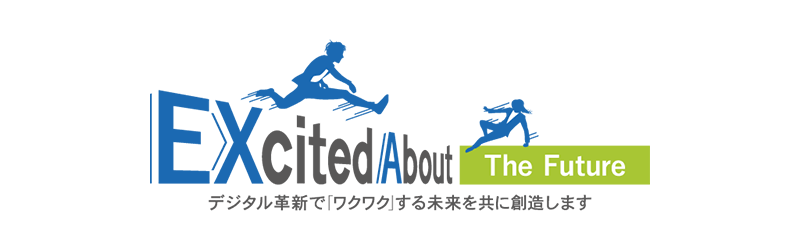
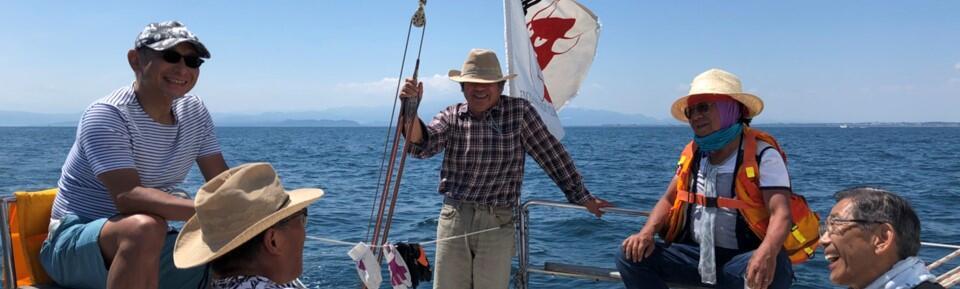
こんにちは。わたしは、PLMのアプリケーションプロフェッショナルとして、長年、製造業のお客様のシステムのご支援をしています。
今回は製造現場を支える実機システムへのデータサイエンス技術適用について、最近の動向を交えながら取り組みの事例をご紹介します。
昨今、製造現場へのデータサイエンス技術の導入が重要になっています。短納期短寿命製品に対応した変種変量生産に適合する業務プロセスの改善は、特に重要な活用シーンです。市場の国際化により消費者ニーズは多様化し、企業間の競争激化も加わって、製品の要求仕様は高度化するとともにライフサイクルも短期化してきました。そのため、短納期短寿命となった高機能で多様な製品を、より高い生産性で製造する要求が高まっています。
この要求はエンドユーザー商品から始まり素材製品にまで及び、対応した生産方式は変種変量生産として定着しています。
変種変量生産とは、多品種少量生産ではなく、市場の動きにダイナミックに連動し少量から大量まで、オーダーが入ればすぐに対応できるフレキシブルな生産方式です。しかし、同一品種の製造繰り返し頻度の低下とともに品種毎の高機能化が進み、製造難度はますます高くなっています。これにより、QCサークルなどの現場活動による製造技能の習熟プロセスや品質改善プロセスで成果を出すことが難しくなっています。
そこで、新しい取り組みとして製造現場への適用が期待されるのが、「データサイエンス技術による人的活動の補完強化(DS-Instrumentality of Human Activity 、以下DS-IHA)」です。
DS-IHAとは、製造プロセスの中核での人が主体となる活動に、AI やデータサイエンスの手法を用いてより高度で優れた意思決定を実現することです。その成功のカギは、データサイエンス技術だけにあるのではなく、導入先の製造現場の理解と協力を取り付けることにあります。
そのためには、データに基づくデータサイエンスと現実とのギャップを埋めていくことが重要になります。
本稿では、DS-IHAの現場適用例として、「某素材メーカ様の熟練計画者の製造順序組み替えノウハウ」をデータサイエンス (以下DS)で補完強化し、現行システムに統合したソリューションを紹介します。
