昨今のビジネス環境(販売・生産のグローバル化、ニーズの多様化や製品ライフサイクルの短期化、熟練技能者の減少など)の
急激な変化や既存システム(部分最適なシステムの乱立、基幹システムとのマスター不整合、品番の更なる増加など)への
対応力が求められる今日、多くの製造業では特に製造基準情報(BOM/BOP)のAgility獲得が課題となっています。
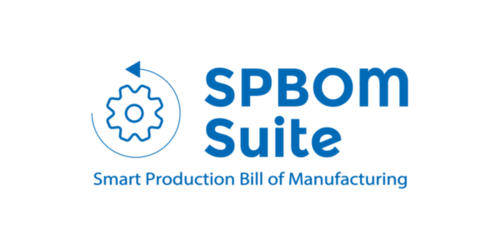
SPBOM Suiteとは
SPBOM Suiteは、ものづくりのノウハウをナレッジとして管理し、
製造基準情報の生成と変換、連携するソリューションです。
製品の製造に関わる業務で必要な静的な製造基準情報を全て抱えることなく
都度自動出力することで業務の効率化を実現し、また、SCM / ERP / MES等の
システム毎に必要な粒度や属性などを統合管理し、整合の取れた製造基準情報を
効率的に目的別システムへ配信する全社製造基準情報基盤として効果が期待できます。
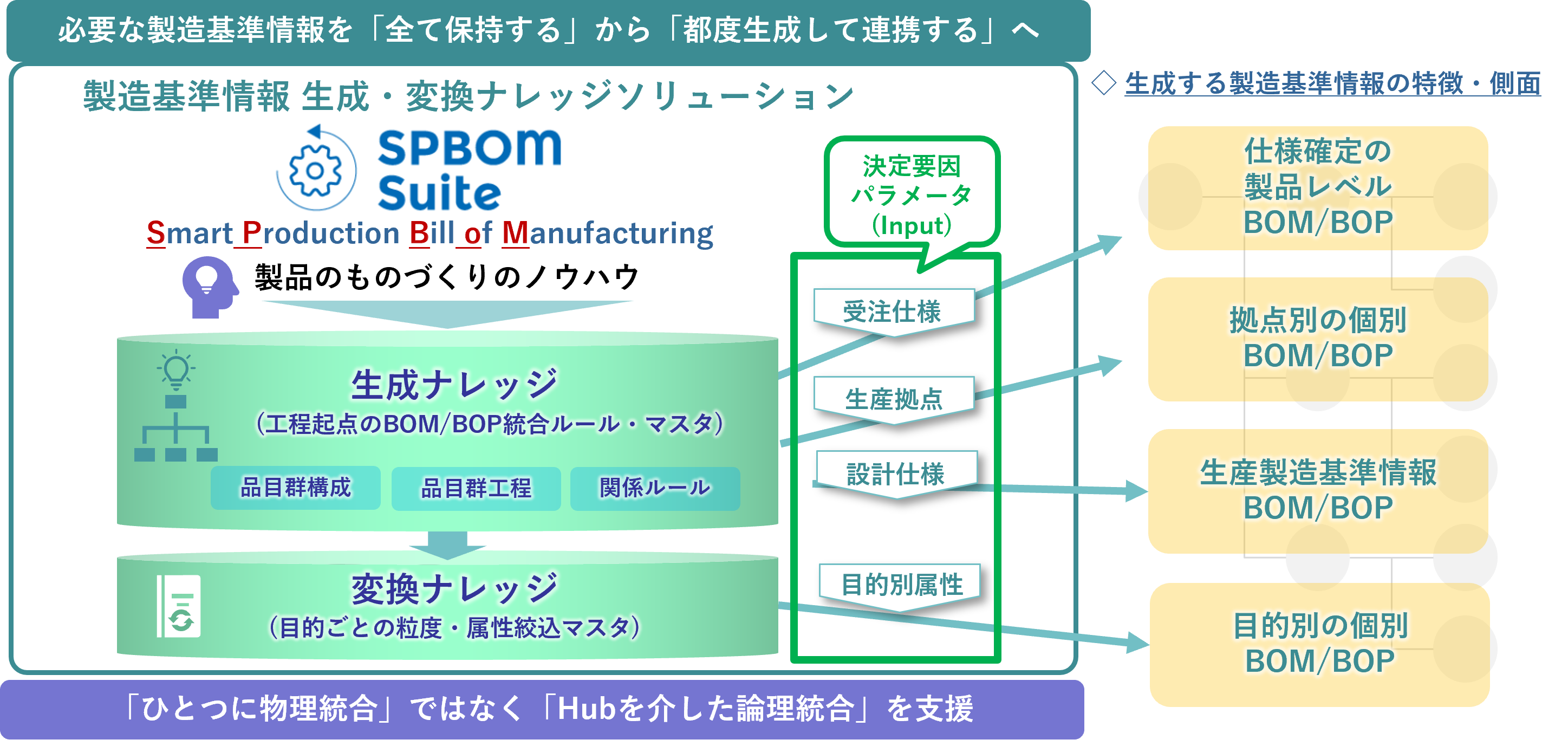
SPBOM Suiteの導入効果
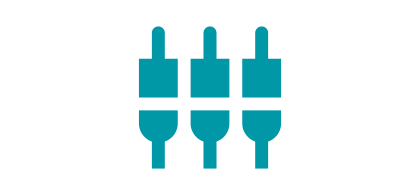
受注情報からBOMを
自動生成
・生産システムと連携し、製造指示までのL/Tの大幅な短縮
・システム毎に異なるコード体系の自動変換も可能
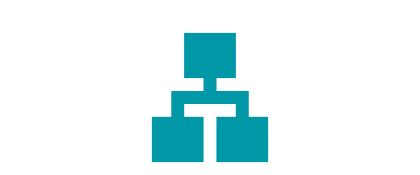
生産拠点、工場、ラインごとのBOM/BOPを自動生成
・生産サイクルタイムや積上原価もリアルタイムに把握
・素材の品番違いや中間在庫品を自動でBOM切替
