徐々に範囲を拡大していくことが大切です。
工程数や設備の規模にもよりますが、業務変更によって改善結果が出るまで大体2週間を目安にした計画を立ててください。重要なのは、2週間という短期間で確実に成果を出し、業務改善の成功体験を作ることです。
成功体験を多く重ねることで業務改善のノウハウが身に付き、改善点を効率的に全体へ広げられます。
PDCAを回す
業務改善は一回だけでは効果が少なく、何度も繰り返し改善作業を実施する必要がありますが、その際はPDCAサイクルを意識して取り組みましょう。
PDCAサイクルとは、Plan(計画)、Do(実行)、Check(評価)、Act(改善)の順に作業を繰り返すことです。PDCAサイクルは製造業だけでなく、あらゆる仕事の基本の考え方となっています。
PDCAサイクルを回せば作業を効率的に実施・評価できるため、業務改善活動においても有効な手段となっています。しかし、PDCAサイクルを回す際、具体的な数値目標を掲げていないことで、正しい評価ができない・作業の繰り返しになっているなどの問題が発生することがあります。
事前に目標値を明確にし、目標に向かってPDCAを回すことが重要です。
生産管理に欠かせないBOMとBOPとは
BOM(部品表)とは
BOMはBill Of Materialsの略称で、日本語では部品表または部品構成表と呼ばれます。製品の組み立てに必要となる部品を表や構成図で記したもので、BOMを見れば製品がどの部品から成り立っているのかが一目でわかるようになっています。
BOMは管理方法と用途によって何種類かに分類され、部門や製造過程によって使用するBOMが異なります。例えば、管理方法ではサマリ型・ストラクチャ型・パラメトリック型などに、用途としてはM-BOM・E-BOM・S-BOMなどに分けられます。
BOMのメリットには、部品の管理を効率化できる・製品の品質を保てる・在庫管理が容易になるなどがあります。一方BOMの課題には、製品の多品種化によりBOMの作成自体が困難である・部門ごとに品名や部品コードが異なるため統一化できないなどがあります。
BOMを活用すると、部品の在庫が足りない、手配が漏れている、といった事態を回避できるため、結果的に生産管理の効率化が可能です。
BOPとは