素材製品の製造現場の現状とエクサのデータサイエンスについて
素材製品の製造現場では、短納期で短寿命な高機能製品の変種変量生産の波及による、同一品種の製造繰り返し頻度の低下、品種の高機能化による製造難易度の上昇に加えて、新手順や生産プロセスの律速段階となる大型製造設備の段取り替え作業が増大しています。
これにより、オペレータは多忙になり、生産サイクルタイム中の非生産時間も長くなり、生産効率の改善が限界となっています。生産ラインの全工程を通した製造順序の最適化により、無理無駄を排除した非生産時間の削減が必要となります。
素材産業では、上記に加えて少子高齢化と若年層の素材産業離れに伴う労働力不足が、従来通りの現場活動による品質改善、製造技能の習熟・継承の阻害に拍車をかけています。そのため短納期短寿命、変種変量生産で安定した製造組織の維持・強化と収益改善のため、DSを活用したQCD構造改革(品質・生産性・納期達成率の向上)が不可欠となってきています。
エクサは、製造業向けのPDM /PLM 、BOM といったECMソリューションビジネスとSCM ソリューションビジネスを通じて横断的に多くの製造現場の課題に向き合い、製造プロセスの変革に対応してきました。そこで培われたノウハウ、ICT の総合力、およびSE の多様性が、製造業向けのDS適用の原動力となっています。
製造業の課題解決に取り組む中で、製造プロセスに組み込まれた人的活動をDSにより補完強化できると考え、現場技能の継承と少人数による生産適応力改善の仕組みづくりにいち早く取り組んでいます。またこうした取り組みが、日本の製造現場の空洞化の対策につながると考えています。
DS-IHAソリューションの導入
変種変量生産の現場への業務プロセス改善の新しい取り組みとして、DS-IHAソリューションを製造システムに適用しました。製造プロセスの中核で人が主体となる活動に適用し成功するカギは、現場の納得が得られる方法で良い結果を出すことです。そのためには、製造現場の協力を取り付け、データに基づくDSと現実とのギャップを埋めていくことが重要になります。
DS-IHAの対象は、無理無駄を極力排除する製造順序の組み替えオペレーションです。
このオペレーションには、熟練計画者の技能が要求されます。連続する製品ロット間の品質影響の極少化、製造順に起因するエネルギー損失の最小化、および製造ラインの組み替え段取りの最適化などを複合的に考慮する必要があります。
