製造現場において、設備を安定稼働させることは、品質維持や従業員が安全に働ける環境づくりの観点から重要です。中でも設備の安定稼働には、「予防保全」が有効です。本記事では、予防保全の方法や予知保全・事後保全との違い、重要性やメリットなど、予知保全に関する知識を解説します。
予防保全とは
予防保全とは、トラブルが起こらないための予防策として行われる、設備保全の一種です。
製造業などの現場において最大限にリスクを下げるためには、「トラブルが起こらない環境」を整える対策が有効です。もちろん、トラブルは起こってしまった後の対処も重要ですが、そもそもトラブルが起こらなければ重大事故につながることもありません。そのため、日頃から予防保全として点検作業などを徹底し、設備を安全に稼働させられる状態に保つことが重要です。
予防保全では、法規・法令に従って定期的な保全作業をすること以外に、工場内の設備が故障したり不具合を起こしたりすることを防ぐために、自主的に決められた項目に従って定期的に保全業務を行います。
予防保全の方法
ひと口に予防保全といっても、方法はさまざまです。予防保全は、主に「TBM」「CBM」「RBM」「RCM」の4種類に分けられます。
TBM(Time Based Maintenance)とは、時間を基準にした定期メンテナンスを行う手法です。一定期間が経過したタイミングで部品交換を行い、現場のトラブルを防止します。長すぎず短すぎない、適切なメンテナンスの間隔を設定することが、現場のトラブルを防ぎつつ、運用コストを最小限に抑えるためのポイントです。
CBM(Condition Based Maintenance)は、定期的に設備の状態を点検し、不具合や状態の悪化が見られれば、必要に応じて部品交換や修理を行う手法です。点検結果によって対応が異なるため、設備の状態を正確に判断するための、明確な基準を設けなければなりません。
RBM(Risk Based Maintenance)は、故障リスクを評価し、評価結果に基づいてメンテナンスを行うかどうかを判断する手法です。「故障しているか、していないか」という2つの判断基準ではなく、「故障した場合のリスク」や「将来的な故障の可能性」について評価する点が特徴です。
RCM(Reliability Centered Maintenance)は、故障データを収集し、故障のパターンや発生しやすい箇所などを特定して、最適な保全方式を適用する手法です。機器について深く調査して機器の信頼性を高め、信頼性に応じて効果的な手法を選び出します。
予防保全を行うために必要なこと
予防保全の場合、事前に作成したスケジュールに沿って保全業務を実施する必要があります。そのため、中長期および年間の保全スケジュールを策定し、保全のタイミングをメンバーで共有することが大切です。また、保全業務における保全基準や、実施手順を明確に定めることも求められるでしょう。