BOPはBill of Processの略称で、日本語では工程表と呼ばれます。BOPは、製品の組み立てや部品ごとの加工の工程を示します。BOPには主に、図面・工程名・工順・品質チェック項目・使用する設備・製造条件などが含まれます。
また、BOPはBOMの概念を拡張し、工程・設計情報を統合して管理するという基本概念やデータシステムを差す場合もあります。BOPシステムの導入によって開発設計と製造工程を連携させられるだけでなく、生産に関するさまざまなデータの一元管理が可能です。
現場の設備や工程、製造条件といった社内に散在していた情報を一箇所にまとめ、製品や部品の構成情報以外にも、製造工程や生産技術情報も統合して管理することで、コスト削減や開発プロセス短縮などの効果が期待できます。
BtoBの製品で重要視されるのは、どんな製品を作るのかよりも、どうやって作るかという工程作業を効率化することです。製品競争力を強めるため、BOPの管理や活用ができるシステムに注目が集まっています。
生産準備におけるBOM / BOP管理の課題
BOMとBOPは製品の構成部品や部品の組み立て工程などを可視化でき、生産管理の効率化に有効です。しかし、多品種少量生産による製造工程の煩雑化や、部門ごとに個別化された内容などが原因で、BOMやBOPの管理が難しくなっています。
また、BOMはExcelや紙で作成・活用されている場合が多いですが、人の手による入力作業ではミスが発生しやすいことも課題です。特に、サイズ・色違いのバリエーションが多い製品では部品数も膨大で、手作業で部品コードやメーカー名を入力するには限界があります。
BOMとBOPが抱える課題を解決するには、BOM・BOP管理のシステム化が必要です。システム化することでBOM・BOPの作成を自動化したり、複数のBOM・BOPを一元管理したりできます。
▼カシオ計算機では、カスタマイズサービス「MY G-SHOCK」の実現に向けて、マスターBOM生成エンジンを導入し、受注生産体制の構築と業務効率化を達成しました。
導入事例:カシオ計算機株式会社様はこちらからダウンロードできます。
BOM管理を自動化する「SPBOM」で生産管理の課題を解決