本ソリューションは、調整可能な製造諸元の推定と製造順序の推定との多段推定のフロー(図1)で実現しました。
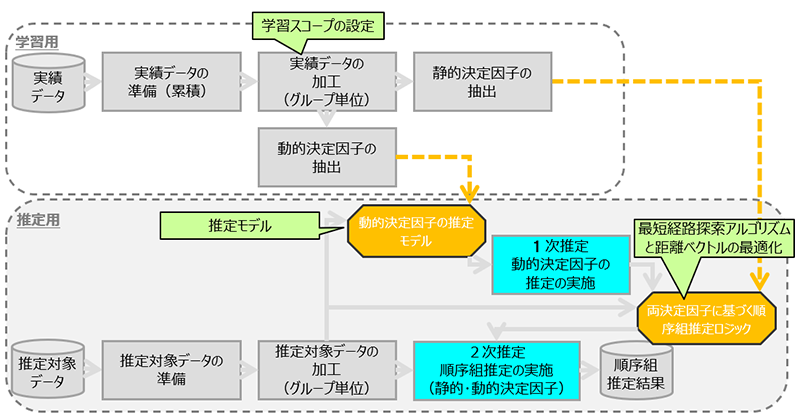
図1 多段推定システム
最初に、対象データを分析し順序組の決定因子を静的決定因子(定数の製造諸元)と動的決定因子(調整可能な製造諸元)に分解します。
動的決定因子は、推定モデル(機械学習)で一次推定します。
次に、この推定された動的決定因子と静的決定因子を用いて順序組を二次推定します。
二次推定では、一次推定された決定因子と各種規制に基づく厳密ルール(形式知)で製品ロットをクラスター化し、クラスター間の連結順序は確定ロジックで求め、クラスター内の順序は熟練者の経験値に基づくファジールール(暗黙知)に対応した推定ロジックを適用します。
推定ロジックには、下記の最短経路探索アルゴリズムから推定精度や処理時間などの適性を考慮して選択します。
- 巡回セールスマン問題(TSP)
- 単一始点最短経路問題(SSSP)
- 全点対最短経路問題(APSP)
最短経路探索アルゴリズムのTSPの適用例としては、上下工程の順序が相互依存関係にある製鉄所の薄板一貫スケジューリング問題の解法(*1)などがあります。
本適用例では、最短経路探索アルゴリズムに、以下の改良を加えました。
- 厳密ルール遵守のため、対象を多階層化し確定ロジックでの逐次処理
- 推定ロジックの精度向上のため、多次元距離ベクトルの最適化処理
特に、多次元距離ベクトルの各要素は、長さ、重さ、温度、時間、成分比等と、単位が異なることから、無次元化し物理的あるいは業務的な意味を考慮した重み付けが必要です。
そこで、その重みの最適化を、各製造段取りグループを1個体と見立て個体群の最適解を求める粒子群最適化(PSO)(図2)ロジックで実現しました(*2)
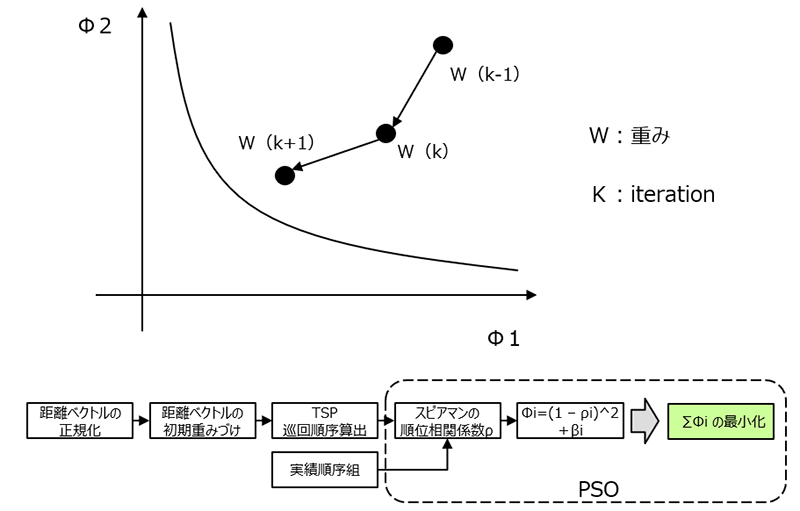
図2 粒子群最適化(PSO)
スピアマンの順位相関係数をベースにした複合評価値を多目的関数とし最適解を導出します。最適化空間の一部次元を取り出した結果を図3に示します。
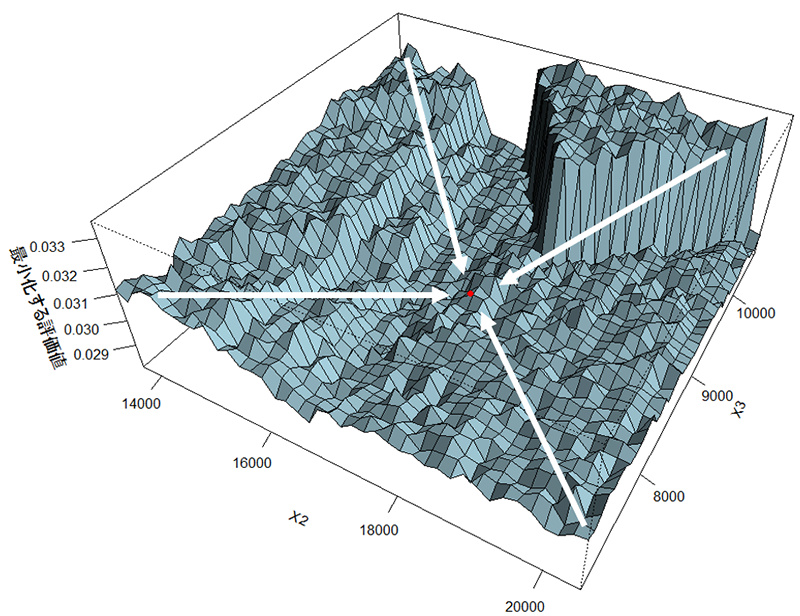
図3 粒子群最適化(PSO)評価値の最小値収束
