現場の全員が協力体制を取って生産保全を行うTPMは、40年以上前から製造現場に取り入れられている考え方です。近年は、サステナビリティ経営などの観点からあらためて注目されています。本記事では、TPMの基本的な考え方や「16大ロス」の定義、ロスを防ぐ「TPMの8本柱」について解説します。
TPMの考え方は、ロスの最小化を通じて生産性を高めるだけでなく、エネルギーや人員といった経営資源のムダ削減にも直結します。ロスを放置すれば、コスト増や生産性低下といった悪循環を招く可能性もあるため、中長期的な収益性や持続性を確保するうえで、改めてTPMを見直すことが重要です。設備の故障・停止といったロスを最小化するための考え方や、TPM推進に役立つ設備保全管理システムの活用法を詳しく知りたい方はダウンロード資料をご活用ください。
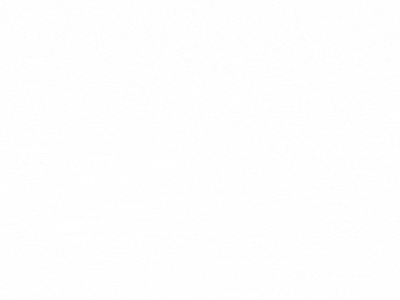
TPM活動の成果を最大化するには?
現場でTPMを実践するためのステップや、設備保全管理システムの活用法を1冊にまとめました。基礎から実践まで知りたい方は、ぜひご活用ください。
TPM(Total Productive Maintenance)とは?
近年注目されているTPMとは、現場の全員が協力して行う生産保全のことです。まずは、TPMの概要や基本的な考え方について解説します。
TPMとは「全員参加の生産保全」
TPM(Total Productive Maintenance)とは、生産現場全体で協力して生産保全を行う考え方のことです。国内で発表されている書籍などでは、「全員参加の生産保全」と訳されるのが一般的です。
現場の全員が保全に参画し、計画に沿ったメンテナンスを実施することで、効率よく高品質な製品を生産することを目的に行われています。TPMはロスをゼロに近づけるためのアプローチ方法として、「人」や「設備」を中心に据えている点が特徴的です。人の行動や現場の設備を変革することで、現場のロスを抑えて、生産性を高める考え方を採用しています。
TPMの考え方は40年以上に渡って生産現場で用いられており、今でも時代の流れを汲みながら発展を続けています。
▼ 設備保全に関する最新のデジタルトレンドをまとめた資料(全50ページ)
『Industry4.0 時代のデジタル業務改革』はこちらからダウンロードできます。
TPMで定義されている16大ロス
TPMで定義されているロスには、「設備の効率化を阻害する8大ロス」「人の効率化を阻害する5大ロス」「原単位の効率化を阻害する3大ロス」の合計16種類があります。以下、各ロスの定義を解説します。
設備の効率化を阻害する8大ロス
設備の効率化を阻害する8大ロスは、次のように定義されています。
- 故障ロス
- 段取り・調整ロス
- 刃具交換ロス
- 立上がりロス
- チョコ停・空転ロス
- 速度低下ロス
- 手直し・不良ロス
- シャットダウン(SD)ロス
故障ロスとは、恒常的あるいは突発的に発生する、故障によって生じるロスのことです。機械の停止や機能低下を生じるもの、修理に5~10分以上の時間がかかるもの、機能を回復させるために修理が必要なものなどが挙げられます。
段取り・調整ロスは、ある製品の製造が終了して、次の製造に移り、新たな製品が完成するまでに生じる時間的なロスを指します。治工具の取り外しや掃除・片付け、試加工や調整、測定などのプロセスがあり、段取りの時間を短縮するほど、ロスの発生を抑えられます。
