デジタル化の進展や技術進歩を背景に、製造業ではものづくりのスマート化(スマートファクトリー)が求められています。しかし、ものづくりのスマート化をどのように行えば良いか把握できていない方もいるのではないでしょうか。本記事では、経済産業省が公表している「スマートファクトリーロードマップ」をもとに、ものづくりのスマート化の目的やレベルに応じたロードマップをご紹介します。
製造業でものづくりのスマート化が必要な背景
デジタル化の進展(IoT・ビッグデータなど)、⼈⼯知能(AI)、⽣産技術(3Dプリンタなど)、ロボットなどの技術⾰新、資源の制約、消費者ニーズの変化など、ものづくりを取り巻く外部環境は今後⼤きく変化することが予想されます。
こうした中で企業がグローバル競争⼒を維持・強化するためには、IoTを活用した生産プロセスの革新、製品の高付加価値化、サービスを取り込んだ新たなビジネスモデルの創出に取り組むなど、IoTやロボットを活用した「ものづくりのスマート化」が不可欠です。
また、付加価値が「もの」そのものから、「サービス」「ソリーション」へと移る現在、付加価値の創造・最大化や、現場力の向上を後押しするためにも「ものづくりのスマート化」が求められています。
ものづくりのスマート化とは
「ものづくりのスマート化」とは、IoT・ビッグデータ・AI・ロボットを活用し、エンジニアリングチェーンやサプライチェーンをネットワーク化・最適化・自動化することです。
これにより、ニーズに即した短期間での製品設計や、個別のニーズや需要変動に対して柔軟性・即応性を有した生産、製品に付随したサービス提供による新たな付加価値の創出などを実現します。
ものづくりのスマート化を実現する要素・技術
ものづくりのスマート化を実現する要素・技術としては、主に以下のものがあります。
IoT
IoTは"Internet of Things"の略であり、「モノのインターネット」と訳されます。製造現場におけるデバイスや機器にセンサを組み込むことでインターネットへの接続機能や通信機能を持たせ、リアルタイムでデータを収集し、遠隔からモニタリングや制御、計測等を行うことが可能になります。
AIによるビッグデータ分析
デジタル技術が進展したことで、業務に関連するあらゆる情報を収集できるようになりました。人間では収集・把握・分析が難しい多様で膨大なデータ郡のことをビッグデータと呼びますが、AIを活用することであらゆるビッグデータを収集・分析できようになり、製造プロセスの最適化や異常検知、予防保全などに活用されています。
自動化とロボティクス
生産プロセスの自動化も、ものづくりのスマート化には欠かせない要素です。例えばロボットを導入することで、これまで人が行っていた工程を自動化できるため、省力化・省人化に寄与します。これにより製造業の現場で深刻な課題となっている人手不足の緩和が期待できます。また、自動化を通じて作業の精度や速度を向上させることが可能であるほか、危険を伴う作業をロボットに任せることで安全性を高めることも可能です。
デジタルツイン
デジタルツインとは、物理空間(現実世界)における製品や製造現場の情報、オペレーションに関するデータなどをIoTやAIを通じて収集し、サイバー空間(仮想世界)で再現する技術のことです。物理空間と全く同じ状態をサイバー空間に構築し、リアルタイムに同期することで、現実世界で製品や設備に手を加えることなく製造のシミュレーションなどを行うことができます。これにより、製品の設計や製造プロセスの最適化を支援します。
ものづくりのスマート化によるメリット
ものづくりのスマート化によって、製造現場では以下のようなメリットを得ることができます。
生産性の向上