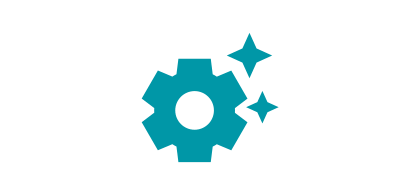
各システム単位にBOMを自動配信
・既存システムを変更せずにBOM連携が可能
・BOM/BOPの統一が難しい場合、全社Hub基盤としての利用も可能
・リアルタイムに生産計画や調達計画に連携し、欠品・過剰在庫を削減
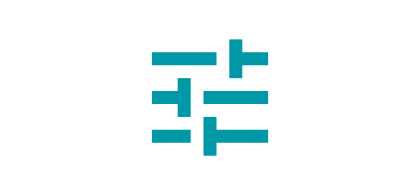
EBOM-MBOM連携
・独自の変換ルールにより正確かつ迅速な自動変換
・属人化が排除でき、標準化による精度や生産性が向上
ものづくりにおける製造基準情報(BOM/BOP)管理の課題
ビジネス環境の変化や既存システムの対応力が求められる今日、多くの製造業では特に製造基準情報(BOM/BOP*)のAgility獲得が求められています。
- 新製品や販売地域限定品の増加やグローバル化による販売/生産拠点の拡大・細分化
-
同じ製品でも、生産拠点ごとに生産プロセスが異なるケースがあり、製品+拠点ごとの製造基準情報(BOM/BOP)を用意する必要がある。
- ニーズの多様化による多品種化・製品仕様の複雑化
-
製品バリエーションやシリーズ製品が増加し、膨大な数の製造基準情報(BOM/BOP)作成が必要となり、類似データが大量に存在することで、人手によるメンテナンスが限界となっている。
- ニーズの急速な変化による製品ライフサイクルの短期化
-
ERP、生産計画、MES等の各システムは、各々異なる粒度と情報の基準情報(BOM/BOP)を必要とし、それらを人が個別に作成しているため、多大なコストとリードタイムが掛かっている。
- 就業人口減少による業務負荷の増大・属人化