故障やトラブルを防ぐための、自主的な予防保全のスケジュールは、どのようにして決めるのでしょうか。多く見られるのは、メーカーが提示する使用回数や期間と、現場の保全担当者の知識や経験を掛けあわせて決める方法です。これまでの経験や勘に基づいて、適切なスケジュールを策定すれば、現場でトラブルが発生する前に部品交換や修理を行い、常に安全な状態を維持できる可能性が高まります。
ただし、部品交換や修理のサイクルが短すぎると、まだ故障とは無縁の時期に、十分に使用可能な部品や機器を交換してしまうことになるため、コストに無駄が生じるかも知れません。この観点からも、点検スケジュールを最適化できているかどうかは重要です。
また、保全基準が明確に定められていないと、担当者によって判断基準にばらつきが生じて、想定外のトラブルを招く原因になります。保全に関しては、いつ、誰がどのように実施するのかなど実施手順を定めてマニュアルなどに明文化しておくことで、作業の抜け漏れなどを回避しましょう。
予防保全と似た用語との違い
予防保全と似た言葉として、予知保全や事後保全があります。ここでは、これら2つの言葉がどのような意味を持つのか、予防保全と比較しながら解説します。
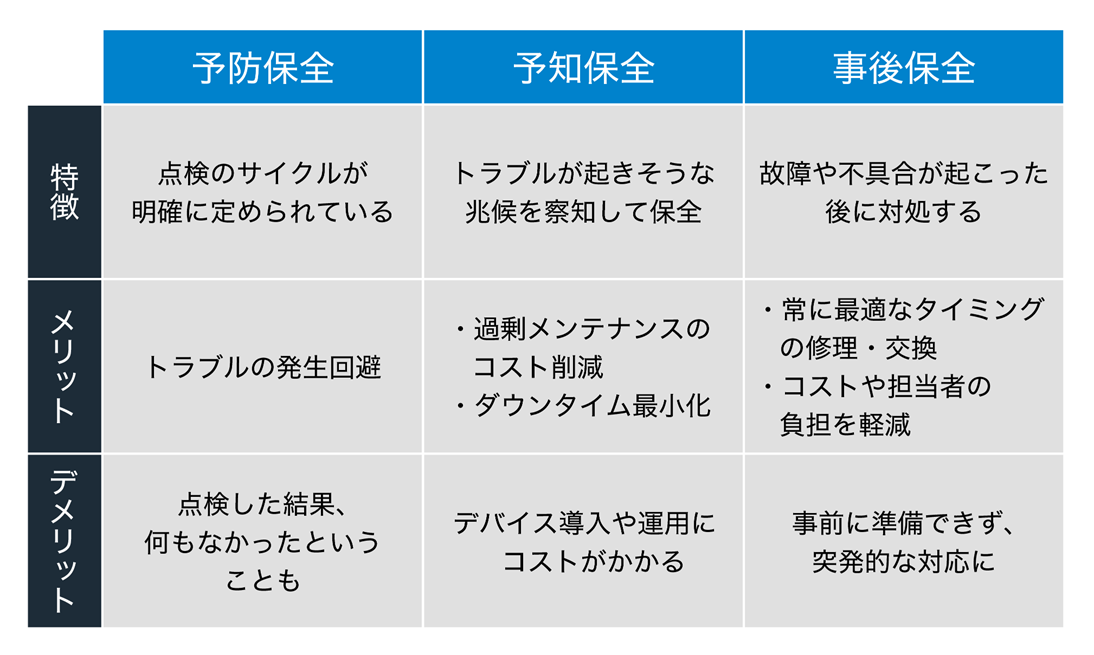
予知保全との違い
予防保全と予知保全の違いは、簡単に言えば「定期的に行うか」という点です。
予防保全は、事前にメンテナンスのスケジュールを立てて点検し、部品交換や修理の必要性を判断します。2週間、1ヶ月、3ヶ月など、あらかじめ点検のサイクルが明確に定められているのが特徴です。
裏を返せば、問題が起きそうかどうかに関係なく、決められた時期になれば、点検する必要があります。実は何も問題はなかった、といった結果になりうることも十分考えられ、点検にかかるコスト負担が増えることも、十分想定しておかなければなりません。
一方、予知保全は、メンテナンス時期をあらかじめ決めることはありません。その代わり、トラブルが起こりそうな兆候を、IoT(Internet of Things:モノのインターネット)やAI(Artificial Intelligence:人工知能)を駆使して察知し、保全するのがポイントです。つまり、IoTにより収集されたデータを、AIに解析させて、トラブルがそろそろ起きそうな時点でメンテナンスを実施します。予防保全と異なり、過剰にメンテナンスすることでかかるコストを削減でき、停止期間であるダウンタイムを最小化できるメリットに、近年注目が集まっています。
しかし予知保全は、IoTデバイスなどの導入や運用にコストがかかるのがデメリットです。過剰メンテナンスやダウンタイムを抑制することで得られるメリットとのバランスを見ながら、導入を検討するとよいでしょう。
事後保全との違い