IoTやAI、ロボットなどの導入により自動化を推進することで、生産ラインをよりスムーズに稼働できるようになり、これまでと同じ時間でより多くの生産量を実現できます。また、省力化を進め人件費を抑制することでも生産性向上に寄与します。
品質の向上
データ分析や異常検知によって、人による目視だけでは見落とす可能性のある製品の欠陥や不良品を早期かつ確実に発見できるようになり、品質管理のレベルが向上します。また、自動化を進めることで属人的な要素が減り、作業の標準化が進むため、この点でも品質向上を期待できます。
コスト削減
ものづくりのスマート化により省力化・省人化が進むことで人件費を抑制できるほか、不良品の減少を通じて生産におけるロスが少なくなり、トータルでの生産コスト低減につながります。
新たな設備やソリューションの導入には初期投資コストがかかりますが、中長期的なコスト削減効果や生産性向上を考えれば、費用対効果は決して小さくありません。
柔軟性の向上
日々刻々と変わる市場環境や需要の変動を踏まえ、ニーズに応じた生産計画や設計・開発などの調整が容易になります。特に、AIやビッグデータを用いたデータ分析を通じてより正確な需要予測ができるようになり、柔軟かつ無駄のない生産を実現できます。
イノベーションの促進
ものづくりのスマート化においては、IoTやAIを通じて生産データや顧客からのフィードバックなどを、製品や製造プロセスの分析に活用することができます。こうしたデータドリブン型のアプローチにより、製品の改良や新製品の開発などに関してより客観的な意思決定が可能となり、イノベーションを促進します。
また、前述のように生産性向上や品質の向上、コスト削減を通じて競争力が高まり、そこで得た利益を投資に活用できるため、さらにイノベーションを促進する効果があります。
ものづくりのスマート化を進めるためのロードマップの定義
企業では、ものづくりのスマート化への対応が必要と認識しつつも、スマート化に向けた戦略⽴案を⾃ら進めることができていない課題があります。これは、どのようにスマート化を進めていけば良いか明確になっていないことが要因です。
スマート化を促進するには、スマート化の⽅向性・レベルを示すことが必要です。そこで、ロボットを活⽤したものづくりのスマート化の⽅向性・レベルを示したロードマップを定義し、スマート化の各レベルに到達するために克服が必要な課題や成功のポイントを整理することが重要となります。
ロードマップは目的、範囲、レベルによって異なる
ロードマップの内容は目的、範囲、レベルによって異なります。たとえば目的としては、品質の向上、コスト削減、生産性の向上などがあります。範囲としては、生産性の向上が目的なら、①設備・ヒトの稼働率の向上、②ヒトの作業の効率化、作業の削減・負担軽減、③設備の故障に伴う稼動停⽌の削減などの範囲が挙げられます。
またレベルとしては、レベル①:データの収集・蓄積、レベル②:データによる分析・予測、レベル③:データによる制御・最適化というように、データ活用の水準によって分けられます。
ロードマップの具体例
以下では、経済産業省が公表している「スマートファクトリーロードマップ」をもとに、スマート化の目的とレベルごとに達成したい内容の具体例を抜粋してご紹介します。
(1)「品質の向上」に向けたロードマップの一例
「品質の向上」に向けたロードマップの例として、以下では①不良率の低減、②品質の安定化・ばらつきの低減(加⼯誤差の最小化、加工性能の最大化)、③設計品質の向上の3つをご紹介します。
スマート化の目的①:不良率の低減
主な対象企業層 | 素形材加工企業、設備・金型供給企業、組み立て企業 |
主な対象プロセス | 生産 |
レベル1 (データの収集・蓄積) |