-
製品数増加に伴い、製造基準情報(BOM/BOP)作成ノウハウを持つ熟練者の業務負荷が増大している。
属人化により、同じ製品でもシステム間差異(製造基準情報(BOM/BOP)の同期が取れていない状態)が発生してしまうことがある。
SPBOM Suiteが独自のしくみで解決
SPBOM Suiteは、動的ルールから目的に依存しない汎用的なBOM/BOPを生成する[生成ナレッジ]と、目的別に必要な形式変換と情報付加、そして必要なタイミングでの連携を行う[変換ナレッジ]に分けて管理します。この2段階ナレッジにより、目的別のBOM/BOPを矛盾なくかつ効率よく生成する事が可能となります。
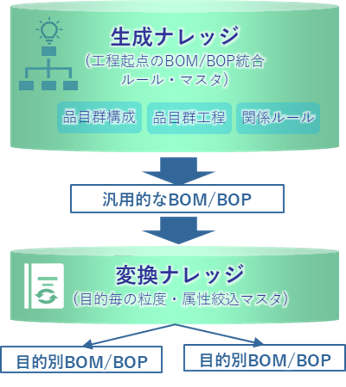
- 生成ナレッジでの実現例
-
受注仕様、拠点、設計仕様を指定すると、ルールが埋め込まれたSPBOM Suiteデータモデルから、製造に必要なBOM/BOPが都度自動生成され利用可能となります。
- 変換ナレッジでの実現例
-
共通のSPBOM Suiteデータモデルから目的別システムごとに変換することで、整合のとれたBOM/BOPが利用可能となります。
お客様の声
SPBOM Suite活用ユースケース
活用ケース① 受注情報からのBOM/BOP生成
全社ERP等からの案件受注情報に基づいた製品仕様から、BOM/BOPを自動生成し、生産管理システムへ即座に連携することで、従来時間を要していた製造指示までのLTが大幅に削減されます。
SPBOM Suiteで可能となる具体例
- ERPと生産管理システムでコード体系の違う品目コードを自動変換できほぼリアルタイムに連携