事後保全とは、「故障や不具合が起こった後に」対処する手法のことです。予防保全や予知保全は、トラブルが起こる前にメンテナンスし、トラブルの発生そのものを回避する目的で行われます。一方、事後保全の場合は、トラブルが起こるまであえて特別な対処を行いません。
もちろん、定期的にメンテナンスを実施する予防保全とは異なり、事前に準備できず突発的に保全対応しなければならない点や生産計画に影響を及ぼしてしまう点はデメリットです。しかし、実際にトラブルが起きていることから、常に最適なタイミングで修理・交換ができる方法とも考えられるでしょう。かかるコストや保全担当者の負担の軽減を図りやすい点はメリットです。
予防保全の重要性
予防保全は、設備稼働の安定性を確保したり、想定外のトラブルによって設備や装置にダウンタイムが生じ、生産性が低下することを防いだりするために重要な取り組みです。
適切な予防保全が行われていなければ、稼働中に突然設備が停止して生産に悪影響を及ぼすおそれがあります。生産に遅延が発生すれば、納期遅延を招き、売上低下につながるだけでなく、企業としての信頼を大きく損ねることも考えられるでしょう。
また、設備にトラブルが生じると安全な稼働を維持できなくなり、現場で働く従業員の安全性が損なわれるリスクも高まります。
予防保全のメリット
予防保全のメリットとして、品質低下の抑制やダウンタイム発生の減少、働き方の改善などが挙げられます。これら3つのメリットをすべての従業員と共有できれば、より保全の効果を高められるでしょう。ここでは、それぞれのポイントを分かりやすく解説します。
品質低下の抑制
設備に故障や不具合を抱えた状態で生産を続けると、品質低下のおそれがあります。不良品の出現率が増えれば、検知・排除の手間も増加し、生産現場全体の運用コストが膨らむでしょう。また、品質の低い製品を大量に生産すれば、不良や廃棄につながりやすく、その分だけ原料や資源に無駄が生じる点もデメリットです。
設備に不具合が起こる前に予防保全を行うことで、品質低下を回避でき、安定的な品質維持を図れます。検知コストを軽減でき、原料や資源の無駄も抑制可能です。製品を使うユーザーからの評価も高まってリピーターが増加し、新規顧客を取り込みやすくもなることも期待できます。
ダウンタイム発生の減少
設備にトラブルが生じると、トラブル解消のためのダウンタイムが発生します。ダウンタイムとは、トラブルなどで製造がストップする期間のことです。事態が複雑化すると長期的に稼働が停止するケースもあるため、生産計画に大幅なずれが生じるリスクも高まります。長期化しなくても、タイミング悪く繁忙期にダウンタイムが発生すると、大きな痛手になりかねません。
予防保全では一定周期で部品交換や修理をするため、設備トラブルのリスクを減らし、ダウンタイム発生を抑制することが可能です。結果的に、製造現場全体がスムーズに稼働し、生産性向上にもつながります。安定して製品を供給できるようになることで、取引先や顧客からの信用も高まるでしょう。
働き方の改善