ヒトの作業内容(作業手順、作業結果など)をセンシングすることで、作業内容を収集・把握。ポカミスが発生した際、ヒトへ早期に通知できる。 |
レベル2 (データによる分析・予測) |
過去のポカミスを分析することで、ポカミスが発生しやすい作業工程を特定できる。 |
レベル3 (データによる制御・最適化) |
分析結果に基づいて、従業員を人材育成したり、設計を変更したりすることで、ポカミスの発生を抑制し、不良率を削減・最小化できる。 |
スマート化の目的②:品質の安定化・ばらつきの低減(加工誤差の最小化、加工性能の最大化)
主な対象企業層 | 素形材加工企業、設備・金型供給企業、組み立て企業 |
主な対象プロセス | 生産 |
レベル1 (データの収集・蓄積) |
設備にセンサを取り付けて搭載してモニタリングすることで、加工寸法などの製品の品質データと設備の加工条件・設定値を収集・把握できる。 |
レベル2 (データによる分析・予測) |
収集したデータを分析し、品質のばらつきの要因を特定することで、加工誤差や加工性能の改善につながる加工条件・設定値をモデル化できる。 |
レベル3 (データによる制御・最適化) |
構築した加工改善モデルを用いて、設備の加工条件・設定値を最適化することで、加工誤差を最小化したり、加工性能を最大化できる。 |
スマート化の目的③:設計品質の向上
主な対象企業層 | 設備・金型供給企業、組み立て企業 |
主な対象プロセス | 製品企画、開発・設計、製品稼働、サービス提供 |
レベル1 (データの収集・蓄積) |
製品にセンサ・通信機能を搭載することで、製品の使用状況や使用環境のデータを収集・把握できる。 |
レベル2 (データによる分析・予測) |
収集したデータと設計データとを関連付けて因果関係を明らかにすることで、品質・信頼性の向上につながる設計仕様・生産方法を分析できる。 |
レベル3 (データによる制御・最適化) |
分析結果に基づいて、設計仕様・生産方法を修正・改善して最適化することで、製品の品質・信頼性を向上できる。 |
(2)「コストの削減」に向けたロードマップの一例
「コストの削減」に向けたロードマップの例として、以下では①材料の使用量の削減、②生産のためのリソーセスの削減、③在庫の削減、④設備の管理・状況把握の省力化の4つをご紹介します。
スマート化の目的①:材料の使用量の削減
主な対象企業層 | 素形材加工企業、設備・金型供給企業、組み立て企業 |
主な対象プロセス | 製品企画、開発・設計 |
レベル1 (データの収集・蓄積) |
設計事例を収集してデータベースとして蓄積することで、過去の事例を容易に参照できる。 解析・シミュレーションソフトウェアを利用することで、構造等を解析できる。 |
レベル2 (データによる分析・予測) |
過去の設計事例の分析や、解析・シミュレーションソフトウェアなどによって、材料の軽量化や部品点数の削減につながる形状・構造等を知見としてモデル化できる。 |
レベル3 (データによる制御・最適化) |
構築した設計改善モデルを用いて、製品設計を最適化することで、材料の使用量を最小化できる。 |
スマート化の目的②:生産のためのリソースの削減
主な対象企業層 | 素形材加工企業、設備・金型供給企業、組み立て企業 |
主な対象プロセス | 生産 |
レベル1 (データの収集・蓄積) |
MES(製造実行システム)などの生産管理システムのデータを利用することで、生産の作業プロセスの進捗状況や、ヒト(工数)、材料、エネルギーの投入状況を収集・把握できる。 |
レベル2 (データによる分析・予測) |
生産の作業プロセスの進捗状況を踏まえて、ヒト(工数)、材料、エネルギーの予定投入量、予定生産量などを予測できる。 |