- 在庫引当・資材発注や外注手配・生産指示が速やかに繋がり、製造L/T短縮及び管理コスト削減が可能
- 新規バリエーション製品の受注の際も自動変換ルールにより設計を介さずBOM/BOP生成が可能
- 受注時にBOM/BOPが自動生成され、工場負荷による代替生産拠点割り当て等が迅速に対応が可能
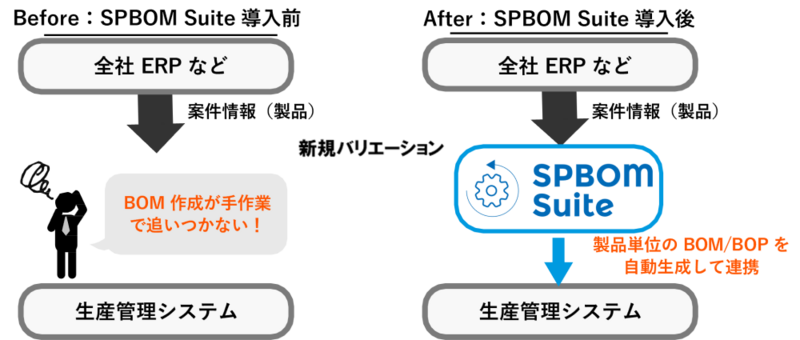
活用ケース② 生産拠点ごとのBOM/BOP生成
生産拠点ごとに異なる生産プロセスの組合せルールをSPBOM Suiteに登録しておくことで、同一製品に対して生産拠点に応じたBOM/BOPを迅速に生成します。
SPBOM Suiteで可能となる具体例
- 工場・ライン違いによる生産サイクルタイムや積上原価集計計算が可能
- 各生産拠点とリアルタイムな連携により、生産変動への対応や無駄な滞留を防止
- 工場・ライン違いにより発生する素材の品番違いや中間在庫品(ファントム)を自動でBOM切替が可能
- 新しい工場展開の際にも工程生成ルールを流用することでルールマスター登録の時間短縮が可能
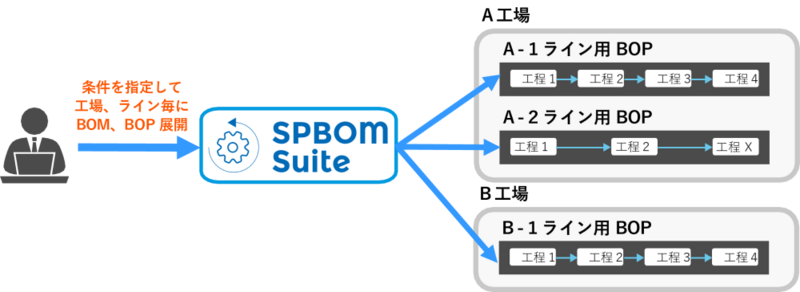
活用ケース③ 全社BOM/BOP連携基盤活用
SPBOM Suiteの汎用的データモデルにより、各システム毎に必要な粒度や属性などを統合管理し、整合の取れたBOM/BOPを効率的に目的別システムへ配信する全社BOM/BOP基盤として活用できます。
SPBOM Suiteで可能となる具体例
- BOM/BOPを自動生成・連携可能となり、目的別システムに応じた変換作業が大幅に削減可能