このソリューションの適用により、製造順序の決定因子として、熟練者が意識しなかった項目も見つかりました。さらに、現場ノウハウの習得を支援する機械チュータとしても運用することができ、現場へのスムーズな浸透と理解を深めるとともに、機械学習用の教師データの補強も期待できます。
組織的受容性の呪縛による課題とその対応について
DS、DX(デジタルトランスフォーメーション) 、AIなどは、ビジネス変革の場でバズワードとして登場して久しいですが、これらの製造現場での活用は、保守保全業務の課題や問題発見、故障予測、品質管理業務での劣化要因の探索と言った、いわゆる製造後のデータマイニングが主流です。製造に直結する製造計画・製造工程業務での活用は、未成熟です。DS-IHAの実現では、安全、安心、および安定にかかわる組織的受容性の呪縛が、主な阻害要因となりました。
最初の「安全」の呪縛とは、熟練技能者では簡単に気付く製造プロセスのリスクを、DSを活用しても完全には察知できないことです。これらリスクデータの確保が不十分(暗黙知)なことや、例外事象の混入が特異点となって結果を不連続にすることも、DSの製造プロセスへの適用の阻害要因です。特に、素材製品の製造現場では、大型設備の予期せぬ故障は大きな損失を招くため、その活用はより慎重になります。
次の「安心」の呪縛とは、多くの機械学習は、非線形予測モデルであり、説明変数との因果関係や重みを可視化できないため、なぜだかうまく行くが論理的な説明ができず安心して利用できないことです。特に、この拒否反応は、理論武装した製造現場で顕著で、DSに基づく解析結果活用の阻害要因となっています。
最後の「安定」の呪縛とは、製品品質や製造設備稼働の安定の保証ができないことです。特定の教師データに対して過学習(オーバーフィッティング)が進むと、教師データに含まれるノイズに反応したり、他の事象への適応力が失われたりします。逆に未学習(アンダーフィッティング)の場合、学習した教師データの範囲外で大きな誤差が発生します。品質や安定稼働を阻害する事象は、管理された現場では発生が稀で未学習となりやすく、管理が不十分な現場では発生が見かけ上周期的になった場合に過学習となり、どちらもシステムの安定性を損ないます。
これら3つの呪縛が、DSの製造プロセスへの普及を阻害しています。
ビジネスへのDS活用は、厳密な理論の公式化より現実に適合することが何より重要です。