レベル3 (データによる制御・最適化) |
設備の稼動計画、ヒトの作業計画を修正・最適化することで、投入するヒト(工数)、材料、エネルギーを最小化できる。 |
スマート化の目的③:在庫の削減
主な対象企業層 | 素形材加工企業、設備・金型供給企業、組み立て企業 |
主な対象プロセス | 受注・調達、生産、物流・販売 |
レベル1 (データの収集・蓄積) |
MES(製造実行システム)などの生産管理システムのデータを利用することで、生産計画や生産実績データの入力・表示・確認が容易にできる。 |
レベル2 (データによる分析・予測) |
受注、生産、出荷の計画・実績データを連動させて分析することで、需給変動要因を明らかにしたり、需給を予測したりできる。 |
レベル3 (データによる制御・最適化) |
需給予測に基づいて、調達した資材や生産した製品の在庫が最小化となるよう、生産計画・出荷計画の作成を自動化・最適化できる。 |
スマート化の目的④:設備の管理・状況把握の省力化
主な対象企業層 | 素形材加工企業、設備・金型供給企業、組み立て企業 |
主な対象プロセス | 生産 |
レベル1 (データの収集・蓄積) |
設備にセンサを取り付けてモニタリングすることで、設備の設置場所にいなくても、複数の設備の稼働状況を、遠隔でリアルタイムに収集・監視できる。 |
レベル2 (データによる分析・予測) |
該当なし。 |
レベル3 (データによる制御・最適化) |
設備に異常などが発生したときに、従業員への通知を自動化することで、監視・点検の管理工数を最小化できる。 |
(3)「生産性の向上」に向けたロードマップの一例
「生産性の向上」に向けたロードマップの例として、以下では①設備・ヒトの稼働率の向上、②ヒトの作業の効率化、作業の削減・負担軽減(ヒトの作業プロセスの最適化)、③設備の故障に伴う稼動停止の削減(故障の発生頻度の最小化)の3つをご紹介します。
スマート化の目的①:設備・ヒトの稼働率の向上
主な対象企業層 | 素形材加工企業、設備・金型供給企業、組み立て企業 |
主な対象プロセス | 生産 |
レベル1 (データの収集・蓄積) |
MES(製造実行システム)などの生産管理システムのデータを利用することで、生産ライン全体の設備の稼働・ヒトの作業の進捗状況を収集・把握できる。 |
レベル2 (データによる分析・予測) |
設備の稼働・ヒトの作業の進捗状況を基に、各プロセスの完了予定時間を予測できる。設備とヒトの非稼動時間が発生する要因を分析できる。 |
レベル3 (データによる制御・最適化) |
生産ライン全体の生産完了予定時間が最短化されるよう、設備の稼動計画、段取り替え計画、ヒトの作業計画を修正・最適化することで、設備・ヒトの非稼動時間を最小化できる。 |
スマート化の目的②:ヒトの作業の効率化、作業の削減・負担軽減(ヒトの作業プロセスの最適化)
主な対象企業層 | 素形材加工企業、設備・金型供給企業、組み立て企業 |
主な対象プロセス | 受注・調達、生産、物流・販売 |
レベル1 (データの収集・蓄積) |
HMI(モバイル端末、スマートグラスなど)・RFIDなどを活用することで、調達した資材や生産した製品の管理情報、生産情報、設備の稼動情報を迅速かつ簡易に入力・表示できる。 |
レベル2 (データによる分析・予測) |
作業の進捗状況に応じて、HMIに必要な情報や作業指示を予測して表示できる。 |
レベル3 (データによる制御・最適化) |
情報の入力・表示の自動化による作業の短時間化や、適切な判断を支援する情報を提示することで、作業プロセスを最適化できる。 |
スマート化の目的③:設備の故障に伴う稼動停止の削減(故障の発生頻度の最小化)