-
迅速に鮮度の高いBOM/BOPを連携することにより、現実に即した生産計画および調達計画の結果、欠品・過剰在庫の削減が図れ、納期遵守率が向上
- 積上げ原価や4M*1情報を基にシミュレーションを行い原価や工程見直しのカイゼン活動が推進可能
- MTS*2からBTO/CTO*3等へのビジネス変革の際、既存システムを変更せずBOMの連携可能
-
部門ごとに乱立しているBOM/BOPをひとつに物理統合するのが難しい場合、SPBOM SuiteをHubとして論理的に連携する事が可能
*1 4M: Man/Machine/Material/Method
*2 MTS(Make To Stock): 見込生産
*3 BTO(Build To Order)/CTO(Configure To Order): 受注組立生産
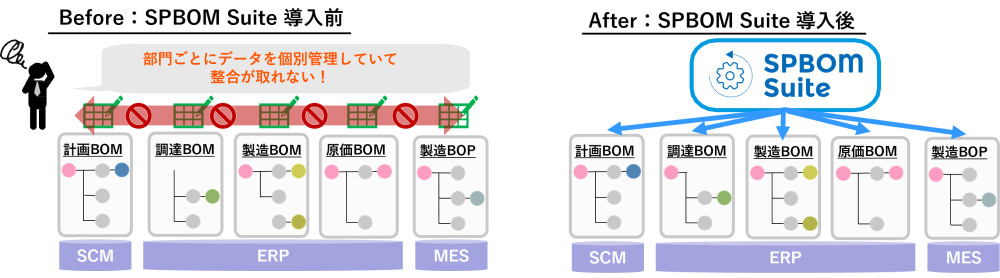
活用ケース④ EBOMとMBOMを連携
システムによる管理、または手動連携による負荷増大や不整合による手戻りが課題となっている EBOMとMBOMの連携が、SPBOM Suite独自の変換ルール活用により正確かつ迅速に実現できます。
SPBOM Suiteで可能となる具体例
- 品目コード単位のEBOMを品目コード単位のMBOM/BOPに自動で変換可能
- 設計変更の取り込みでは変換したMBOM/BOPの変更差分を抽出可能
- EBOMをベースにMBOM/BOP情報を手動で追加、編集する作業が不要となるため大幅なL/T短縮が可能
- 変換ルール活用により属人化(設計や生産の熟練者依存)が排除でき、標準化による精度や生産性の向上が可能