刃具交換ロスは、製造に使用する刃具のメンテナンスや交換によって、一時的に発生する時間的、または物量ロスです。刃具そのものや刃物ホルダーの精度が悪いと、ロスが拡大することもあります。
立上がりロスは、機械に特別なトラブルが起こっていない状態で、休憩明けの再稼働時などに安定的な品質で生産できるようになるまでに生じるロスを指します。多くの立上がりロスは、設備の熱膨張によって起こります。
チョコ停、空転ロスは、回復までにかかる時間が5分未満の一時的な停止や、部品交換を必要としない停止などによるロスのことです。1回あたりのロスは小さいものの、積み重なると大きなロスにつながります。
速度低下ロスは、設備の動作速度が遅いために、製造に時間的なロスが生じている状態を表します。本来の技術水準よりもスピードが著しく遅い場合は、設備を刷新することも選択肢のひとつです。
手直し・不良ロスは、不良品を良品に修正するために生じる時間的・物量ロスです。慢性的にロスが生じる場合は、改善策を講じる必要があります。
シャットダウン(SD)ロスは、計画休止にともない発生するロスのことです。計画的な設備保全を行うために設備を停止する時間的ロスと、その立上がりのために発生する物量ロスがあります。
人の効率化を阻害する5大ロス
人の効率化を阻害するロスには、次の5つが定義されています。
- 管理ロス
- 動作ロス
- 編成ロス
- 自動化置き換えロス
- 測定調整ロス
管理ロスは、原料調達を待つ時間や、故障修理にかかる時間などによって生まれるロスのことです。待機時間をほかの作業で埋めるなど、上手くスケジュールを調整することでロスの拡大を防止できます。
動作ロスは、現場の担当者が作業を行う際に、動作に無駄が生じることで積み重なるロスを指します。現場の設備レイアウトが原因で起こる歩行ロスも、動作ロスに含まれます。最小の動作で最大のパフォーマンスを出せる導線づくりが重要です。
編成ロスは、ライン設計における手待ちロスやコンベヤ作業のバランスロスのことです。複数の製造を掛け持ちしている場合に起こる、ベルトコンベアのラインバランス崩れなどが原因になります。
自動化置き換えロスは、自動化することで省力化が図れる状況であるにもかかわらず、人の手で処理を続けているために生じるロスのことです。製造そのものだけでなく、部品の供給や運搬など、物流のロスも自動化置き換えロスに含みます。
測定調整ロスは、品質不良や流出を起こさないために実施する、測定・調整にかかる時間的ロスのことです。不良品の発生が多いと短縮が難しいロスなので、製造品質の向上が根本的な改善策になります。
原単位の効率化を阻害する3大ロス
原単位とは物の生産に必要な時間やエネルギー、モノの量のことです。原単位の効率化を阻害する3大ロスは、次のとおりです。
- 歩留まりロス
- エネルギーロス
- 型・治工具ロス
歩留まりとは、製造のために投入した原料や素材の総量に対する、得られた出来高の割合のことです。歩留まりロスは、歩留まりが本来期待される水準よりも低かった場合に生じるロスを表します。可能な限り歩留まりを高めるための施策を講じることが重要です。
エネルギーロスは、製品を製造するために使われる水や燃料、電力などのエネルギーに関するロスです。必要以上のエネルギーを使用していないかどうかを振り返り、最適化を図ることで、ロスの発生を抑えられます。