製造現場を上述の三つの呪縛から解放するために、データサイエンティストとしては、現象を的確に解明し、現場に受け入れていただくことが重要になります。製造現場の人的活動へのDS適用を通じて対応したことを以下に紹介します。
「安全」では、実績データの外れ値となるサプライチェーンの乱れや保全活動、事故・災害の影響を除外することで、特異値の出現を抑止しました。さらに、重要な規範には、機械学習の推定モデルではなく、推定ロジックを活用しました。
「安心」では、現象のアナロジー展開で製造現場の理解を深めることで対応しました。アナロジー展開は、現場が慣れ親しんだ現象に当てはめることで、理解と共感を促進し、現場の「なぜ」に向き合った納得感のある説明で、新しい技術の導入に対する安心に繋げます。例えば、摩耗故障の予測では、ゴムの経年劣化の硬化による軋み振動のモデルにアナロジー展開することで、機械の劣化予測に適用イメージを共有できます。同じように、製造順序組では、最短経路探索問題などへのアナロジー展開を試み、その有用性のイメージを共有しました。
「安定」では、規範(製造ルール)の改訂を跨る実績データが教師データ内に混在しないようにしました。推定対象の動的因子は、調整可能な有限の選択肢にも関わらず、選択肢以外の外れ値が混入していました。この外れ値は、新製品開発のための実験的試行の場合と入力ミスの場合があります。その試行で製品仕様の許容範囲に収まる結果が得られると、規範が改正され、外れ値ではなくなります。この規範変更情報が、製造情報と連動されていないことが問題要因の一つです。規範が変わると、推定モデルは適合しなくなります。また、新しい規範がオペレータに浸透するのに一定の時間を要することもポイントでした。このような、データや規範の動的な揺らぎが、製造現場での推定モデルを不安定にしています。規範更新周期に基づいた同一規範内を保障する実績データのスコープ、サプライチェーンの乱れや災害などによる異常データフィルターの追加で対応しました。
加えて、オーソドックスですがIPO Diagram を活用して業務プロセスを見える化し、段階的な業務への浸透を計画しました。
実機化でのその他課題
推定精度の評価
製造順序の組み替えオペレーションには唯一の正解がないため、推定結果の精度評価方法の決定が問題となります。