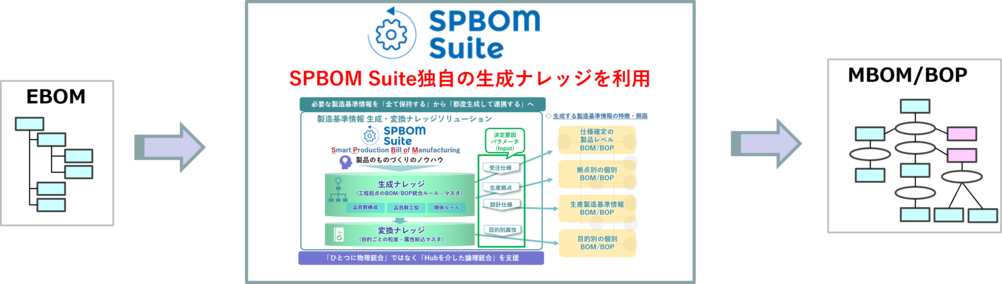
ECMとSCMをつなぐソリューション例
日本の多くの製造業は多品種少量生産へのシフトを加速しています。また、見込み生産主体の製造業でも受注生産によるカスタマイズ、個別仕様製品の比率が増える傾向にあります。
PLMを導入することでモノづくりの要となるEBOM・MBOMの整合性をとることを可能にします。一方で、カスタマイズ、個別仕様製品のBOMを全てマスタとしてPLM上に事前に用意するとマスタの肥大化に繋がります。
結果として、PLMのメンテナンスの問題やパフォーマンスの劣化を招き、ECM/SCMプロセス全体のAgilityが欠如します。
このような多くの製造業で抱える課題を解決すべく、SPBOM SuiteはHi-PerBT PLM(製造元:株式会社日立ソリューションズ西日本)との連携を可能にしました。
PLM製品単独の運用において課題となる「カスタム仕様を含む全MBOMの事前登録」と「バリエーション展開に応じた目的別BOMの作成・メンテナンス」をSPBOM Suiteが担うことでECM/SCMプロセスの最適化を実現します。
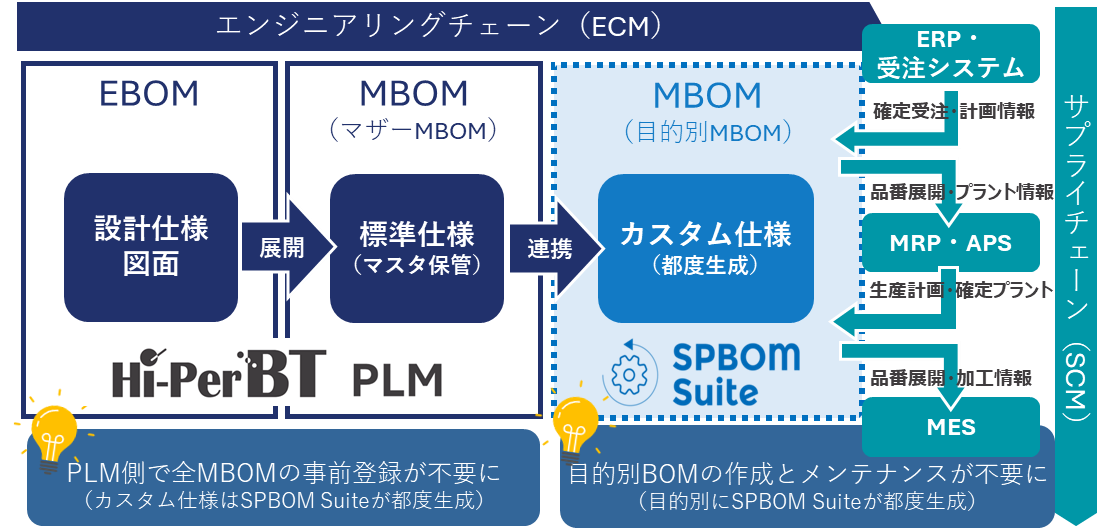
SPBOM Suiteご紹介資料
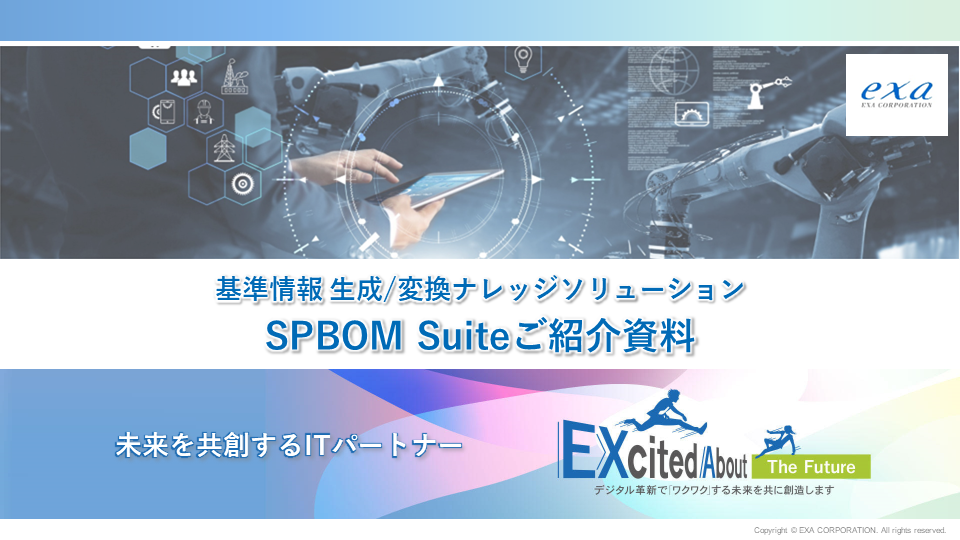
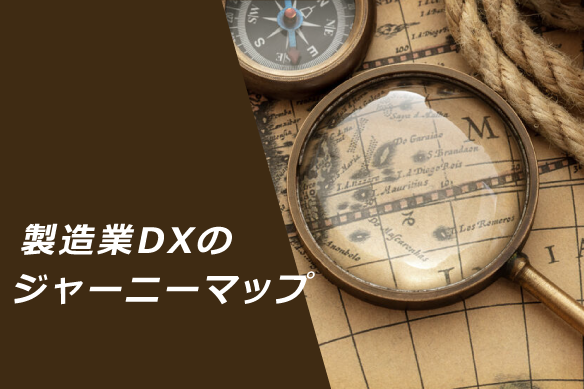
製造業DXのジャーニーマップ