型・治工具ロスは、製品を製造するために不可欠な、型や治工具を製作・補修するための金銭的ロスを指します。型や治工具は経年劣化によっていずれ交換が必要になりますが、消耗や破損を最小限に抑えて、交換のサイクルを延ばすことでロスを小さくできます。
ロスを防ぐ「TPMの8本柱」とは
製造現場で生じるロスを防ぐためには、「TPMの8本柱」と呼ばれる8つの項目を意識した改善が求められます。8つの項目が適用される対象は、製造現場だけでなく、経営層や保守部門、管理・間接部門にまで及びます。
ここでは、それぞれの柱の内容を詳しく解説します。
生産システムの個別改善
生産システムの個別改善では、設備単位のロスや、生産ラインの各プロセスで発生しているロスを個別に調査し、判明したロスをひとつずつなくしていきます。
製品が完成するまでには、原料調達から製造まで、さまざまなプロセスが介在しています。これらのプロセスをひとつずつ最適化できれば、全体の生産が効率化され、ロスを削減して高品質な製品を短期間で製造することが可能です。
日頃当たり前のように運用しているプロセスであっても、人の手で行う作業のロスと、設備によるロスが積み重なることで、気がつかないうちに多大なロスが発生している場合があります。個別のプロセスをあらためて調査することは、現場のロスの全容を意識するきっかけにもなるでしょう。
オペレーターの自主保全
オペレーターの自主保全とは、現場で作業を行うオペレーター自身が、担当する製造現場や設備を自主的に保全する活動のことです。稼働前に設備を点検して不具合がないか確かめたり、交換や修理が必要な部品がないかどうかを調べたりすることで、設備によるロスを最小限に抑えられます。
現場のオペレーターがそれぞれ自主保全を意識することで、工場全体の生産性アップにつながります。また、オペレーター以外の現場担当者であっても、自分が担当する現場の設備や環境をこまめにチェックして、自主保全活動を行うことは重要です。
作業の無駄をできるだけ省き、無理な運用をせず、ムラをなくすためには、現場の全員が自らの担当する業務に責任を持ち、保全に取り組む必要があります。
保守部門の計画保全
保守部門の計画保全とは、設備の故障を減らしたり、寿命を延ばしたりすることを目的として、保守部門が行う活動のことです。設備が故障したときに速やかに機能を回復させるための予備部品をストックしたり、定期的なメンテナンスを行って故障の発生を未然に防いだりする施策が考えられます。
また、定期的なメンテナンスによる予防保全だけでなく、設備の劣化状況を診断して修理や交換の予兆を見つける予知保全体制の確立なども行います。
予知保全の体制を整えられれば、最適なタイミングで修理・交換を行えるため、保守費用を最適化できるメリットもあります。近年では、予知保全にAI技術が活用される例も増えてきています。
ロスを最小限にする初期管理
製品や設備の開発段階から、生産時に想定されるロスを考慮する「初期管理」も重要です。ロスが生じにくい製品開発や設計を行うことで生産時のロスを防ぎ、ロスが発生したとしても最小限に留めることが可能になります。
また、さまざまな改善情報を収集し、開発現場にフィードバックしてよりロスの少ない設備にアップデートする取り組みも効果を発揮します。設備を導入した後は、漫然と稼働させるのではなく、定期的に現場担当者からヒアリングを行って、設備の改善点がないかどうかを確認すると良いでしょう。
品質保全体制の確立