主な対象企業層 | 素形材加工企業、設備・金型供給企業、組み立て企業 |
主な対象プロセス | 生産 |
レベル1 (データの収集・蓄積) |
設備にセンサを取り付けてモニタリングすることで、設備の稼働状況を収集・監視できる。 |
レベル2 (データによる分析・予測) |
収集したデータと設備異常とを関連付けて、設備の故障につながる兆候・条件を明らかにすることで、故障の発生時期を予測できる。 |
レベル3 (データによる制御・最適化) |
設備の故障予測に基づき、予防保全することで、故障の発生を抑制し、想定外の稼動停止時間を削減・最小化できる。 |
(4)「製品化・量産化の期間短縮」に向けたロードマップの一例
「製品化・量産化の期間短縮」に向けたロードマップの例として、以下では①製品の開発・設計の自動化、②仕様変更への対応の迅速化、③生産ラインの設計・構築の短縮化の3つをご紹介します。
スマート化の目的①:製品の開発・設計の自動化
主な対象企業層 | 素形材加工企業、設備・金型供給企業、組み立て企業 |
主な対象プロセス | 製品企画、開発・設計 |
レベル1 (データの収集・蓄積) |
設計事例を収集してデータベースとして蓄積することで、過去の事例を容易に参照できる。 解析・シミュレーションソフトウェアを利用することで、構造等を解析できる。 |
レベル2 (データによる分析・予測) |
過去の設計事例や、解析・シミュレーションソフトウェアなどによって分析することで、設計仕様を満たし、かつ、生産しやすい形状・構造等を知見としてモデル化できる。 |
レベル3 (データによる制御・最適化) |
構築した設計改善モデルを用いて、製品設計を自動化することで、製品開発・設計期間を短縮できる。 |
スマート化の目的②:仕様変更への対応の迅速化
主な対象企業層 | 素形材加工企業、設備・金型供給企業、組み立て企業 |
主な対象プロセス | 製品企画、開発・設計、生産 |
レベル1 (データの収集・蓄積) |
E-BOM(設計部品表)やM-BOM(製造部品表)などを利用することで、部品の詳細情報を容易に表示・確認できる。 |
レベル2 (データによる分析・予測) |
E-BOMやM-BOMなどをデータ連携することで、開発、設計、生産のデータを一元的に管理できる。 仕様変更となった場合、影響範囲と影響度を分析できる。 |
レベル3 (データによる制御・最適化) |
仕様変更となった場合、統合BOMを通じて、開発、設計、生産工程のデータを連動させて反映することで、仕様変更の対応時間を最小化できる。 |
スマート化の目的③:生産ラインの設計・構築の短縮化
主な対象企業層 | 素形材加工企業、設備・金型供給企業、組み立て企業 |
主な対象プロセス | 生産 |
レベル1 (データの収集・蓄積) |
生産ラインシミュレータなどを利用することで、サイバー上で生産ラインを設計できる。 |
レベル2 (データによる分析・予測) |
生産ラインシミュレータなどを利用することで、生産ラインのレイアウト、生産能力、作業工程、搬送ルート、投資コストなどを事前に評価・検証できる。 |
レベル3 (データによる制御・最適化) |
サイバー上で生産ラインを設計し最適化した上で、実世界の生産現場へ実装することで、構築時の試行錯誤を削減し生産ライン構築期間を短縮できる。 |
(5)「人材不足・育成への対応」に向けたロードマップの一例
「人材不足・育成への対応」に向けたロードマップの例として、以下では①多様な人材の活用、②技能の継承の2つをご紹介します。
スマート化の目的①:多様な人材の活用
主な対象企業層 | 素形材加工企業、設備・金型供給企業、組み立て企業 |
主な対象プロセス | 生産 |
レベル1 (データの収集・蓄積) |