「SPBOM」は、BOMにおける従来の課題を解決できるソリューションサービスです。多品種少量生産にも対応可能なBOM・BOP管理システムであり、登録したルールに則ってスピーディーにBOM、BOPを自動生成します。
SPBOMが優れているのは、ERPとの連携が可能である点です。ERPや生産管理システムなど自社の既存システムと連携させることで、受注データに基づいてBOMやBOPの自動生成を行えるため効率的です。システムによる自動化でヒューマンエラーの減少にもつながり、さらなる生産性向上につながります。
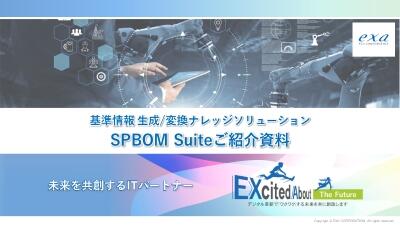
SPBOM Suiteご紹介資料
マスカスタマイゼーション実現のためにSPBOM Suiteで解決できることや導入事例についてご紹介しています。
生産管理の改善事例・SPBOMの導入で機会損失を大幅減!
SPBOMの導入により、生産管理の最適化、および工数の削減や納期の短縮を実現できます。
SPBOMを導入して課題を解決した事例として、株式会社LIXILの事例を紹介します。
株式会社LIXILは、以下の点を実現するためのシステムを求めていました。
- 膨大な製品数の即納を実現し、顧客満足度の向上と欠品による機会損失を削減すること
- 数千万アイテムある製品の多品種少量生産を国内の工場で実施し、受注後に即出荷する
- 事業や工場ごとに異なるルールやプロセスがあることで、製品、半製品、原材料の過不足が発生し計画の変更業務の手間が増えることの解決
上記を実現するため、統合生産システム構築のメインとしてSPBOMを導入し、周辺システムへ連携することにより以下の効果がありました。
- 受注時にリアルタイムでBOMを生成でき、生産リードタイムを大幅に短縮
- システム別、用途別に異なるBOMをそれぞれSPBOMが自動変換し、配信が可能(One Source multi-Use)
- 商材個別最適で管理していた データ構造、データ項目を「 SPBOM基盤 」で一元管理
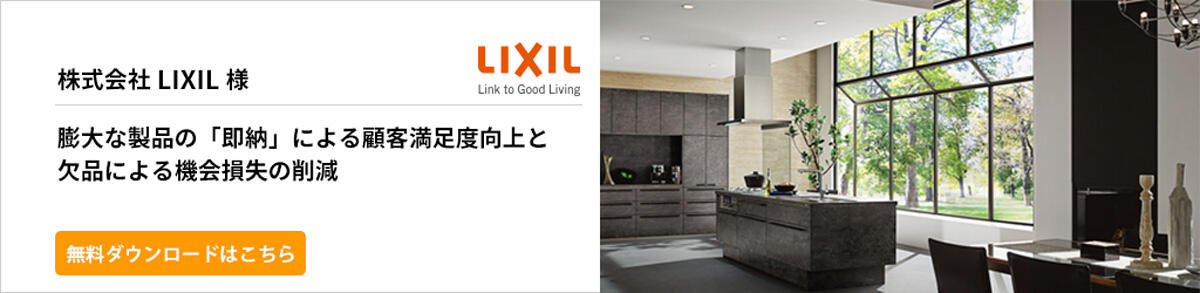
まとめ
関連する記事
関連ソリューション
関連事例
お問い合わせ
CONTACT
Webからのお問い合わせ
エクサの最新情報と
セミナー案内を
お届けします
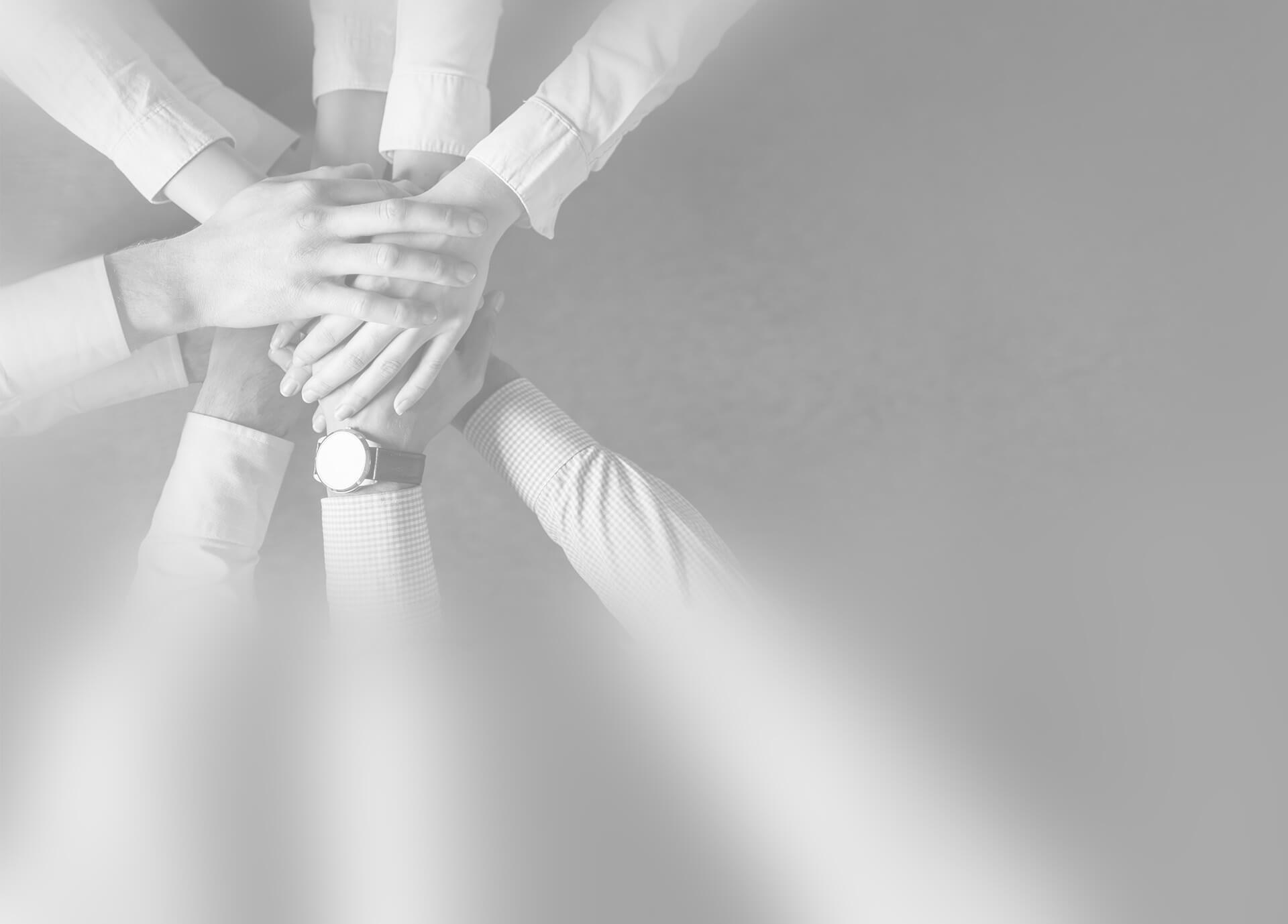