品質保全体制の確立とは、不良品や消費者からのクレームによって生じるロスを防止する活動を指します。
適切な製造プロセスを構築できていないと、製造途中で不良品が発生して修正や除外のために時間的ロスが発生したり、誤って消費者に届いてしまい、クレームに発展したりするリスクは高まります。不良品が発生しない条件を見極めて、最適な条件が見つかった後は、その条件を維持し続けられる体制づくりを行うことが重要です。
検査体制の強化は、不良品を流通させないという観点では効果的ですが、不良品の発生そのものを防ぐ効果はありません。そのため、製造プロセスを最適化したり、設備の設定を見直したりして、「不良品ゼロの現場」を目指すことが求められます。
教育・訓練の最適化
教育・訓練の最適化とは、業務を進めるうえで必要な知識・スキルを身につけるために、必要な知識を整理して、教育と訓練を最適化する活動のことです。
製造を効率化するためには、現場担当者の知識やスキルを最大限に活用して、システムや設備の力を最大限に引き出す必要があります。日頃からスキルアップの機会を設けて、業務に不可欠な知識を身につけられれば、ロスの抑制につながります。
管理・間接部門の保全活動
管理・間接部門の保全活動とは、生産現場で生じるロスを削減するために、管理部門や間接部門が現場を支援する活動全般を指します。現場担当者が個々のムダを意識して活動することもロス削減のためには重要ですが、管理・間接部門においても、保全活動を積極的に行うことが求められます。
例えば事務所の「5S」の推進は、管理・間接部門の保全活動の一種です。ほかにも、事務作業の効率化や物流在庫のロス削減、営業の売上拡大などを通じて全社のロス削減に努めます。
安全・衛生管理の確立
安全・衛生管理の確立は、災害や事故が起こらないように徹底し、ゴミの排出を削減したり、省エネに取り組んだりする活動のことです。
製造現場で災害や事故が起こると、大幅な時間的ロスが発生するだけでなく、場合によっては人的損失が生じるおそれもあります。現場で働く従業員の安全を確保する意味でも、安全・衛生管理を確立することは重要です。
また、環境へ配慮した経営は、近年、国際的に重視されている項目でもあります。SDGs(持続可能な開発目標)を意識した経営は、ロスの削減だけでなく、対外的に環境に配慮できる企業であることをアピールするチャンスにもなります。
TPMが注目されている理由
TPMの考え方が登場してから40年以上が経ちますが、今、再び多くの企業から注目を集めています。ここでは、TPMが再び注目されるようになった理由を、3つの観点から解説します。
市場の競争激化
近年ではグローバル化が進み、企業は世界中の同業他社と市場のシェアを争わなければならない状況に置かれています。次々と変革していく技術を取り入れながら競争力を高めていかなければ、市場の中で置き去りになり、競争力を失ってシェアを落としてしまう可能性があるでしょう。
市場における競争力を強化するには、「ロスをゼロに近づける施策」が重要になります。どれだけロスをゼロに近づけて強靭な企業体質を確立させられるかが、激化する競争社会の中で生き残り続けるポイントです。
また、時間的ロスを削減して開発・生産を高速化できれば、市場の変化にいち早く対応可能な体制が整い、新たなビジネスを獲得できるチャンスが広がります。
設備の高度化・高経年化