各従業員の作業熟練度、知識、身体能力、使用言語などを、データベースとして蓄積することで、各従業員の特性情報を利用できる。 |
レベル2 (データによる分析・予測) |
該当なし。 |
レベル3 (データによる制御・最適化) |
HMD(ヘッドマウントディスプレイ)や音声認識機器などのウェアラブルデバイス、パワーアシストスーツ、生体センサなどを活用し、ヒトの能力を拡大することで、特性が異なる多様な人材を活用できる。 |
スマート化の目的②:技能の継承
主な対象企業層 | 素形材加工企業、設備・金型供給企業、組み立て企業 |
主な対象プロセス | 生産 |
レベル1 (データの収集・蓄積) |
熟練技能者の技能(段取り調整力、状況判断力、手わざ、トラブル対応力など)をセンシングすることで、データベースとして蓄積できる。 |
レベル2 (データによる分析・予測) |
収集したデータを分析し、その他の作業者と比べて熟練技能者が優れている点を明らかにすることで、技能・ノウハウ・知見を体系化できる。 |
レベル3 (データによる制御・最適化) |
体系化した技能・ノウハウ・知見を国内外の拠点へ共有することで、それらを継承し、ヒトの能力を向上できる。それらをスマートロボットに学習させることで、ヒトを代替できる。 |
(6)「新たな付加価値の提供・提供価値の向上」に向けたロードマップの一例
「新たな付加価値の提供・提供価値の向上」に向けたロードマップの例として、以下では①多用なニーズへの対応力の向上(個別ニーズにあわせた多品種の製品の提供)、②提供可能な加工技術の拡大、③新たな製品・サービスの提供(新たな製品を先回りした企画・提案)、④製品の性能・機能の向上(製品性能の最大化・カスタマイズ化)の4つをご紹介します。
スマート化の目的①:多用なニーズへの対応力の向上(個別ニーズにあわせた多品種の製品の提供)
主な対象企業層 | 組み立て企業 |
主な対象プロセス | 受注・調達、生産 |
レベル1 (データの収集・蓄積) |
各製品に共通する部分を定義して、製品の構造、設計・生産プロセス、加工基準などを共通化することで、共通モジュールと個別モジュールの組み合わせによるフレキシブルな生産体制を構築できる。 |
レベル2 (データによる分析・予測) |
調達・生産・販売などの社内関係部門間でデータ連携することで、調達計画・生産計画・物流計画などを情報共有できる。 |
レベル3 (データによる制御・最適化) |
設備・ヒトへの作業指示・部品供給や段取り替えの計画策定を自動化・最適化することで、個別のニーズにあわせて多品種の製品をフレキシブルに生産できる。 |
スマート化の目的②:提供可能な加工技術の拡大
主な対象企業層 | 素形材加工企業 |
主な対象プロセス | 受注・調達、生産 |
レベル1 (データの収集・蓄積) |
MES(製造実行システム)などの生産管理システムのデータを利用することで、生産の進捗状況を収集・把握できる。 |
レベル2 (データによる分析・予測) |
共同受注を行う企業間でデータ連携することで、生産計画・進捗状況などを情報共有できる。 |
レベル3 (データによる制御・最適化) |
各企業における加工時間・加工ロット単位などの違いを考慮して、全体で、生産計画・物流計画などを最適化することで、共同受注生産体制を構築し、様々な加工技術を提供できる。 |
スマート化の目的③:新たな製品・サービスの提供(新たな製品を先回りした企画・提案)
主な対象企業層 | 設備・金型供給企業、組み立て企業 |
主な対象プロセス | 製品企画、開発・設計、製品稼働、サービス提供 |
レベル1 (データの収集・蓄積) |