予防保全は、働き方改革やワークライフバランスの実現にも高い効果を発揮します。
日本では近年少子化が進み、とくに労働の中心的存在となる15歳から64歳人口が20年以上減少を続けています(2023年1月時点)。
参照:図3「年齢区分別人口の割合の推移(1950年~2021年」
https://www.stat.go.jp/data/jinsui/2021np/index.html
「年齢(5歳階級)、男女別人口(2022年8月確定値、2023年1月概算値)」
https://www.e-stat.go.jp/stat-search/files?page=1&layout=datalist&toukei=00200524&tstat=000000090001&cycle=1&year=20230&month=11010301&tclass1=000001011678
限られた人材を確保するため、2019年4月からは「働き方改革関連法(働き方改革を推進するための関係法律の整備に関する法律)」が順次施行され、各企業に柔軟な働き方の推進が求められています。
事後保全はトラブルが起こってから対処する保全方式であることから、想定していないタイミングで、緊急に対応しなければならないことがあります。休日や退勤後の夜間に呼び出されるなど、メンテナンス担当者の負担が重くなりがちです。
一方、予防保全によって想定外のトラブル対応の可能性を下げるなら、勤務時間外の呼び出しを抑えられ、従業員にとって負担感の強い働き方を避けられます。現場の労働環境が改善されれば、人材の流出を防ぎ、定着率を高められるでしょう。人的リソースの確保は、製造業全体として喫緊の課題でもあるため、大きなメリットです。
予防保全のデメリット
さまざまなメリットがある予防保全にも、注意すべき点があります。
まず、前述したように定期的なメンテナンスを定めていることから、異常がなくても作業のための労力や費用を要する点です。予知保全は何かしらの異常を感知している状態で、事後保全はすでに問題が起きた状態で保全対応するため、いずれもメンテナンスは不可欠なものです。よって発生する工数は必要最小限のものといえます。一方、予防保全は異常の予兆がなくても工数を確保しなければならず、予知保全や事後保全よりも全体の作業工数が多くなってしまいます。
また、自主的な予防保全のスケジュールを決める際には、メーカーの推奨するタイミングのほか、現場担当者の経験や勘といった要素に頼ることも少なくありません。場合によっては判断を誤っていることもありえるでしょう。もし最適なタイミングで実施できていたとしても、保全業務の属人化にもつながる点が問題視されています。
予防保全を行う際におさえておくべきこと
1. 作業工数が増える
たとえ現場が正常に稼働していたとしても、定期的にメンテナンスのために稼働を停止する必要があり、メンテナンスのためにも一定の工数を要します。
2.コストがかかる