製造業のDX動向や、私たちに寄せられたお客様からのご相談内容や共に手掛けた実績を元に、国内製造業がDXを推進していく上での地図を「製造業DXのジャーニーマップ」として取り纏め、DX取組みのテーマの検討やロードマップを策定する上でのベースラインとしています。
また、ビジネス変革に向かう製造業DXのジャーニーマップに沿った取り組みの方向性や、それを支援するソリューションや事例などをご紹介します。
導入実績例
産業用素材メーカー様
標準原価の作成・改善、実際原価の把握などを目的とした原価管理システムにSPBOM Suiteを採用。全社ERPから連携される製品情報に対応したBOMを都度自動生成し原価管理システムに連携することで、原価積み上げ、実績収集などに利用される基礎データを提供。また、BOM一括再生成による原価改善作業の効率化にも活用。
ポンプメーカー様
受注生産型の大型産業機械における日程管理システムにSPBOM SuiteとAsprovaを採用し生産管理に適用。製造工程における計画作成ノウハウの蓄積と計画の見える化によって迅速な納期回答,生産リードタイム短縮およびコスト削減を実現。
建材メーカー様
生産管理システム再構築において部品表データ散逸、図面・BOM作成の作業負荷大という課題解決のためSPBOM Suiteを採用。SPBOM Suiteによる部品表作成ルール一元管理、製品仕様に応じた部品表自動生成の仕組みを実現。また、寸法値自動算出を活用し図面作成省略も可能となり、製造リードタイム、作業工数削減に貢献。
導入事例
関連情報
関連ソリューション
エクサを知る
お問い合わせ
CONTACT
Webからのお問い合わせ
エクサの最新情報と
セミナー案内を
お届けします
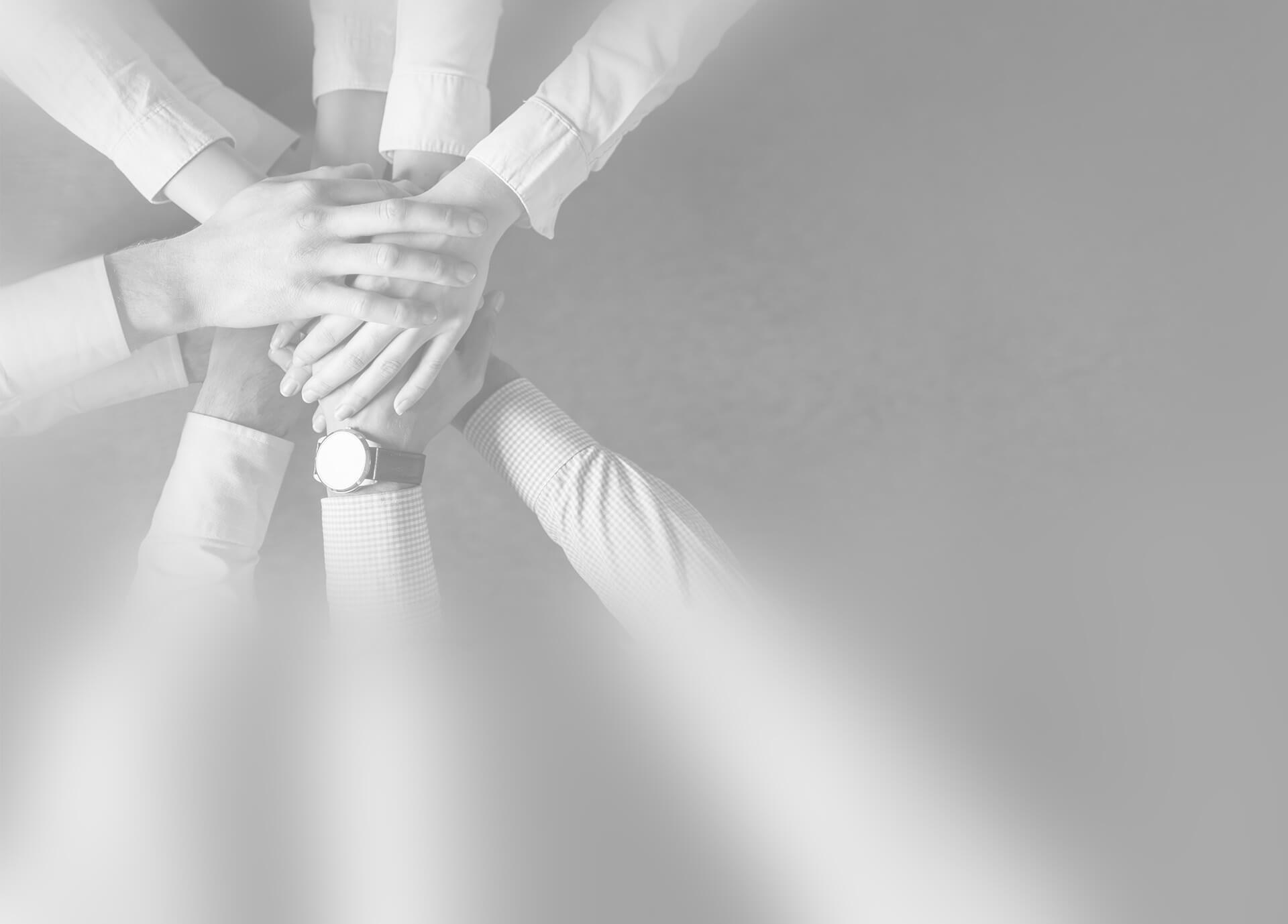