製品にセンサ・通信機能を搭載することで、製品の使用状況や使用環境のデータを収集・把握できる。 |
レベル2 (データによる分析・予測) |
収集したデータを分析し、ユーザを⾏動観察する(⼈間⼯学、⼼理学などの観点から分析する)ことで、⾮顕在ニーズを把握できる。 |
レベル3 (データによる制御・最適化) |
把握したニーズを実現する製品・機能・サービスを先回りして企画・提案できる。 |
スマート化の目的④:製品の性能・機能の向上(製品性能の最⼤化・カスタマイズ化)
主な対象企業層 | 設備・金型供給企業、組み立て企業 |
主な対象プロセス | 製品稼働、サービス提供 |
レベル1 (データの収集・蓄積) |
製品に組み込まれたセンサなどを利⽤したり、製品にセンサ・通信機能を搭載したりすることで、製品の使⽤状況、使⽤環境のデータ、製品の制御データを収集・把握できる。 |
レベル2 (データによる分析・予測) |
収集したデータを分析することで、ユーザにおける製品の使⽤⽅法の傾向を把握できる。 |
レベル3 (データによる制御・最適化) |
ユーザにおける製品の使⽤⽅法の傾向にあわせて、製品の制御設定値を最適化することで、製品の性能を最⼤化・カスタマイズ化できる。 |
(7)「その他(リスク管理の強化)」に向けたロードマップの一例
「その他」のロードマップとしては、リスク管理の強化が挙げられます。
スマート化の目的:リスク管理の強化
主な対象企業層 | 素形材加工企業、設備・金型供給企業、組み立て企業 |
主な対象プロセス | 製品稼働、サービス提供 |
レベル1 (データの収集・蓄積) |
製品にRFIDや通信機能を搭載し、加工・組立・検査・出荷のデータを蓄積することで、製品個体毎の品質を証明できる。 |
レベル2 (データによる分析・予測) |
製品に不具合が発生したときに、製品や資材に蓄積されたデータを分析することで、不具合の原因の特定を早期化できる。 |
レベル3 (データによる制御・最適化) |
製品に不具合が発生したときに、通信機能を通じて、製品を使⽤しているユーザを把握し、対策を講ずることで、影響範囲を最小化できる。 |
まとめ
AIやIoT等のデジタル技術の進展や市場の変化などを背景に、ものづくりのスマート化が注目されています。ものづくりのスマート化は生産性や品質の向上、イノベーションの促進などのメリットがあり、国際的な競争が激しくなっている現在、導入・推進することが不可欠となっています。
ものづくりのスマート化を進める際には、目的やレベル、業務範囲に応じてロードマップを定義し、課題を整理した上で各レベルに到達するためのステップを1つずつ踏んでいくことが大切です。
本記事でご紹介したもの以外にも、達成したい目的や範囲によってロードマップはさまざまにあります。また、取り組み事例も参考にしながら進めると良いでしょう。
以下の資料では、スマートファクトリーの取り組み事例を紹介しておりますので、ご関心のある方はぜひご覧ください。
お役立ち
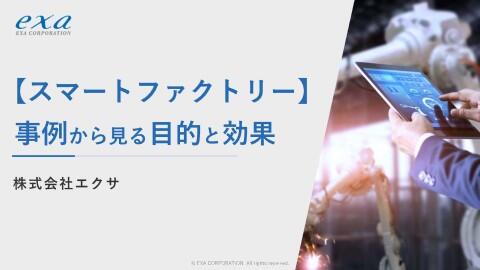
【スマートファクトリー】
事例から見る目的と効果
人材不足や競合となる海外諸国のスマートファクトリーの推進・発展。これらの背景もあり、日本の製造業でも、機械化や自動化を推進し、高品質な製品を安定的に生産するスマートファクトリー化が注目を集めています。
本資料では、目的別のスマート化事例を通して、スマートファクトリーの目的とメリットをご紹介します。
関連する記事
関連ソリューション
関連事例
お問い合わせ
CONTACT
Webからのお問い合わせ
エクサの最新情報と
セミナー案内を
お届けします
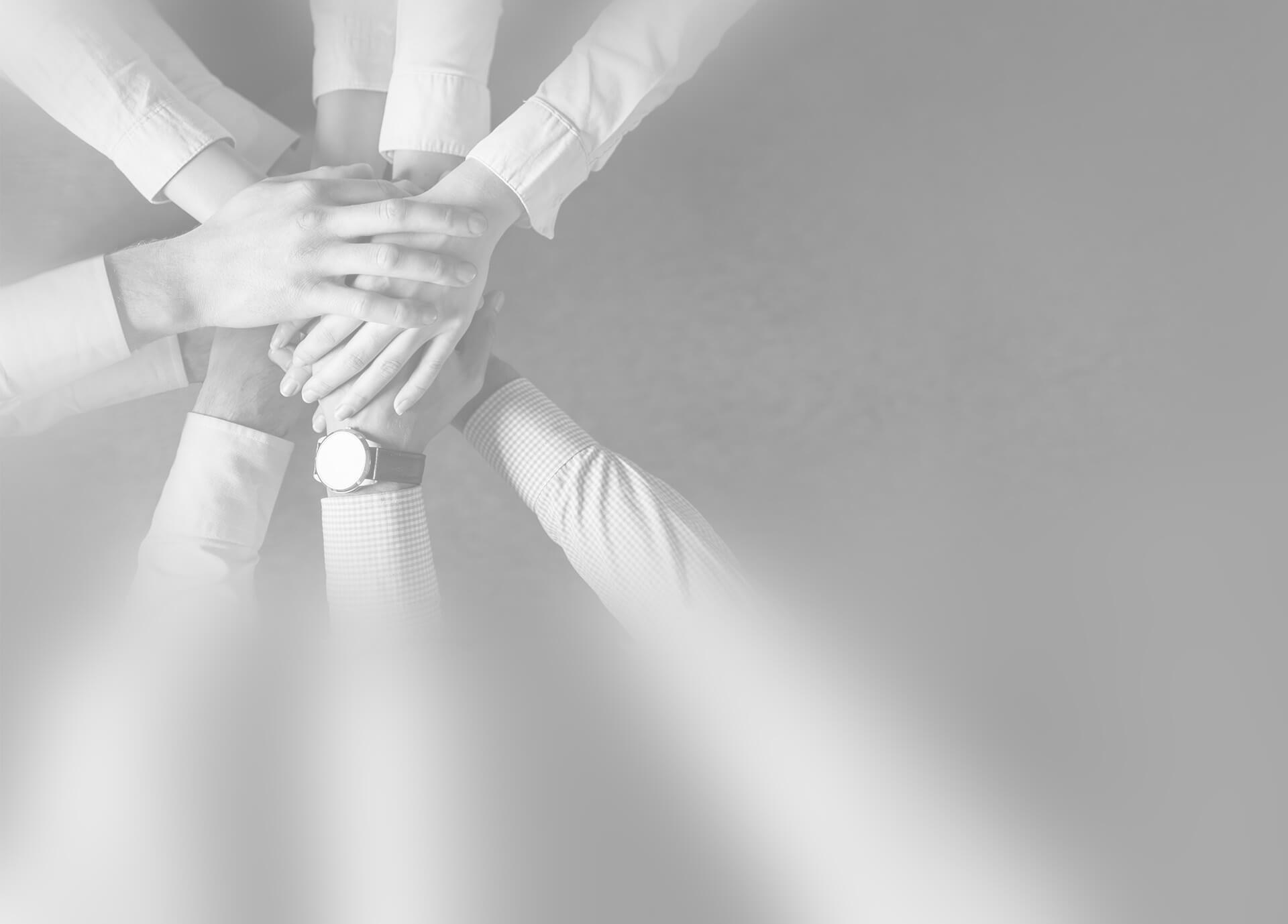