デジタル技術は日に日に進歩を続けており、工場の設備機能も多様化しています。このような環境において、豊富な分析手法をそろえているTPMは、高度化した設備を詳細に分析し、生産とコストの最適化を実現する方法として有効です。
また、長年に渡って設備を使い続けていくと、高経年化によって設備にトラブルが起こる可能性も高まるため、TPMの考え方を取り入れた保全活動の実施が効果を発揮します。TPMは経営層と現場の双方で管理・活動指標を擦り合わせるため、全社が一丸となって取り組みやすい手法でもあります。
サステナビリティへの注目
企業のサステナビリティ(持続可能な)経営に注目が集まっている近年において、安全や環境保全を重視するTPMの考え方は好相性です。
今や、企業に対して求められるのは「品質の高い製品を作ること」だけではなくなっています。サステナビリティ経営を行っており、環境に配慮した経営が行われているかどうかも、購入判断のひとつに加える消費者が増えています。
また、ワークライフバランスや働き方改革が注目されるに伴って、「人を大切にする経営」も重要な要素となりました。適切な労働時間を守り、人を尊重している企業から製品を購入したいと考える消費者に応えるためには、TPMの考え方を取り入れることが有効です。
TPMの実現にはテクノロジーが不可欠
TPMをはじめとした保全活動を高いレベルで実現するためには、IoTやAIなど、最新のデジタル技術の導入が必要不可欠です。IoTを用いて現場データを収集、蓄積、可視化し、最適なタイミングでデータの利活用を行える環境を整備することが、TPMの成功につながります。
ロスの予兆を察知する「予知保全」の実現には、IoTとAIの連携が求められます。AIがさまざまなデータを解析して、ロスの発生をいち早く察知することで、時間的ロスを削減して工場の稼働を効率化させることが可能です。
また、経営層から現場担当者まで、全ての関係者が一丸となって保全活動に取り組むTPMにおいては、包括的なソリューションを導入する必要があります。保全管理システムの導入なども検討して、全社が協力してTPMに取り組める体制を整えましょう。
▼実際に、最新の設備保全・キャリブレーション管理システムを導入し、「止まらない工場」と「生産性向上」を実現した企業の事例をご紹介します。
導入事例:住友ファーマ株式会社はこちらからダウンロードできます。
まとめ
TPMは環境や人への配慮が求められる現代の経営と相性が良いため再び注目を集めています。16大ロスの抑制により強靭な企業体質を醸成できます。
TPMの推進には「Maximo」の導入がおすすめです。設備管理領域をデジタル化し、現場の状況把握や予防保全、業務改善を支援してロスの削減に貢献します。
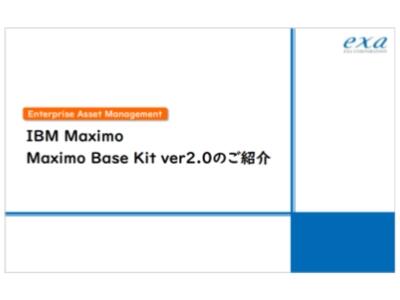
IBM Maximo/Maximo Base Kit 紹介資料
IBM Maximoの概要からMaximo Base Kitのカバー範囲、Maximoを活用した設備管理・作業管理のPDCAイメージと実際の画面を用いた各主要機能の詳細な説明
※「Maximo Base Kit」はIBM Maximoをベースとした短期導入ソリューションです
関連する記事
関連ソリューション
関連事例
お問い合わせ
CONTACT
Webからのお問い合わせ
エクサの最新情報と
セミナー案内を
お届けします
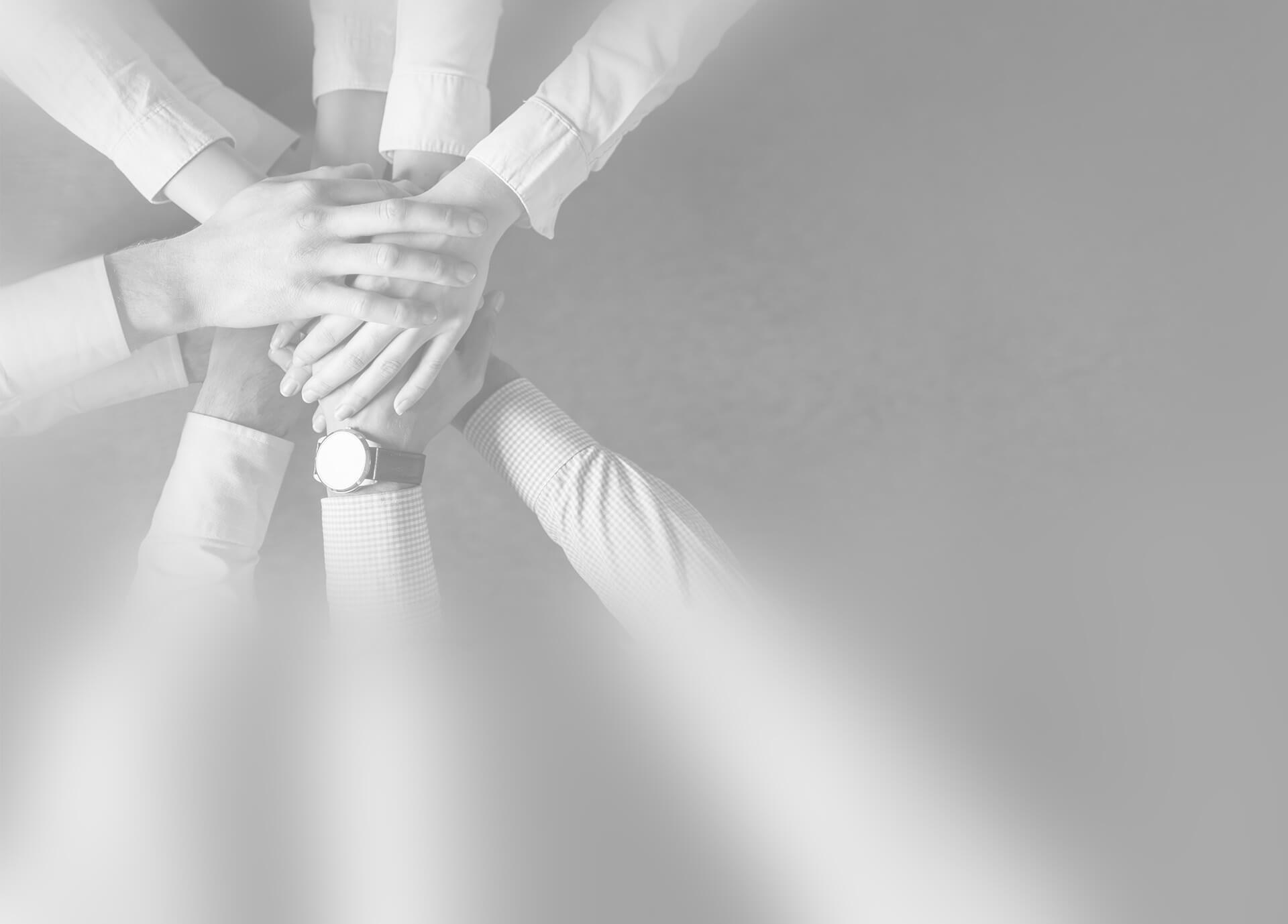