一定の周期で部品交換などを行うため、トラブルが起きた後に対応する事後保全よりも回数が増える分コストも上がります。かけるべき保全コストをあらかじめ算出しておき、運用後に実際にかかった保全コストと比較して、コストの最適化を図ることが重要です。
3.スケジュール通りにできないこともある
もともと事後保全を実施していたり、故障対応が頻発したりする場合、現在起きているトラブルの解消が最優先されるために、予防保全のスケジュールに従えないこともあるでしょう。そして予防保全ができないとトラブルが起きやすくなり、悪循環からますます抜け出しにくくなります。
IoT活用で予防保全から予知・予兆保全の時代へ
「予防保全」には、品質維持やダウンタイムの抑制などさまざまなメリットがありますが、定期メンテナンスによるコストの増大などの懸念点があります。予防保全のメリットを残しつつ、懸念点を解消すべく近年注目されているのがIoT・AIなどの最新テクノロジーを活用した「予知・予防保全」です。
法令点検や自主点検など、計画に基づいた「予防保全」から、今後はIoT・AIなどのデジタル技術を用いた「予知保全」に製造現場全体がシフトしていくと考えられます。IoTやAIなどのデジタル技術の導入が進むことで、データの分析や利活用が容易になり、CBMやRBM、RCMなどの高度な保全が実現可能です。予知保全の取り組みは、故障予測などのモデルを作ることに時間と労力を要するため、ダウンタイムが発生してしまうと損失が大きい設備など、優先度・重要度を考慮して予知保全をするべき対象設備を絞ってスタートすることが大切です。
設備の故障予測に限らず、稼働データ解析も現場の生産性向上に寄与するでしょう。IoTによって、製造現場では生産にかかわるさまざまなデータを収集し、統合的に可視化できます。蓄積したデータをAIで分析・解析することにより、安定稼働を実現しつつ、保全活動の効率化にもつなげられます。
予防保全の定期メンテナンスでは、まだ使える部品にもかかわらず新品に交換するケースも少なくありません。予知保全であれば、AI予測によって最適なタイミングで部品を交換できるため、資源やコストの無駄も削減可能です。
まとめ
予防保全への取り組みは、品質維持や現場の生産性向上に有効です。予防保全を実現し、将来的に予知保全を実現するためには、拡張性の高いソリューションを選定する必要があります。「IBM Maximo」は将来的な予知保全を実現するソリューションが備わったプラットフォームです。
設備管理領域のデジタル化を促進することで、収集したデータに基づくさまざまな状況把握や予防保全、業務改善などをサポートします。
連載コラム AI・IoTによる未来の保全
関連する記事
関連ソリューション
関連事例
お問い合わせ
CONTACT
Webからのお問い合わせ
エクサの最新情報と
セミナー案内を
お届けします
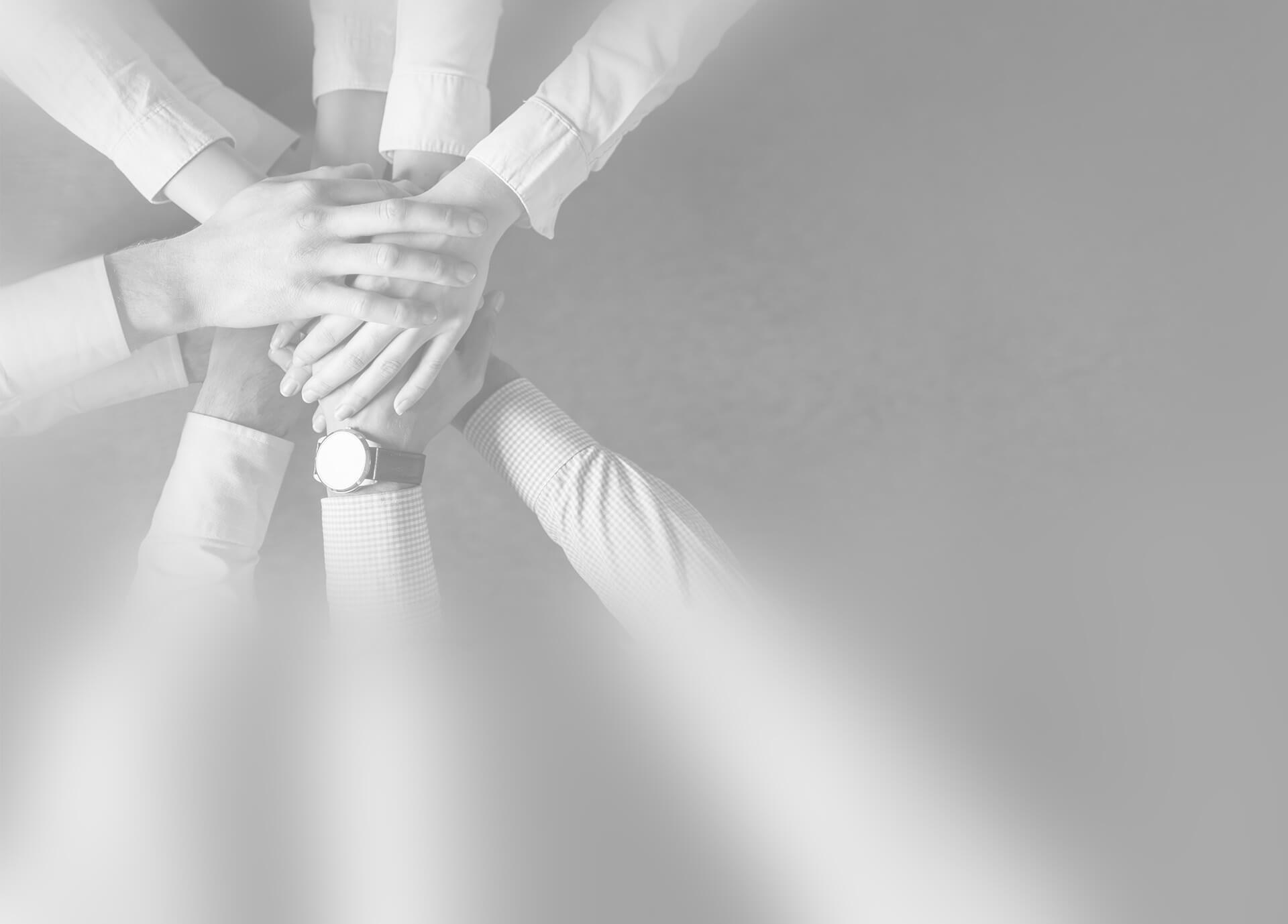