たとえ同じ製造諸元の対象データであっても、教師データとなる実績の製造順序にはオペレータの属人性による揺らぎがあります。そもそもオペレータが組んだ製造順序は、指定の製造条件を満たす製造工程の無理無駄を極力排除した解ではあっても、最善の解である保証はありません。推定結果は、実績と同等あるいは、より優れた未知な解の集合に含まれている可能性があり、適正な評価が難しくなります。推定結果と実績との各種評価手法を用意しましたが、推定モデルとロジックの適正評価には、オペレータによる評価のデータ化が必要でした。
推定精度の向上
製造順序の推定精度を高めるために、ロットごとの製造諸元を単純化し、県と都市(政令指定都市と都市)で構成される多階層構造の都市巡回問題を県単位で逐次処理する最短経路探索問題にアナロジー展開(表1、図4)しました。厳密ルールを順守した推定ロジックを構築し、多次元距離ベクトルの最適化を組み合わせたソリューションすることで精度向上を実現できました。
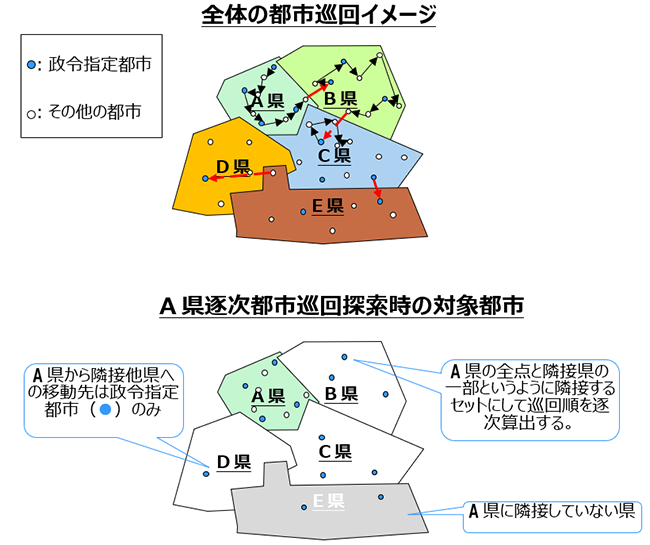
図4 県と都市で構成される多階層構造の巡回問題にアナロジー展開
現実項目 | 置き換え項目 |
---|---|
同一段取りグループ | 県 |
ロット | 都市 |
段取り替え直後慣らし可ロット | 政令指定都市 |
段取り替え直後慣らし不可ロット | 通常都市 |
段取り替え類似グループ | 隣接県 |
ロット間の類似度 | 都市間距離 |
今後の取り組みと将来の展望
今回のケースでは、製造諸元データをベースにした推定にとどまり、製造の品質検査結果の活用には至れませんでした。その他製造プロセスの眠っている有効な情報の活用を図りDS-IHAをさらにブラッシュアップするために、以下の残課題に取り組みたいと考えています。
- DS-IHAソリューションの対象システムへの干渉評価(自己収束、発散)
- オペレータによる、推定製造順序の評価結果のフィードバック
- 製品の品質検査結果のフィードバック
- 教師データのオペレータの個体差の解消
今後は、DS技術を、単に既存システムと連携してデータ収集・分析し業務の改善点の発見に用いるだけではなく、製造プロセスそのものを対象にしたDS-IHAのさらなる発展を目指します。そのために、組織的な受容性を高める活動とともに、以下に取り組みたいと考えています。
- DS-IHAソリューションの他製造プロセスへの適用拡大
- 機械学習と人が相互に影響して生産性を高める仕組み作り
- 自律改善(新たな製品製造プロセスへのフレキシブルな適応)
プライベート紹介
アウトドアで体を動かすことはヒラメキを与えてくれます。モータースポーツとフィジカルスポーツともに効果的です。
学生時代は、SMSC 会員になり鈴鹿サーキットにレース観戦によく行きました。それが高じてモータースポーツにはまり、二輪はレーサーレプリカ仕様、とはいっても四半世紀前から愛用のクラッシックモデルでツーリングを、四輪は真っ赤なスポーツカーでウロチョロと楽しんでいます。
スキーは学生時代から続く冬の娯楽です。
また、社会人になって始めた水泳は、毎年マスターズ大会に出場しています。
45歳からは、トライアスロン、マラソン、オープンウオータースイムと、人生に彩を添えてくれます。
ただ、2年前にスキーで膝を骨折してからは、激しい運動はリハビリ中で、今は縁あって始めたヨットセーリングで海に繰り出しています。江の島を拠点とし東京湾を周遊するのは、とても開放感があり素敵な心持にしてくれます。風向きと潮流を読んで航路を決めるセーリングは、対象を読み解く力、直観力を磨いてくれるようです。コロナ巣籠中は難しいですが、体を動かし血流を良くすることが、ストレス発散、健康維持、そして脳をデフォルトモードにし、アイデアヒラメキの源となります。
多くのことがらに触れ知見を広げるほど、アナロジー展開の引き出しが増え、発見的解決力を培う最良の方法と考えています。「わくわくドキドキ」の体験をしてDS-IHAをさらに展開していきたいと思います。
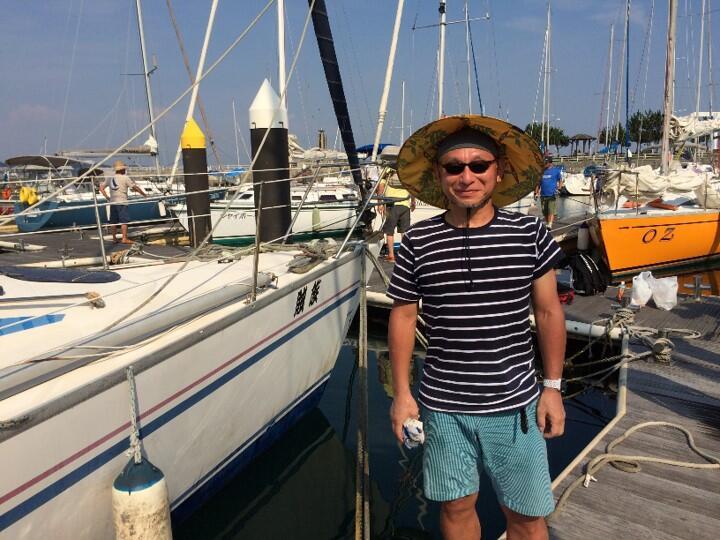
参考文献
(*1) IBM. (2013年4月9日). ビジネス・アナリティクス - 薄板一貫スケジューリング 参照先: https://researcher.watson.ibm.com/researcher/view_group_subpage.php?id=4628
(*2) 斎藤利通. (2011). 粒子群最適化と非線形システム. IEICE Fundamentals Review Vol.5 No.2 pp. 155-161. 参照先: J-Stage: https://www.jstage.jst.go.jp/article/essfr/5/2/5_2_155/_pdf
執筆者紹介
お問い合わせ
CONTACT
Webからのお問い合わせ
エクサの最新情報と
セミナー案内を
お届けします
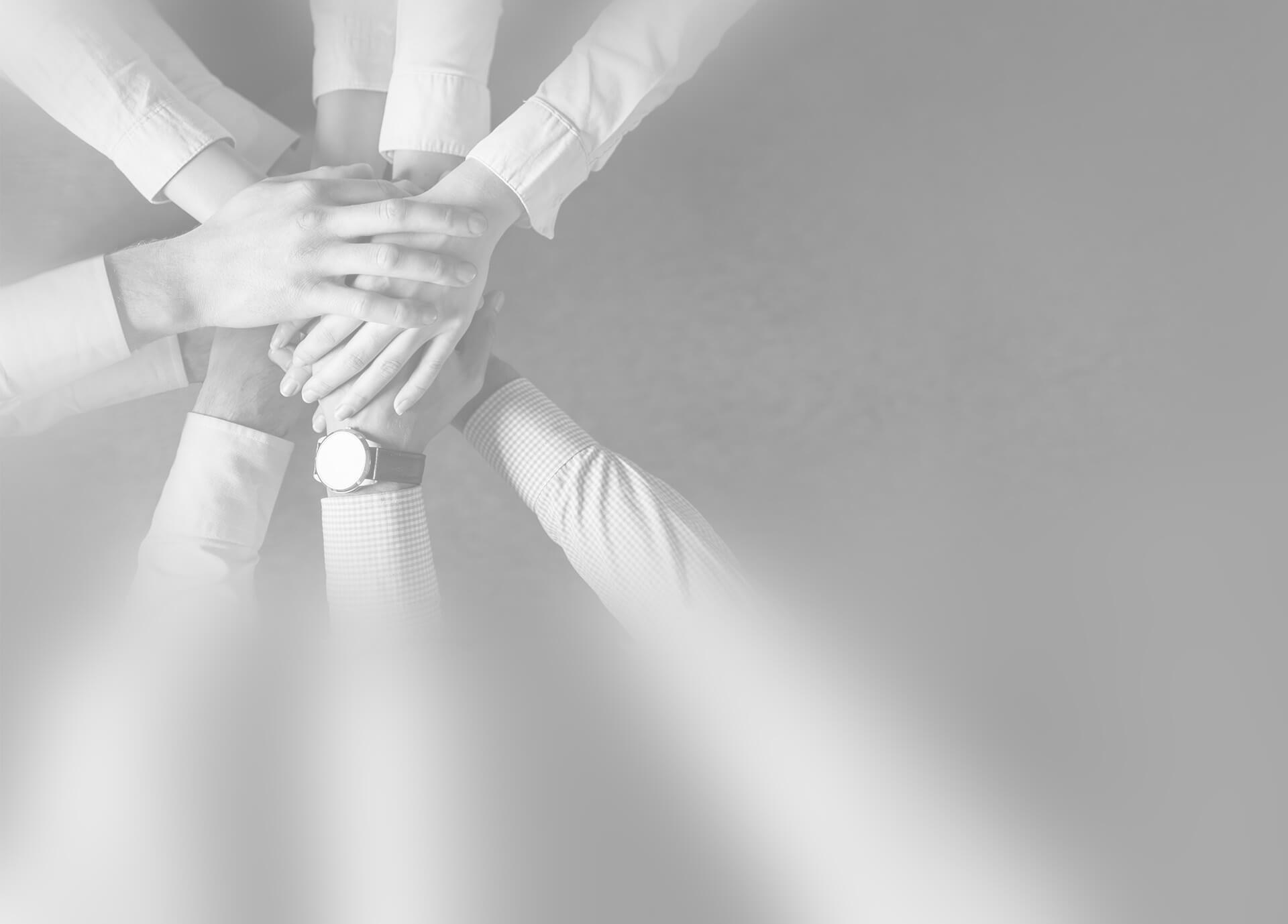